Torque constant, Induced countervoltage, Step angle – BECKHOFF EL7037 User Manual
Page 21: Winding resistance, winding inductance, Specifying the stepper motor
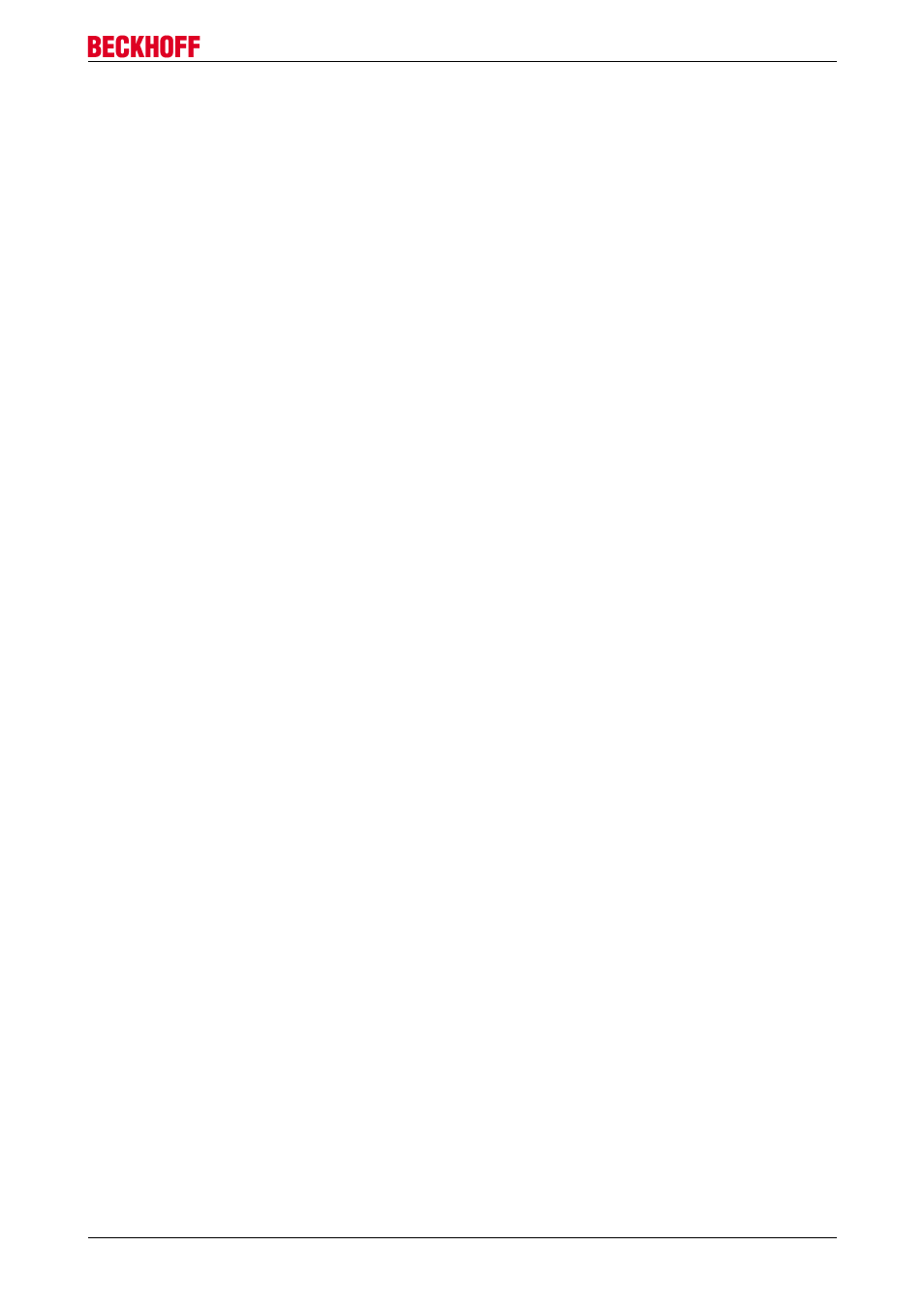
Product overview
•Torque constant
In the Extended Operation Modes the torque constant k
T
is used as an additional parameter for the
mechanical controlled system. It indicates the ratio between the torque-forming motor current and the active
torque at the shaft. However, since the field-oriented operating mode is not common for stepper motors, the
torque constant is usually not listed in the motor data sheet.
Electrical system
• Nominal voltage, supply voltage and winding resistance
Under steady-state conditions, the rated current at the rated voltage depends on the winding resistance. This
voltage should not be confused with the supply voltage of the power output stage in the EtherCAT Terminal.
The EL70x7 applies a controlled current to the motor winding. If the supply voltage falls below the nominal
voltage, the power output stage can no longer apply the full current, resulting in a loss of torque. It is
desirable to aim for systems with small winding resistance and high supply voltage in order to limit warming
and achieve high torque at high speeds.
• Induced countervoltage
Like servomotors, hybrid stepper motors induce a voltage u
i
[Vs/rad] in the stator winding of the motor, which
is proportional to the speed. It is also referred to as Back Electromotive Force (BEMF). In conjunction with
the DC link voltage (motor voltage), the induced countervoltage determines the physically achievable
maximum speed of the motor.
The ratio of the magnitude of the induced countervoltage and the motor speed varies depending on the
design and is described via the voltage constant k
e
.
u
i
= k
e
·ω
m
The motor parameter k
e
[mV/(rad/s)] is required for step loss recognition without encoder and for sensorless
control.
For stepper motors where the voltage constant is not specified in the data sheet, it can be relatively easily
determined using a digital multimeter. To this end the motor to be measured must be operated (within the
rated speed range) by an auxiliary motor via a coupling with constant speed. The motor phases of the motor
to be measured must be open (not connected to the terminal or shorted). The multimeter can then be used
to determine the RMS value of the induced countervoltage, and therefore the voltage constant, at one of the
two open motor phases (A or B).
• Step angle
The step angle indicates the angle travelled during each step. Typical values are 3.6°, 1.8° and 0.9°. This
corresponds to 100, 200 and 400 steps per motor revolution. Together with the downstream transmission
ratio, this value is a measure for the positioning accuracy. For technical reasons, the step angle cannot be
reduced below a certain value. Positioning accuracy can only be improved further by mechanical means
(transmission). An elegant solution for increasing the positioning accuracy is the microstepping function
offered by the EL70x7. It enables up to 64 intermediate steps. The smaller "artificial" step angle has a further
positive effect: The drive can be operated at higher speed, yet with the same precision. The maximum speed
is unchanged, despite the fact that the drive operates at the limit of mechanical resolution.
• Winding resistance, winding inductance
The winding inductance and winding resistance of the stepper motor stator determine the electrical motor
time constant T
e
= L / R, which is a key parameter for current controller configuration.
Specifying the stepper motor
1. Determine the required positioning accuracy and hence the step resolution. The first task is to
determine the maximum resolution that can be achieved. The resolution can be increased via
mechanical gear reduction devices such as spindles, gearing or toothed racks. The 64-fold
microstepping of the stepper motor terminals also has to be taken into account.
EL70x7
21
Version 1.0