Hypertherm HD3070 Plasma Arc Cutting System w/ Automatic Gas Console User Manual
Page 154
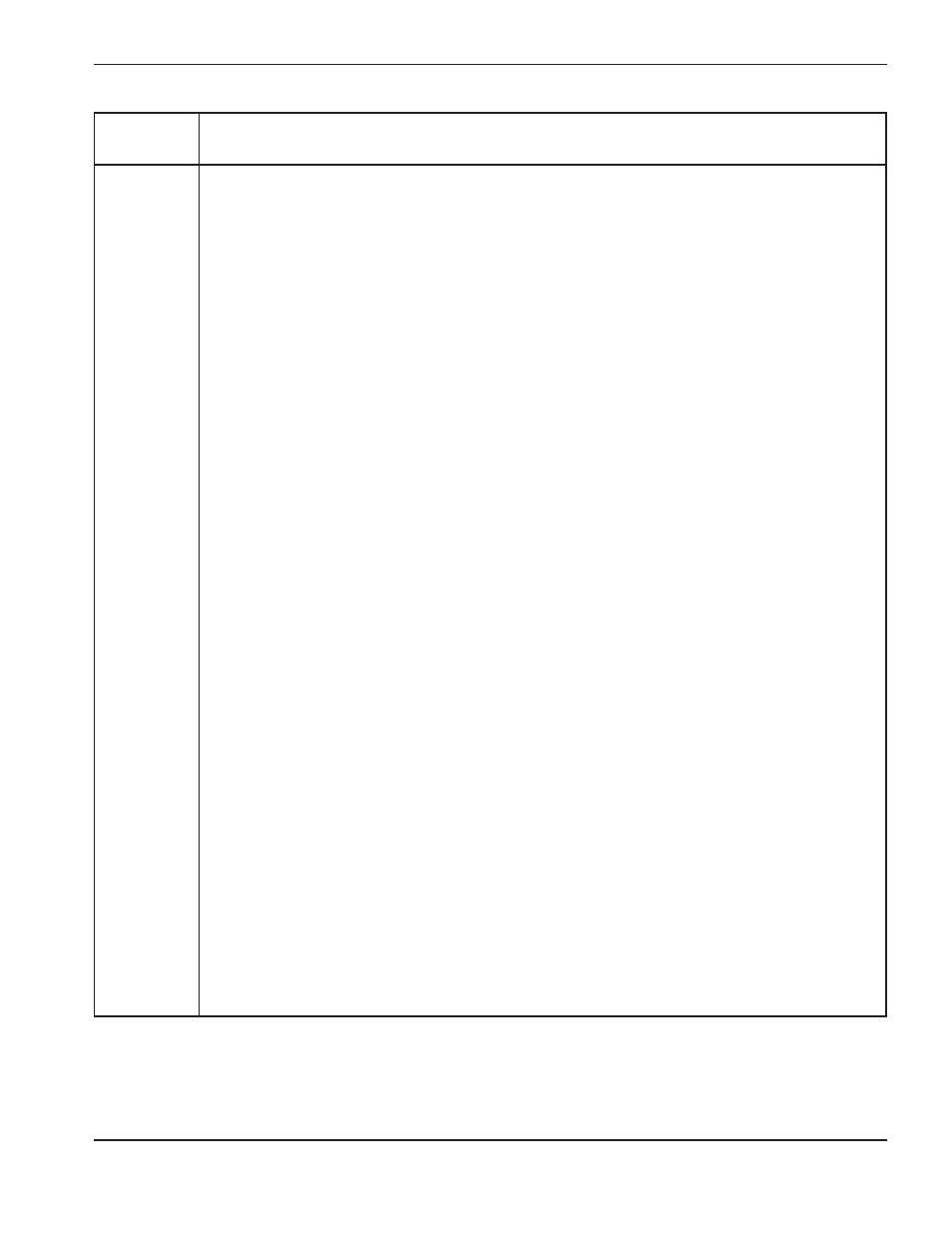
HD3070 with Automatic Gas Console
Instruction Manual
5-29
16
MAINTENANCE
Number
of Blinks
Description
4**
Indicate that the high frequency was unable to ignite the pilot arc within 1 second. Check gas
flows and corresponding pressures.
5**
Indicate that the PIERCE COMPLETE signal was not received within 4 seconds after the
transfer signal.
6**
Indicate that the transfer of the arc to the workpiece was not sensed within 2 seconds of torch
ignition. Check ground clamp to workpiece. Initial torch height may be too high. This will reduce
nozzle life.
7*
Indicate that the arc was extinguished after current transferred to the workpiece, but before
steady-state operation. The pierce delay may have been too long, and after arc transfer, too
much metal was blown away before the X-Y machine moved, leaving the arc no place to
transfer to.
8*
Indicate that the arc was lost during steady-state operation. Typically, this error is caused by
running the torch off the edge of the plate or by having the cut piece fall out leaving the arc no
metal to transfer to.
9*
Indicate that during steady-state operation the measured arc voltage exceeded the
programmed maximum. The torch to work distance was too high during a cut, consequently the
power supply terminated the arc. Check arc voltage setting and that the torch height control
(THC) is working properly.
10*
Indicate that the arc was lost during current ramp down, but before the programmed ramp down
time has elapsed. After the start signal was removed from the power supply, it began to ramp
down, but did not complete it. The most probable cause is by cutting parts that fall out, leaving
the arc no metal to transfer to while the power supply is trying to ramp down. This problem can
be improved, if not eliminated, by changing the CNC program. Try different leadouts for different
shape cuts.
Note:
7,8,9, or 10 blinks in sequence indicate errors that can reduce consumable life, and
cause cut quality to erode prematurely.
12**
Indicate that the software has an error. If this error occurs, there is a fatal error in the
microprocessor chip and it must be replaced.
13
Indicate that the phase loss protection circuit has shutdown the system due to voltage phase
loss or input voltage dropping below 80% of nominal.
*
These errors will also cause the error counter of the timer/counter to increment.
** These errors will also cause an error count output signal to the CNC.