Yaskawa MotionWorks IEC Hardware User Manual
Page 41
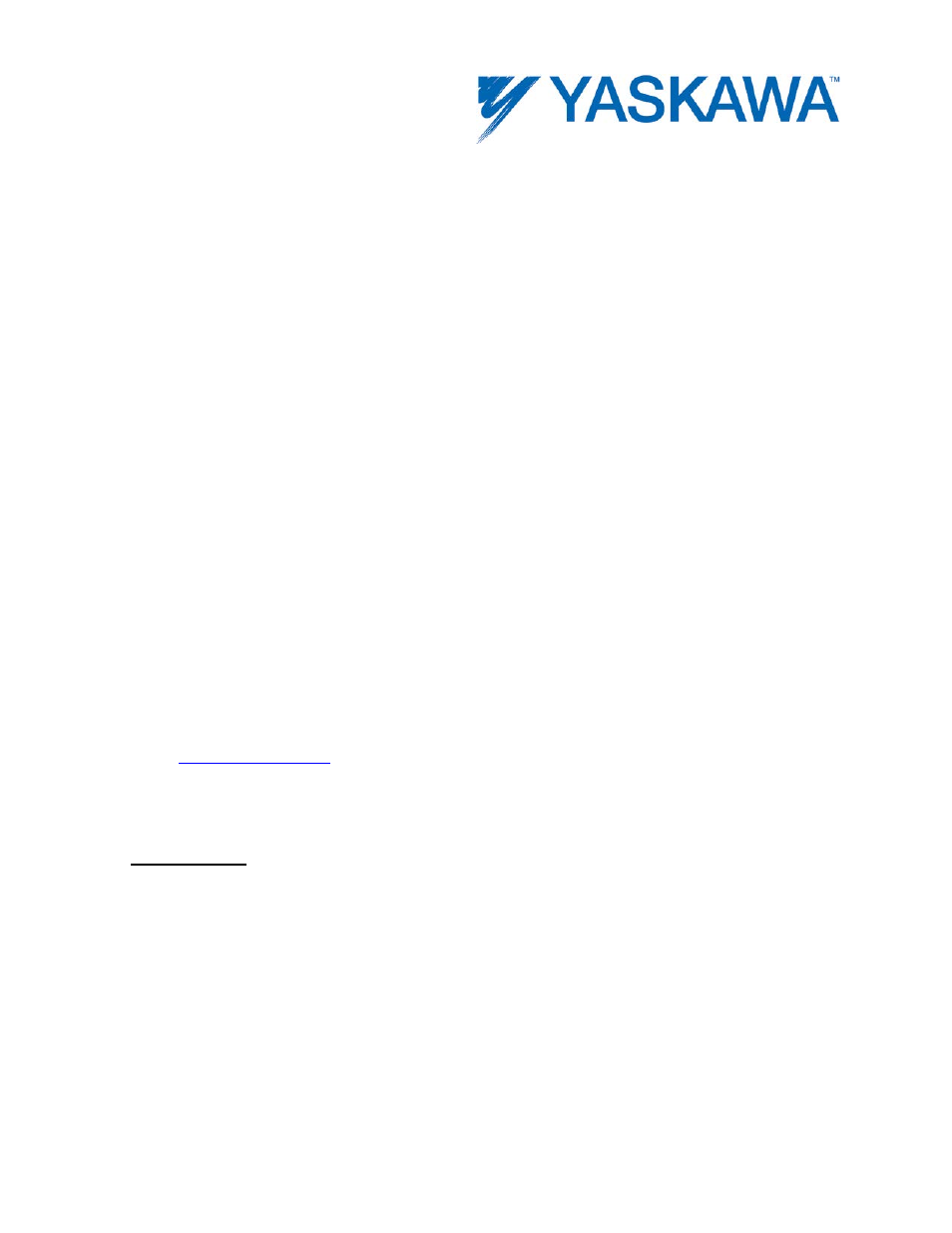
MotionWorks IEC Hardware Configuration – 2013-03-26
38
4. Increase Pn51B , the allowable deviation between motor and load
positions that will trigger an alarm. The proper value is application
dependant.
5. Set Pn22A.3 = 0 (Use motor encoder speed for speed feedback
(Recommended.)
NOTES:
Yaskawa recommends selecting an encoder resolution that closely matches
the encoder counts per user unit of the Sigma-5 servo. (Less than 20:1
pulse count difference.) High resolution will improve the effectiveness of
the powerful auto-tuning algorithms in the Sigma-5 Servopack.
The MPiec controller forces the electronic gear ratio (Pn20E and Pn210) to
be unity (1:1). Use the Gear Ratio values on the Configuration tab as
shown below.
Please refer to the Sigma-5 manual for details about individual Servopack
Pns:
Example 1:
Assume a ball screw system with a lead of 120 mm. There is gear
reduction of 9:1, and the external encoder sine wave pitch = 20 um.
Pn20A = (120mm/1 rev of gearbox) x (1rev of gearbox / 9 rev of motor) x
(pitch / 0.02 mm) = 667 pitch / rev.
The configuration settings for this example are shown in the figure below.