11 safety function, 1 hard wire base block (hwbb) function, 1) risk assessment – Yaskawa Sigma-5 Large Capacity Users Manual: Design and Maintenance-Rotary Motors-Analog Voltage and Pulse Train Reference User Manual
Page 202
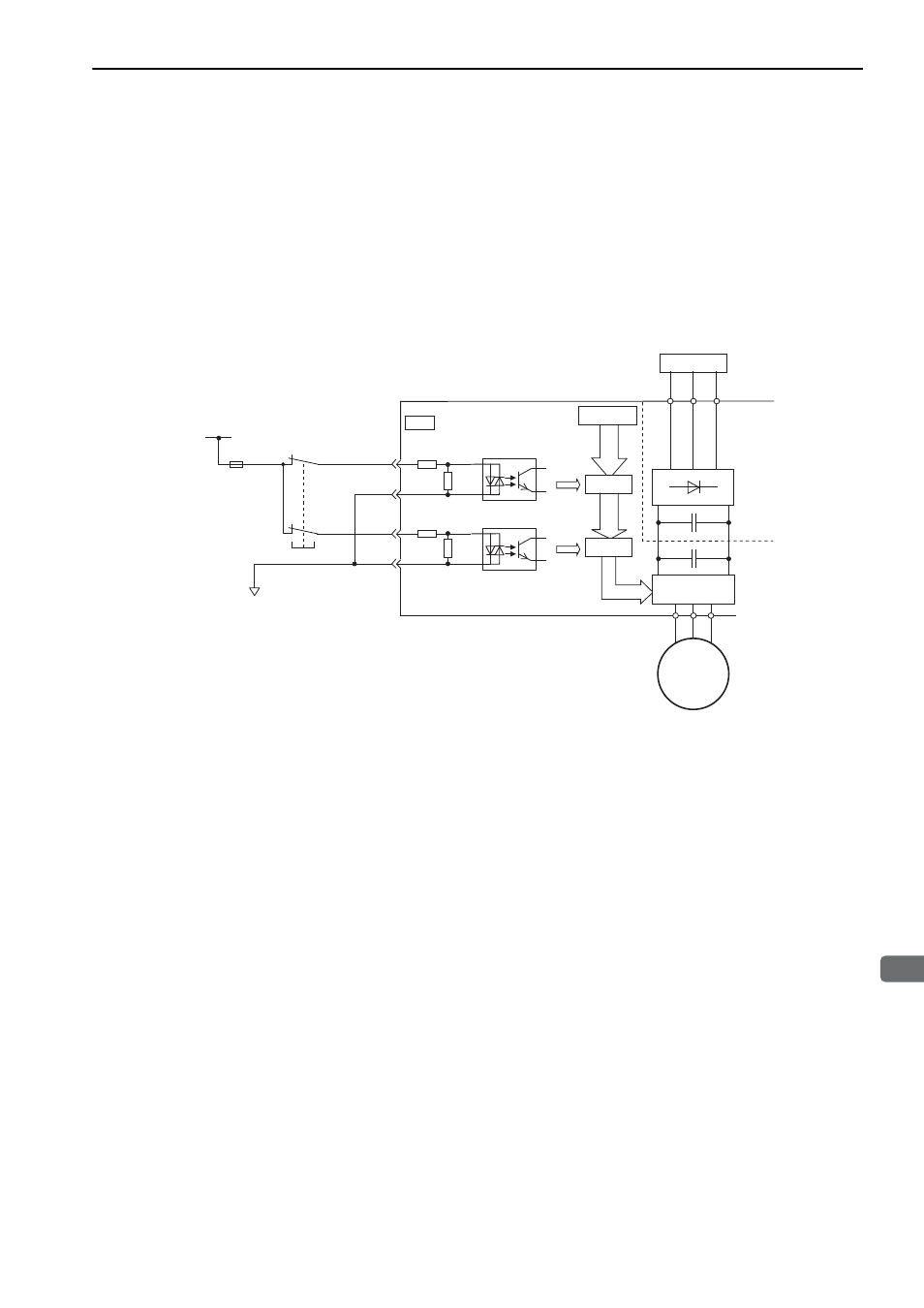
5.11 Safety Function
5-81
5
Ope
rat
ion
5.11 Safety Function
The safety function is incorporated in the SERVOPACK to reduce the risk associated with the machine by pro-
tecting workers from injury and by securing safe machine operation. Especially when working in hazardous
areas inside the safeguard, as for machine maintenance, it can be used to avoid adverse machine movement.
5.11.1 Hard Wire Base Block (HWBB) Function
The Hard Wire Base Block function (hereinafter referred to as HWBB function) is a safety function designed
to baseblock the servomotor (shut off the motor current) by using the hardwired circuits. Each circuit for two
channel input signals blocks the run signal to turn off the power module that controls the motor current, and
the motor current is shut off. (Refer to the diagram below.)
Note: For safety function signal connections, the input signal is the 0 V common and the output signal is the source output.
This is the opposite of other signals described in this manual. To avoid confusion, the ON and OFF status of signals
for safety functions are defined as follows:
ON: The state in which the relay contacts are closed or the transistor is ON and current flows into the signal line.
OFF: The state in which the relay contacts are open or the transistor is OFF and no current flows into the signal line.
(1) Risk Assessment
When using the HWBB function, be sure to perform a risk assessment of the servo system in advance. Make
sure that the safety level of the standards is met. For details about the standards, refer to Harmonized Stan-
dards at the front of this manual.
Note 1. Applications for certification are pending to show that SERVOPACKs comply with rules and regulations for
North American and other safety standards, including those for safe performance.
2. To meet the performance level d (PLd) in EN ISO 13849-1, the EDM signal must be monitored by a host control-
ler. If the EDM signal is not monitored by a host controller, the system only qualifies for the performance level c
(PLc).
The following risks can be estimated even if the HWBB function is used. These risks must be included in the
risk assessment.
• The servomotor will move in an application where external force is applied to the servomotor (for example,
gravity on the vertical axis). Take measures to secure the servomotor, such as installing a mechanical brake.
• The servomotor may move within the electric angle of 180 degrees in case of the power module failure, etc.
Make sure that safety is ensured even in that situation.
The maximum motor rotation angle is 1/6 of a rotation (This is the converted rotation angle for the motor
shaft).
• The HWBB function does not shut off the power to the SERVOPACK and converter or electrically isolate
them. Take measures to shut off the power to the SERVOPACK and converter before performing mainte-
nance on them.
CN8
/HWBB1+ 4
3
6
5
/HWBB1-
/HWBB2+
/HWBB2-
0 V
SERVOPACK
Switch
Block
Block
Power module
Power supply
Converter
24-V power supply
Fuse
Motor
Control circuit
Run
signal