Pecking and tapping – HEIDENHAIN NC 124 User Manual
Page 43
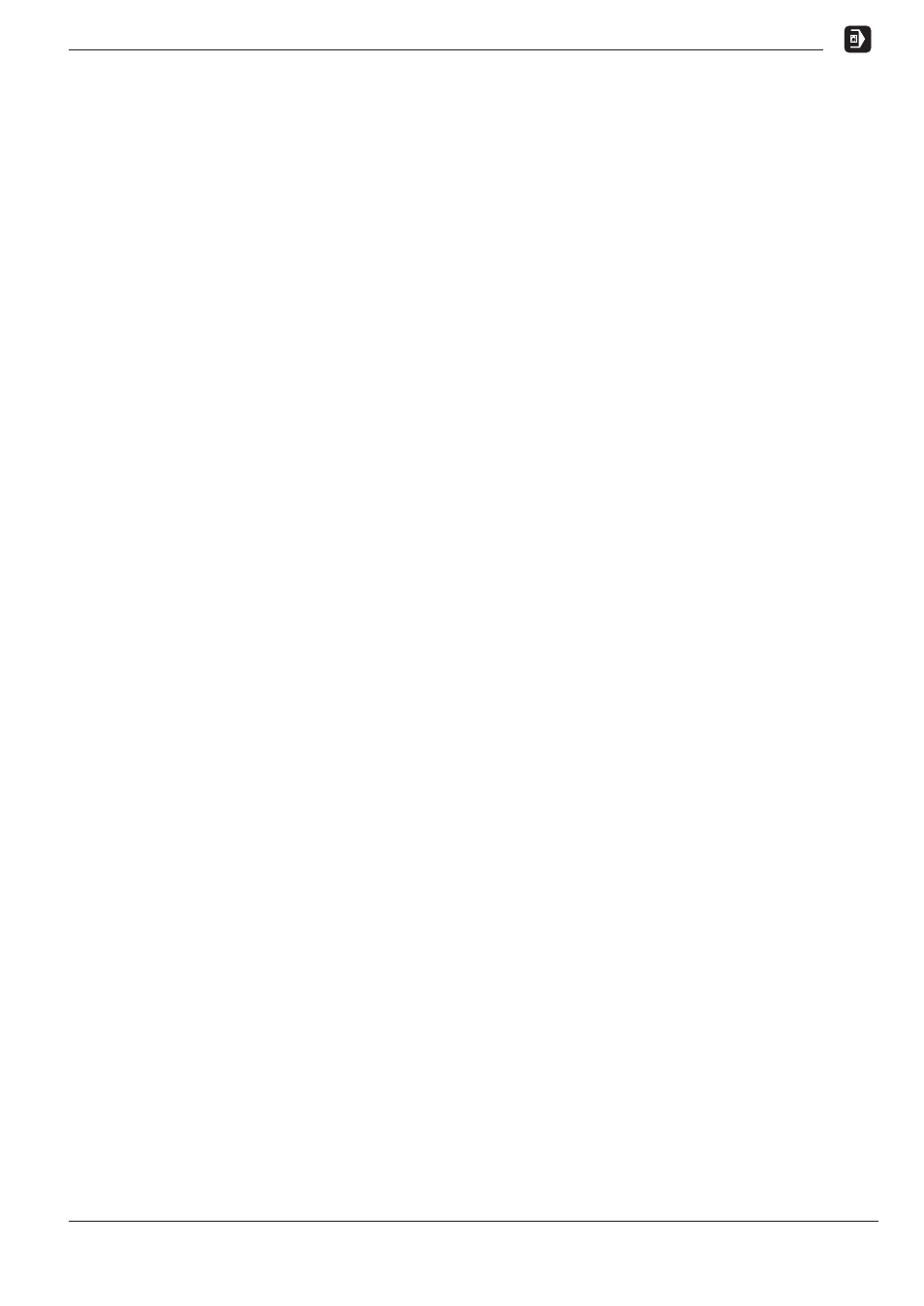
4
Positioning with MDI
TNC 124
43
Pecking and tapping
The TNC cycles for pecking and tapping (see Chapter 7) are available
in the POSITIONING WITH MDI mode of operation.
Use the soft keys on the second soft-key row to select the desired
type of hole and enter the required data. These data can usually be
taken from the workpiece drawing (hole depth, infeed depth, etc.).
The TNC controls the machine tool and calculates additional data
such as the advanced stop distance if the hole is to be drilled in sev-
eral infeeds.
Pecking and tapping in hole patterns
The functions for pecking and tapping are also available in combina-
tion with the hole pattern functions Circle Pattern and Linear Pattern.
Pecking and tapping processes
The input data for pecking and tapping can also be entered as
cycles in a part program. You will find detailed information on how
the TNC controls pecking and tapping operations in Chapter 7. (See
page 79 for pecking and page 82 for tapping).
Pre-positioning the drill for pecking and tapping
Pre-position the drill in the Z axis to a position above the workpiece.
In the X and Y axes (working plane), pre-position the drill to the hole
position. The hole position is approached without radius compensation
(input R0).
Input data for pecking
Clearance height at which the drill can traverse in the working
plane without damaging the workpiece;
Enter an absolute value together with the algebraic sign.
Setup clearance at which the drill is located above the work-
piece.
Coordinate of the workpiece surface;
Enter an absolute value together with the algebraic sign.
Hole depth; the algebraic sign determines the working direction.
Infeed depth
Dwell time of the drill at the bottom of the hole.
Machining feed rate
Input data for tapping
Clearance height at which the drill can traverse in the working
plane without damaging the workpiece;
Enter an absolute value together with the algebraic sign.
Setup clearance at which the drill is located above the work-
piece.
Coordinate of the workpiece surface;
Enter an absolute value together with the algebraic sign.
Hole depth; the algebraic sign determines the working direction.
Dwell time of the drill at the end of thread.
Machining feed rate