Yaskawa P7B Drive Bypass User Manual
Page 87
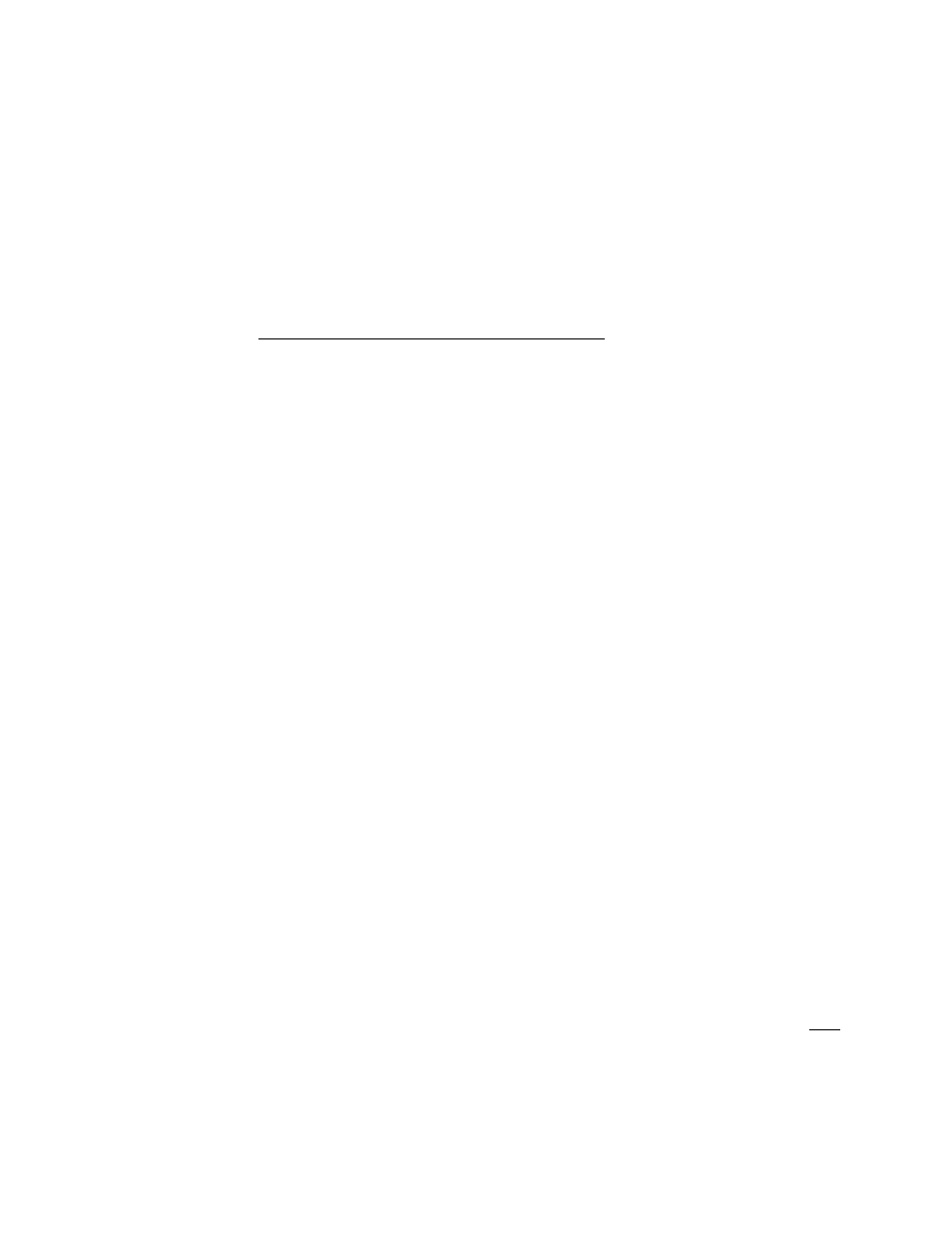
Start Up and Operation 4 - 5
! 3. Various menus are directly available by pressing the MENU key (see Chapter 3). When in the “-DRIVE-/Operation”
menu, the Drive can accept a run command from local (Hand mode) or remote (Auto mode) sources. Press the MENU
key until the “-ADV-/Programming” menu is displayed. From here, any of the parameters can be accessed and
changed using the
"
,
#
, and DATA/ENTER keys. See Appendix A for a list of programmable features. The
“-VERIFY-/Modified Consts” menu can be used to review or modify only those parameters that have been changed
from the Drive’s default values. Using the
"
,
#
, and DATA/ENTER keys as needed, verify that the parameters
are correct for the Drive and installation conditions. See the Factory Parameter Settings printed in Table 1 and Table 2
on page 2 of the Schematic Diagram that was shipped with the unit. Consider any additional parameter settings that
may be needed by this specific application.
The Factory Parameter Settings table documents Drive parameter settings, required to interface with the Bypass
logic circuit, that have been established at the factory and stored in a dedicated location in memory as “User
Initialization” values (think of it as a “back-up file”). If additional parameters are set to the specific needs of the
application project, and the system operation has been checked and verified, then the “User Initialization” values
should be stored in memory again by selecting and entering “1: Set Default” in parameter o2-03.
When there is a need for re-initialization of the “user” parameters (re-setting to the “User Initialization” values) of the
Bypass unit, then a “User Initialization” function should be carried out by selecting “1110: User Initialize” in
parameter A1-03. This will re-establish the drive set-up required for the Bypass application and any “user” parameter
values that have been stored.
The factory parameter settings required to interface with the bypass logic circuit have also been stored in the digital
keypad memory. If there is a need for re-initialization (re-setting to a known factory starting point for trouble-shooting
purposes) of the Bypass unit, then the “back-up file” in the digital keypad memory can be copied to the drive. In
parameter o3-01 select “2: OP->INV WRITE” to carry out the copy function.
Table 1 of the schematic is also used to document parameters that have been factory set to typical values for fan and
pump applications. These parameters may be changed to meet the needs of the specific application. In Table 5.1 of this
manual shading is used to distinguish between settings required by the Bypass logic and those that may be changed.
! 4. From the “-ADV-/Programming” menu, go to parameter E1-01 and select the nominal input voltage that the Drive will
receive in this specific application. The overall voltage classification of the Drive cannot be changed by this parameter.
However, the input voltage should be adjusted within the range available for the given voltage “class” of the Drive to
match the input voltage level normally found on the jobsite. For example, 480 VAC class Drives may be employed on
nominal three phase voltage distribution systems of: 380, 400, 415, 440, 460 or 480 VAC. The factory default values
may need to be changed to meet the needs of the application distribution voltage.
! 5. From the “-ADV-/Programming” menu, go to parameter E2-01 and enter the Motor rated current. Set this parameter to
the Full Load Amps (FLA) rating shown on the motor nameplate. This is essential for proper Drive operation and
motor overload protection.
! 6. If the unit being started has the Speed Potentiometer option, proceed directly to step 7. Otherwise, press the
MONITOR key to return to the “-DRIVE-/Operation” menu. The AUTO SEQ and REF LEDs and the STOP and
CONTROL POWER ON LEDs on the control panel should be ON at this time.
To start the motor in Drive mode, move the HAND/OFF/AUTO switch to HAND. The DRIVE RUN LED will turn
ON and the Drive will ramp up to “6 HZ”. Verify that motor rotation is correct. [Note: In Bypass packages, the Drive
is programmed at the factory for 5 seconds of DC injection braking at start (to stop a rotating motor when switching
from BYPASS to DRIVE), expect to see this delay each time the Drive is started.]
If the direction of motor rotation is wrong, turn the HAND/OFF/AUTO switch to OFF; and turn the Power OFF!
Wait for the Red CHARGE LED (near the Drive power terminals) to go out. When it does, swap the wires in the motor
junction box for T1 & T2 or on the output terminals of the motor OLR (S10). Tighten the terminal lugs, reapply the
power, turn to HAND and re-check the rotation direction.