Parameters a - 21, Ref detection, Fault restart – Yaskawa P7B Drive Bypass User Manual
Page 239: Torque detection, Table 1
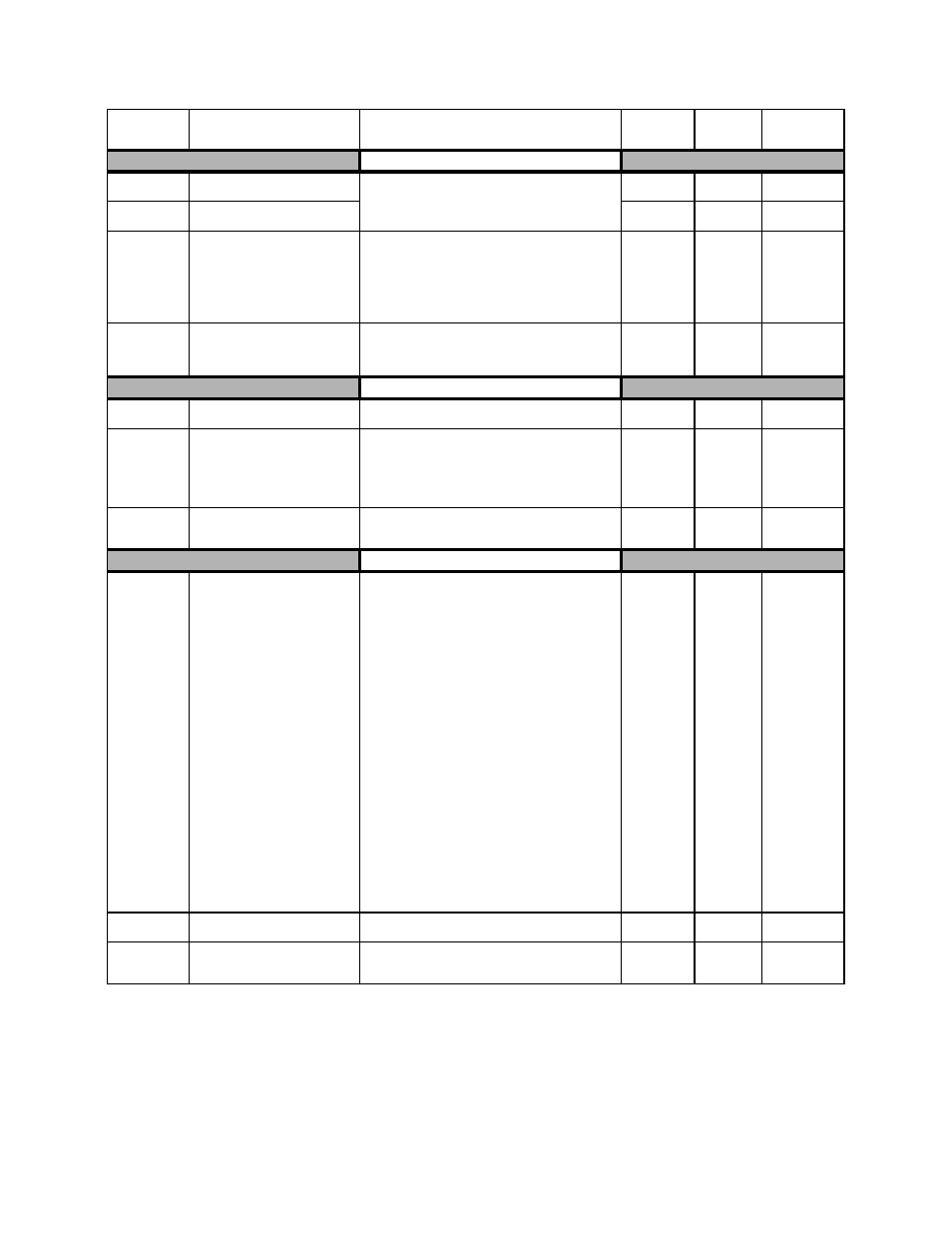
Parameters A - 21
Ref Detection
L4-01
Speed Agreement Detection Level
Spd Agree Level
L4-01 and L4-02 are used in conjunction with the
multi-function outputs, (H2-01and H2-02) as a setpoint
and hysteresis for a contact closure.
0.0 to 200.0
0.0Hz
Programming
L4-02
Speed Agreement Detection Width
Spd Agree Width
0.0 to 20.0
2.0Hz
Programming
L4-05
Frequency Reference Loss
Detection Selection
Ref Loss Sel
Determines how the Drive will react when the fre-
quency reference is lost.
0: Disabled - Drive will not run at the frequency
reference
1: Enabled @ % of PrevRef - Drive will run at a
percentage (L4-06) of the frequency reference level at
the time frequency reference was lost.
0 or 1
1
Quick Setting
L4-06
Frequency Reference Level at
Loss Frequency
Fref at Floss
If Frequency Reference loss function is enabled
(L4-05=1) and Frequency Reference is lost, then the
Drive will run at reduced frequency reference deter-
mined by L4-06. New Fref=Fref at time of loss L4-06.
0 to 100.0%
80.0%
Quick Setting
Fault Restart
L5-01
Number of Auto Restart Attempts
Num of Restarts
Determines the number of times the Drive will perform
an automatic restart.
0 to 10
0
Quick Setting
L5-02
Auto Restart Operation Selection
Restart Sel
Determines if the fault contact activates during an
automatic restart attempt.
0: No Flt Relay - fault contact will not activate during
an automatic restart.
1: Flt Relay Active - fault contact will activate during
an automatic restart.
0 or 1
0
Programming
L5-03
Maximum Restart Time After
Fault
Max Restart Time
If the restart fails (or is not attempted due to a
continuing fault condition, e.g. an OV fault) the Drive
waits L5-03 seconds before attempting another restart.
0.5 to 600.0
180.0sec
Quick Setting
Torque Detection
L6-01
Torque Detection Selection 1
Torq Det 1 Sel
Determines the Drive's response to an overtorque /
undertorque condition. Overtorque and Undertorque
are determined by the settings in parameters L6-02 and
L6-03.
0: Disabled
1: OL@SpdAgree - Alm (Overtorque Detection only
active during Speed Agree and Operation continues
after detection)
2: OL At RUN - Alm (Overtorque Detection is always
active and operation continues after detection)
3: OL@SpdAgree - Flt (Overtorque Detection only
active during Speed Agree and Drive output will shut
down on an OL3 fault.)
4: OL At RUN - Flt (Overtorque Detection is always
active and Drive output will shut down on an OL3
fault.)
5: UL@SpdAgree - Alm (Undertorque Detection is
only active during Speed Agree and operation
continues after detection.)
6: UL at RUN - Alm (Undertorque Detection is always
active and operation continues after detection.)
7: UL @ SpdAgree - Flt (Undertorque Detection only
active during Speed Agree and Drive output will shut
down on an OL3 fault.)
8: UL At RUN - Flt (Undertorque Detection is always
active and Drive output will shut down on an OL3
fault.)
0 to 8
0
Quick Setting
L6-02
Torque Detection Level 1
Torq Det 1 Lvl
Sets the overtorque/undertorque detection level as a
percentage of Drive rated current.
0 to 300
15%
Quick Setting
L6-03
Torque Detection Time 1
Torq Det 1 Time
Sets the length of time an overtorque / undertorque
condition must exist before being recognized by the
Drive. OL3 is then displayed.
0.0 to 10.0
10.0sec
Quick Setting
Table 1:
Parameter List (Continued
)
Parameter
No.
Parameter Name
Digital Operator Display
Description
Setting
Range
Factory
Setting
Menu
Location