Hypertherm HSD130 HySpeed Plasma User Manual
Page 188
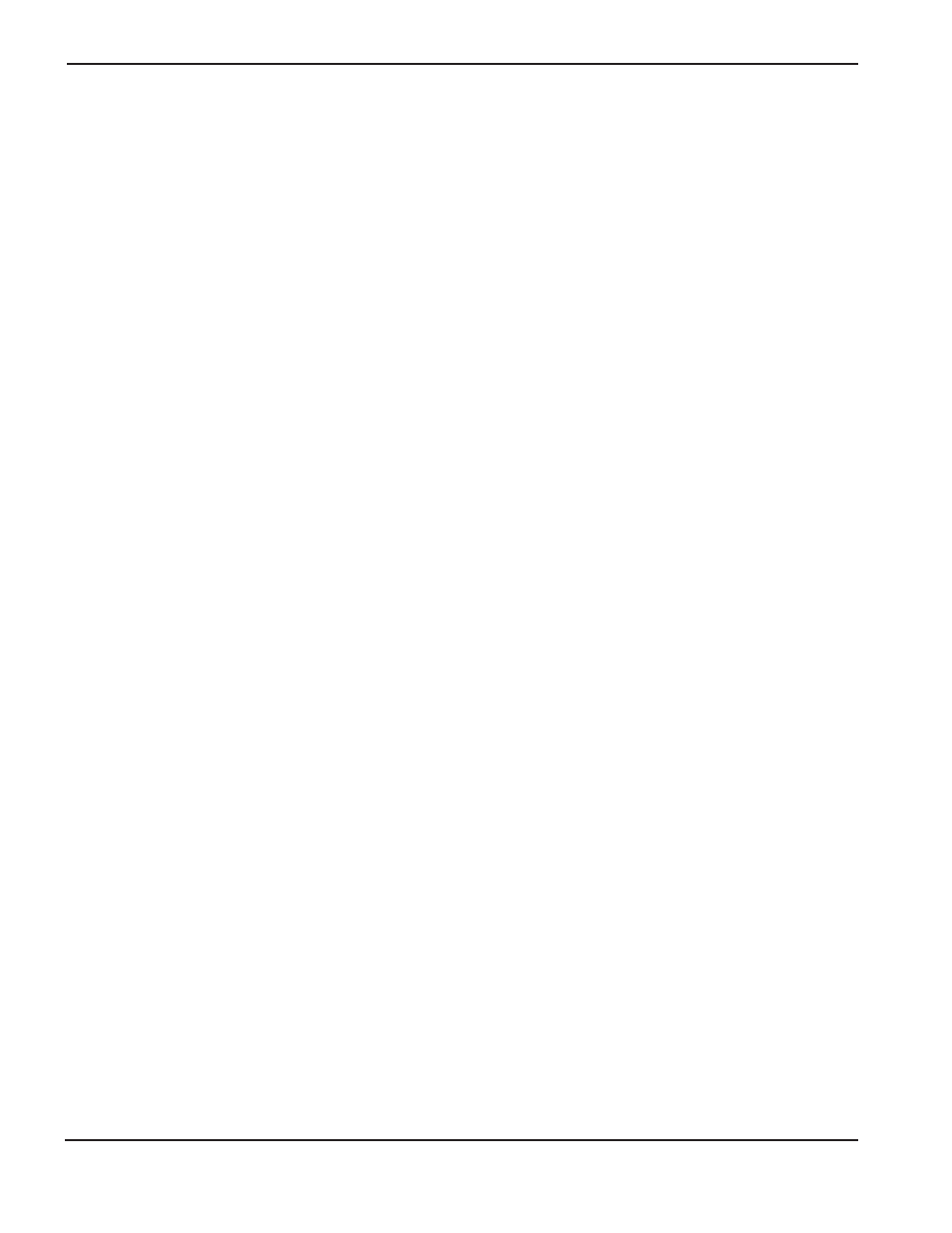
MAINTENANCE
5-42
HySpeed HSD130 RHF
Instruction Manual
Cooling system
4. Inspect the coolant-circulating system’s filter element at the rear of the power supply. If the filter is a brownish color,
replace it. Consult the Parts List in this manual for part numbers.
5. Perform a coolant flow test as described in this manual, then check for coolant leaks. Primary locations to inspect
are these:
A. The back of the power supply;
B. At the ignition console; and
C. At the torch main body.
Also, check the coolant tank for dirt and particulates. Verify that proper Hypertherm coolant is being used. Proper
Hypertherm coolant (028872) is a red liquid.
Torch main body
6. Verify that the water tube is straight and has no pitting on the end.
7. Clean all threads on the front end of the torch head with hydrogen peroxide and a cotton swab, pipe cleaner or
clean cloth. Do not use alcohol. Damage to the threads usually results from not cleaning the torch and retaining cap
threads properly, so that dirt and particulates accumulate in the threads.
8. Inspect the torch insulator for cracks. Replace the torch if you find cracks.
9. Inspect all o-rings on the torch body and consumables. Make sure that the correct amount of lubricant, a thin film, is
applied to these o-rings. Too much lubricant may obstruct gas flows.
10. Check that the retaining or shield cap is tightened securely to the torch main body.
11. Inspect all hose fittings at the rear of the torch for wear. Damage to the fitting threads may indicate that
overtightening has occurred.
12. Check that all connections between the torch and torch leads are tight, but do not overtighten. See torque specs in
the Installation section of this manual.
When removing consumables, always place them on a clean, dry, oil-free surface, since dirty consumables may cause
the torch to malfunction.
Gas flows
13. Check each gas line from the gas supply, as follows:
A. Remove and plug the inlet gas fitting at the gas console.
B. Pressurize the O
2
gas line to 8.3 bar (120 psi) and the air gas line to 7.2 bar (105 psi).
C. Close the gas supply valve at the source. Watch for a pressure drop. If the gas supply line is a hose, there may
be a 0.3 to 0.5 bar (5 to 7 psi) drop due to hose-stretch.
D. Repeat for each line from a gas supply source. If any pressure continues to drop, find the leak within the system.