Tips for table and torch -13, Error code troubleshooting – 2 of 8 -8 – Hypertherm HSD130 HySpeed Plasma User Manual
Page 154
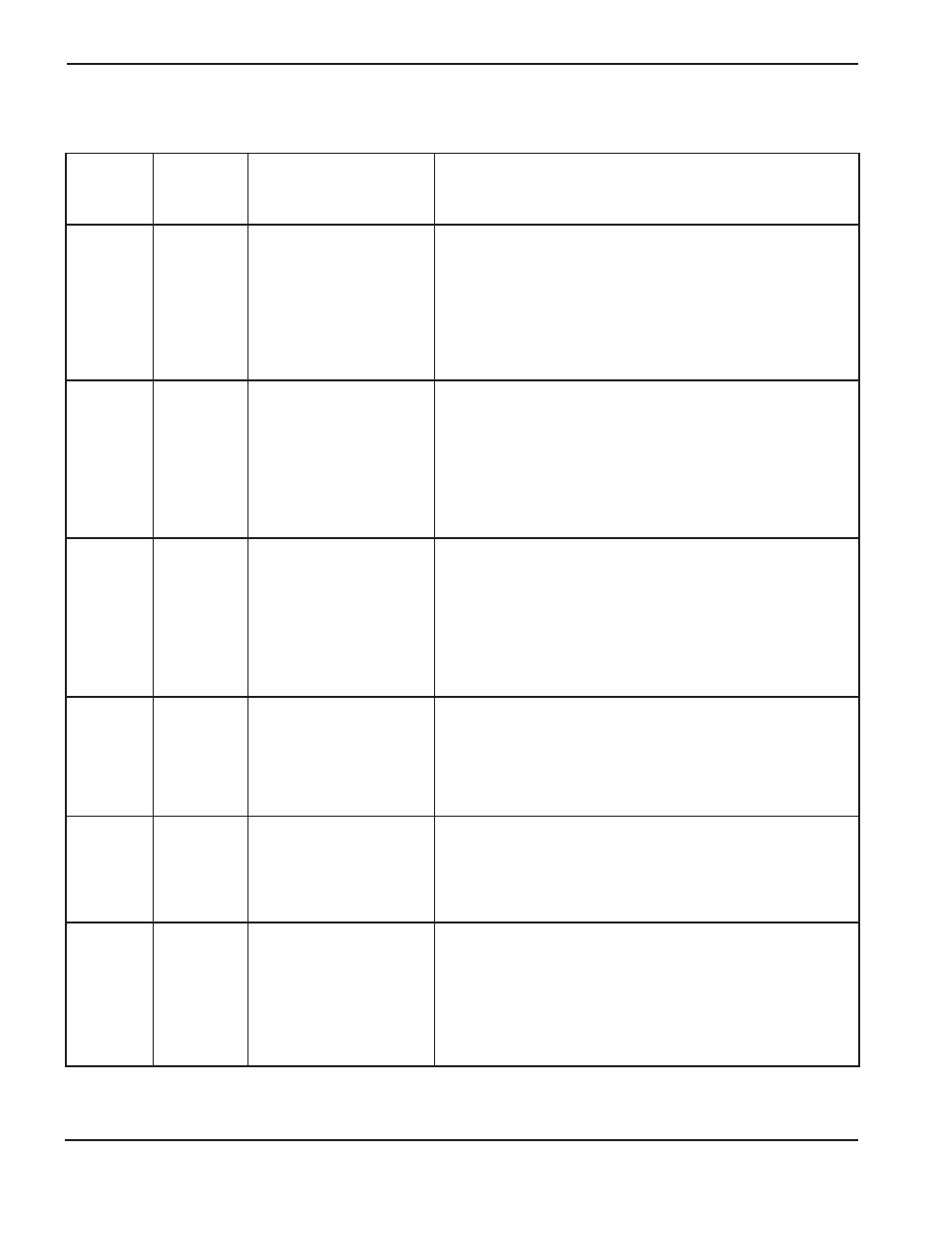
MAINTENANCE
5-8
HySpeed HSD130 RHF
Instruction Manual
Error code troubleshooting (2 of 8)
Error code
number
Name
Description
Corrective action
026
Lost transfer
After transfer lost the
transfer signal. The signal
is < 3.5 amps.
1. Verify that the consumable parts are in good condition.
2. Verify proper gas settings.
3. Verify pierce delay time.
4. Verify that the arc did not lose contact with plate while
cutting (hole cutting, scrap cutting, etc).
5. Inspect work lead for damage or loose connections.
6. Try connecting work lead directly to the plate.
7. Perform chopper test (see Maintenance section).
027
Lost phase
Phase imbalance to
chopper after contactor
engaged or while cutting.
1. Verify phase-to-phase voltage to power supply.
2. Disconnect power to power supply, remove cover on
contactor, and inspect contacts for excessive wear.
3. Inspect the power cord, contactor, and input to chopper for
loose connections.
4. Inspect the phase-loss fuses on the power distribution
board (PCB3). Replace board if fuses are blown.
5. Perform phase-loss test (see Maintenance section).
031
Start loss
Start signal was received
and then lost before an arc
was established.
1. If a mechanical relay is being used to provide the HSD with
a start signal, this relay is either bouncing when activated or
the contacts are faulty. Replace the relay.
2. Inspect interface cable for damage; faulty crimps, or poor
electrical connections.
3. If interface cable is good and a relay is not driving the start
input, the CNC is dropping the start signal before a steady
state arc has been established.
032
Hold timeout
Hold signal was active for
longer than 60 seconds.
1. Check the interface cable for damage. The hold wires may
be short-circuiting inside.
2. The CNC is maintaining this input, it could be waiting for an
IHS complete input from another torch.
3. If CNC interface cable is good and it is a one-torch system,
change PCB4.
035
Low preflow
pressure
Preflow gas pressure
under lower limit of
0.4 bar (5 psi).
1. Put the selection switch in the SET position. The 3-digit LED
shows the preflow supply pressure. The pressure reading
should be between 6.2 bar and 8.3 bar (90 psi and 120 psi).
2. Verify that the Burkart valve is functioning properly.
042
Nitrogen gas
purge error
Low or no nitrogen
pressure during purge.
Purge occurs when
switching from a fuel gas
process to an oxygen or air
process.
1.Verify that the nitrogen supply is turned on, and inspect gas
supply pressure and volume of gas remaining in supply tanks.
2. Verify that the gas regulator is set to 7.2 bar (105 psi). See
Setting the supply regulators (Installation section).