Yaskawa Sigma-5 Large Capacity Users Manual: Design and Maintenance-Rotary Motors-Analog Voltage and Pulse Train Reference User Manual
Series, Ac servo drives
Advertising
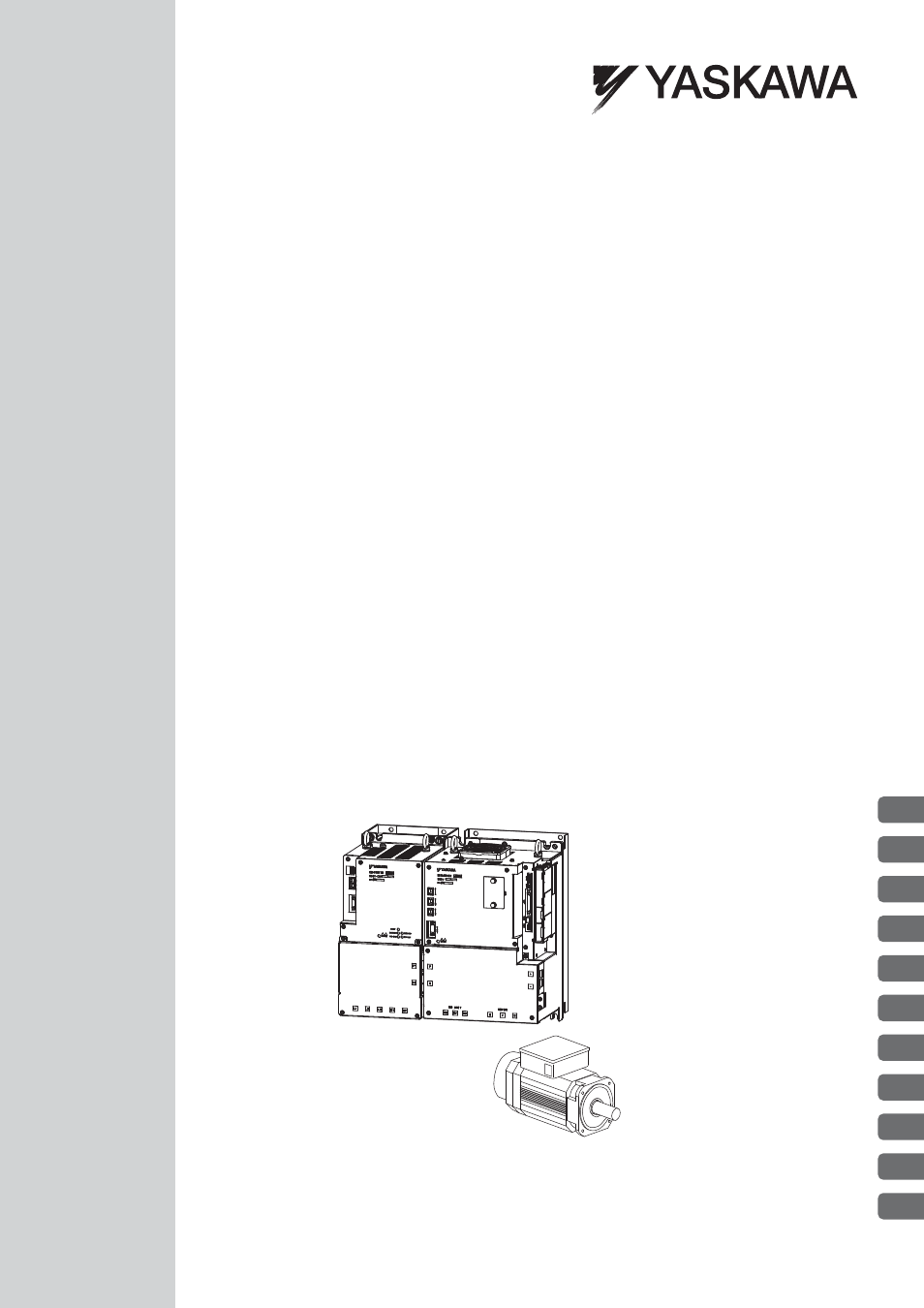
MANUAL NO. SIEP S800000 88D
Outline
Panel Operator
Wiring and Connection
Trial Operation
Operation
Adjustments
Utility Functions (Fn
)
Monitor Displays (Un
)
Fully-closed Loop Control
Troubleshooting
Appendix
1
2
3
4
5
6
7
8
9
10
11
SGDV-
H, -J SERVOPACK
SGDV-COA Converter
SGMVV Servomotor
Rotational Motor
Analog Voltage and Pulse Train Reference
Σ
-
V
Series
AC Servo Drives
USER’S MANUAL
For Use with Large-Capacity Models
Design and Maintenance
Advertising
Table of contents
Document Outline
- Front Cover
- About this Manual
- Safety Precautions
- Warranty
- Harmonized Standards
- Contents
- 1 Outline
- 1.1 Sigma-V Large-Capacity SERVOPACKs and Converters
- 1.2 SERVOPACK Part Names
- 1.3 Converter Part Names
- 1.4 Ratings and Specifications
- 1.5 SERVOPACK and Converter Internal Block Diagrams
- 1.6 Examples of Servo System Configurations
- 1.7 SERVOPACK Model Designation
- 1.8 Converter Model Designation
- 1.9 Combinations of Servomotors, SERVOPACKs, and Converters
- 1.10 Inspection and Maintenance
- 2 Panel Operator
- 3 Wiring and Connection
- 3.1 Main Circuit Wiring
- 3.2 Connecting the Converter to the SERVOPACK
- 3.3 I/O Signal Connections
- 3.4 I/O Signal Allocations
- 3.5 Examples of Connection to Host Controller
- 3.6 Encoder Connection
- 3.7 Selecting and Connecting a Regenerative Resistor Unit
- 3.8 Selecting and Connecting a Dynamic Brake Unit
- 3.9 Noise Control and Measures for Harmonic Suppression
- 4 Trial Operation
- 4.1 Inspection and Checking before Trial Operation
- 4.2 Trial Operation for Servomotor without Load
- 4.3 Trial Operation for Servomotor without Load from Host Reference
- 4.4 Trial Operation with the Servomotor Connected to the Machine
- 4.5 Trial Operation of Servomotor with Brakes
- 4.6 Test Without Motor Function
- 5 Operation
- 5.1 Control Method Selection
- 5.2 Basic Functions Settings
- 5.2.1 Servo ON Signal
- 5.2.2 Servomotor Rotation Direction
- 5.2.3 Overtravel
- 5.2.4 Holding Brakes
- 5.2.5 Stopping Servomotors after /S-ON Turned OFF or Alarm Occurrence
- 5.2.6 Instantaneous Power Interruption Settings
- 5.2.7 SEMI F47 Function (Torque Limit Function for Low DC Power Supply Voltage for Main Circuit)
- 5.2.8 Setting Motor Overload Detection Level
- 5.3 Speed Control
- 5.4 Position Control
- 5.5 Torque Control
- 5.6 Internal Set Speed Control
- 5.7 Combination of Control Methods
- 5.8 Limiting Torque
- 5.9 Absolute Encoders
- 5.10 Other Output Signals
- 5.11 Safety Function
- 6 Adjustments
- 6.1 Type of Adjustments and Basic Adjustment Procedure
- 6.2 Tuning-less Function
- 6.3 Advanced Autotuning (Fn201)
- 6.4 Advanced Autotuning by Reference (Fn202)
- 6.5 One-parameter Tuning (Fn203)
- 6.6 Anti-Resonance Control Adjustment Function (Fn204)
- 6.7 Vibration Suppression Function (Fn205)
- 6.8 Additional Adjustment Function
- 6.9 Compatible Adjustment Function
- 7 Utility Functions (Fn***)
- 7.1 List of Utility Functions
- 7.2 Alarm History Display (Fn000)
- 7.3 JOG Operation (Fn002)
- 7.4 Origin Search (Fn003)
- 7.5 Program JOG Operation (Fn004)
- 7.6 Initializing Parameter Settings (Fn005)
- 7.7 Clearing Alarm History (Fn006)
- 7.8 Offset Adjustment of Analog Monitor Output (Fn00C)
- 7.9 Gain Adjustment of Analog Monitor Output (Fn00D)
- 7.10 Automatic Offset-Signal Adjustment of the Motor Current Detection Signal (Fn00E)
- 7.11 Manual Offset-Signal Adjustment of the Motor Current Detection Signal (Fn00F)
- 7.12 Write Prohibited Setting (Fn010)
- 7.13 Servomotor Model Display (Fn011)
- 7.14 Software Version Display (Fn012)
- 7.15 Resetting Configuration Errors in Option Modules (Fn014)
- 7.16 Vibration Detection Level Initialization (Fn01B)
- 7.17 Display of SERVOPACK and Servomotor ID (Fn01E)
- 7.18 Display of Servomotor ID in Feedback Option Module (Fn01F)
- 7.19 Origin Setting (Fn020)
- 7.20 Software Reset (Fn030)
- 7.21 EasyFFT (Fn206)
- 7.22 Online Vibration Monitor (Fn207)
- 8 Monitor Displays (Un***)
- 9 Fully-closed Loop Control
- 9.1 System Configuration and Connection Example for SERVOPACK with Fully-closed Loop Control
- 9.1.1 System Configuration
- 9.1.2 Internal Block Diagram of Fully-closed Loop Control
- 9.1.3 Serial Converter Unit
- 9.1.4 Example of Connections to External Encoders
- 9.1.5 Encoder Output Pulse Signals from SERVOPACK with an External Encoder by Renishaw plc
- 9.1.6 Precautions When Using an External Incremental Encoder by Magnescale
- 9.2 SERVOPACK and Converter Startup Procedure
- 9.3 Parameter Settings for Fully-closed Loop Control
- 9.3.1 Motor Rotation Direction
- 9.3.2 Sine Wave Pitch (Frequency) for an External Encoder
- 9.3.3 Setting Encoder Output Pulses (PAO, PBO, and PCO)
- 9.3.4 External Absolute Encoder Data Reception Sequence
- 9.3.5 Electronic Gear
- 9.3.6 Alarm Detection
- 9.3.7 Analog Monitor Signal
- 9.3.8 Speed Feedback Method during Fully-closed Loop Control
- 9.1 System Configuration and Connection Example for SERVOPACK with Fully-closed Loop Control
- 10 Troubleshooting
- 11 Appendix
- 11.1 Connection to Host Controller
- 11.1.1 Connection to MP2200/MP2300 Motion Module SVA-01
- 11.1.2 Connection to MP920 Servo Module SVA-01A
- 11.1.3 Connection to OMRON’s Motion Control Unit
- 11.1.4 Connection to OMRON’s Position Control Unit
- 11.1.5 Connection to MITSUBISHI’s AD72 Positioning Module (SERVOPACK in Speed Control)
- 11.1.6 Connection to MITSUBISHI’s AD75 Positioning Module (SERVOPACK in Position Control)
- 11.1.7 Connection to MITSUBISHI’s QD75Do Positioning Module (SERVOPACK in Position Control)
- 11.2 List of Parameters
- 11.3 List of Monitor Displays
- 11.4 Parameter Recording Table
- 11.1 Connection to Host Controller
- Index
- Revision History
- Back Cover