Hypertherm HD4070 Rev.1 User Manual
Page 276
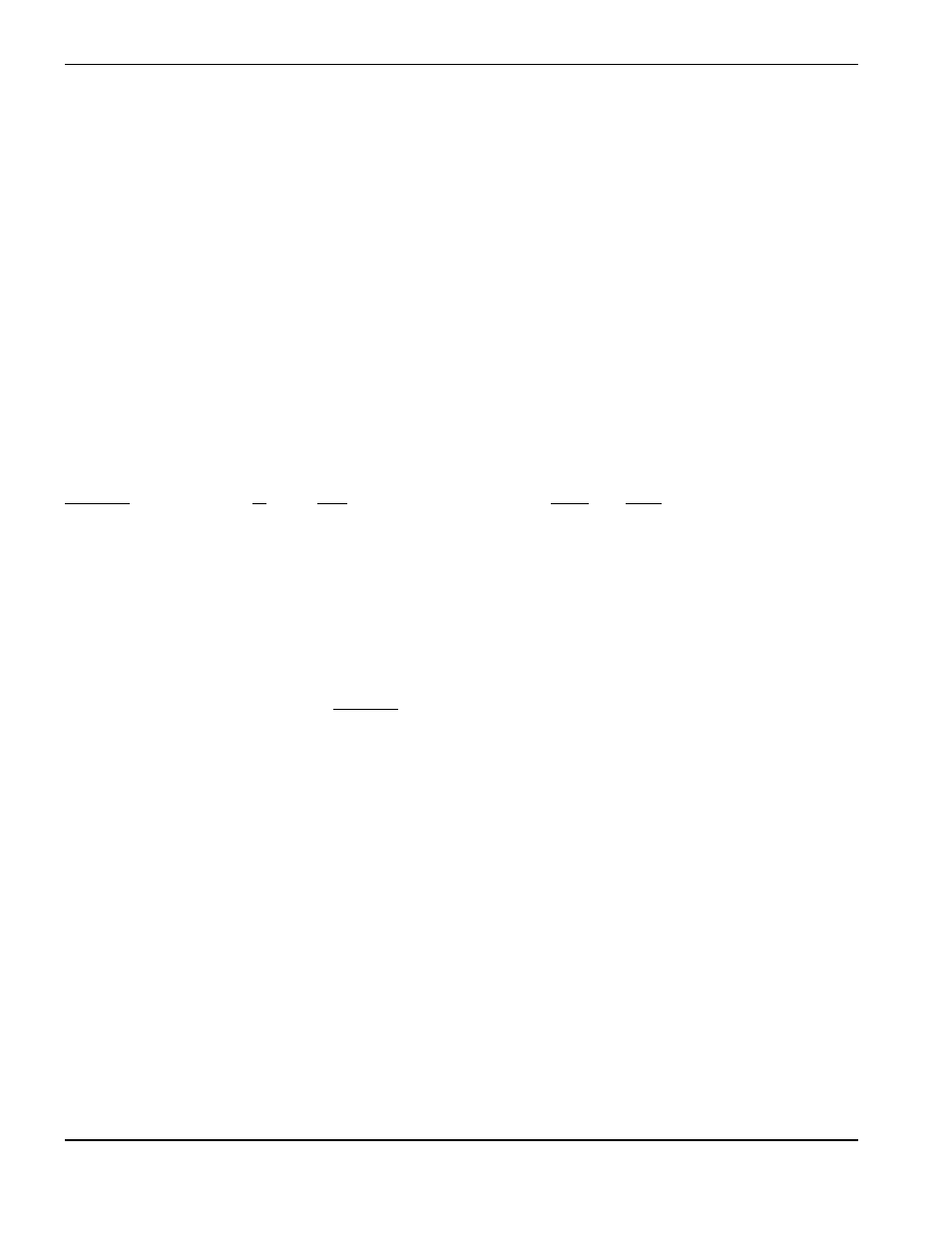
APPENDIX E – COMMAND THC AND CNC SOFTWARE – SUPPLEMENTAL INFORMATION
e-2
HyPerformance HD4070
Instruction Manual
CommandTHC serial protocol
Commands can be sent over a serial link to control the function of the torch height control. The interface is 4 wire
RS422 on the Machine Interface Cable (pins (1) RX-, (20) RX+, (2) TX-, (21) TX+). The serial frame runs at 19200
baud, 8 data bits, 1 stop bit, and no parity. All bytes in a serial message are ASCII characters. A message consists
of a start of message character (>, 0x3E), 2 byte message ID (all message ID’s should be capitalized), variable
length data, 2 byte checksum, and end of message character (<, 0x3C). For example: to put the THC into remote
mode >RM1D0<. ‘RM’ is the message ID, ‘1’ is the data field, and 0xD0 is the checksum (2 hex digits sent as 2
ASCII characters). The response to an accepted command is (^, 0x5E) and the response to an invalid command is
(#, 0x23).
Some of the commands can be queried by using (?, 0x3F) as the data. For example: to query the actual arc
voltage >AV?D6<. The response to this query would be >AV100058<, which represents an actual arc voltage of
100.0 volts with a checksum of 0x58.
Errors can be retrieved over the serial link. There is a discrete output on the machine interface cable (THC Error
pins 14,33) which indicates an error has occurred. Using the command >CL8F< errors can be cleared and
retrieved. A typical response might be >ERR-Motor Current Fault46< or if there is no error (^, 0x5E) is returned.
Command listing:
Command
ID
Data
Query
Notes
Pierce Delay
PD
0 – 9000 (0 to 9.000 seconds)
yes
Delay before motion output
Pierce Height Factor
PH
50 – 300 (50% to 300%)
yes
Used to set pierce height
Preflow During IHS
PF
0,1 (0 = off, 1 = on)
yes
Improves cycle time
IHS Stall Current
SC
1 – 10 (1 = least force)
yes
Used to set stall force
IHS Speed
IV
1 – 10 (1= slowest)
yes
Used to set IHS speed
IHS Test
IH
0,1 (0 = run, 1 = test)
no
Perform IHS test
Nozzle Contact Active
NC
0,1 (0 = off, 1 = on)
yes
Enable nozzle contact IHS
Machine Acceleration
MA
0 – 9000 (0 to 9.000 seconds)
yes
Delay voltage control
Maintenance Mode
MT
No data
no
Maintenance mode
Auto Kerf
AK
0,1 (0 = off, 1 = on)
yes
Disable voltage control in kerf
Actual Arc Voltage
AV
? (query only)
yes
Returned value is 1/10 volts
Automatic Voltage Control
AA
0,1 (0 = manual, 1 = auto)
yes
Voltage control or manual
Retract
RE
0,1 (0 = full, 1 = partial)
yes
Full or partial retract
Retract Distance
RH
0 – 8000 (0 to 8.000 inches)
yes
Must be in partial retract
Remote Mode
RM
0,1 (0 = off, 1 = on)
yes
Must be ON to use serial link
IO Rev
RI
? (query only)
yes
IO revision
RT Rev
RR
? (query only)
yes
Real Time revision
Homing Speed
HS
1 – 10 (1 = slowest)
yes
Home speed
Unit Conversion
UN
0,1 (0 = inches, 1 = metric)
yes
Units
Lifter Test
LT
No data
no
Perform lifter test
Cut Height
CH
0 – 1000 (0 to 1.000 inches)
yes
Used to set cut height
Arc Voltage Set-point
VS
500 – 3000 (50.0 to 300.0 volts)
yes
Used to set voltage control
Step Up
S+
No data
no
Move up fixed increment
Step Down
S-
No data
no
Move down fixed increment
Jog Up
J+
No data
no
Continuous movement up
Jog Down
J-
No data
no
Continuous movement down
Clear Error
CL
No data
no
Clear error, send error string
Flush Buffers
FL
No data
no
Reset RX and TX buffers
Error code
EC
? (query only)
yes
Send error code number