Yaskawa P7B Drive Bypass User Manual
Page 88
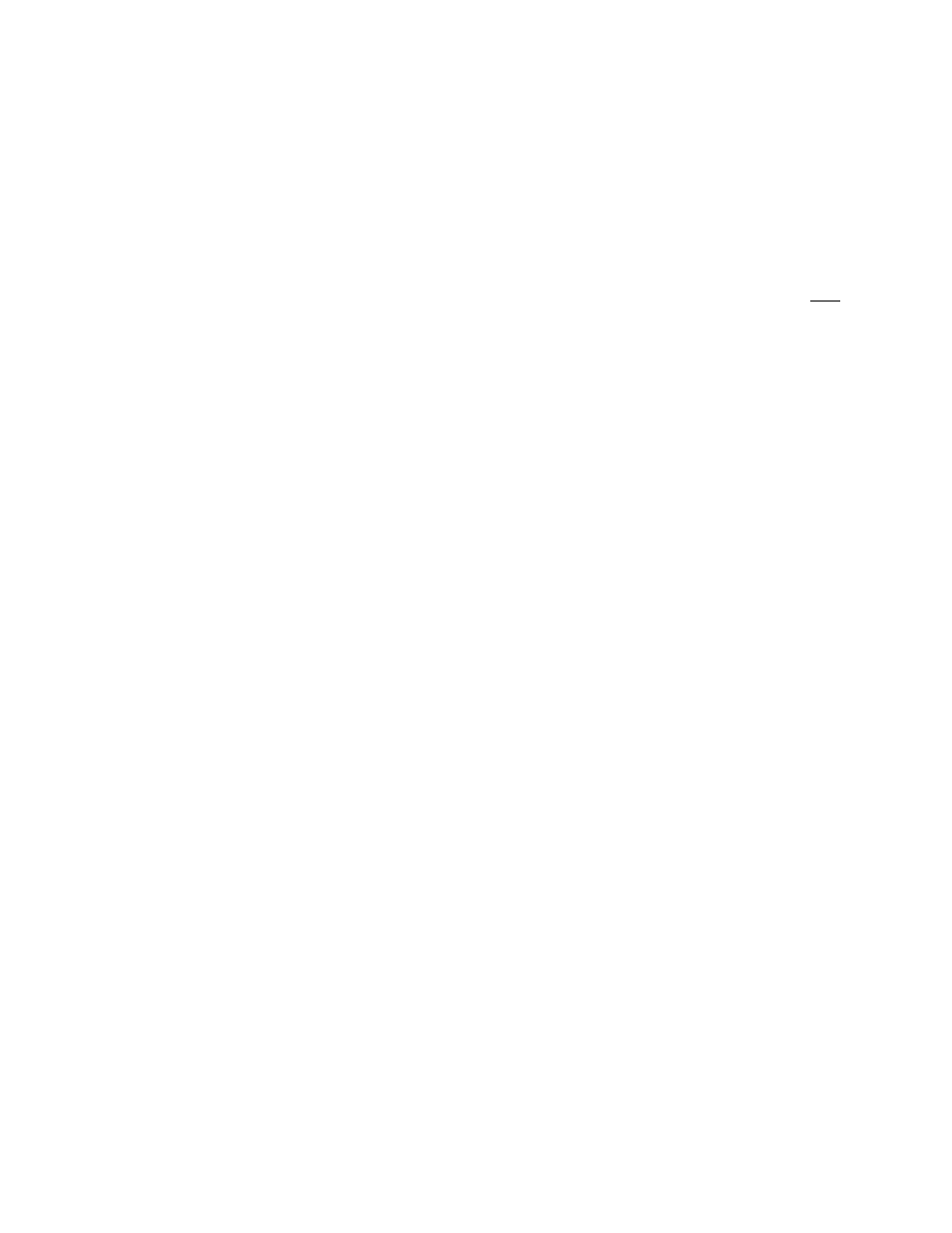
Start Up and Operation 4 - 6
! 7. If a Speed Potentiometer option is present, turn the Speed Potentiometer fully counterclockwise to ensure that the
local speed command is zero. If necessary, press the MONITOR key to return to the “-DRIVE-/Operation” menu. The
AUTO SEQ and REF LEDs and the STOP and CONTROL POWER ON LEDs on the control panel should be ON
at this time.
To start the motor in Drive mode, move the HAND/OFF/AUTO switch to HAND, then rotate the Speed Potentio-
meter clockwise to establish a speed command in the 6 to 10 Hz range. The DRIVE RUN LED will turn ON and the
Drive will ramp up to this setting. Verify that motor rotation is correct. [Note: In Bypass packages the Drive is
programmed at the factory for 5 seconds of DC injection braking at start (to stop a rotating motor when switching
from BYPASS to DRIVE), expect to see this delay each time the Drive is started.]
If the direction of motor rotation is wrong, turn the HAND/OFF/AUTO switch to OFF; and turn the Power OFF!
Wait for the Red CHARGE LED (near the Drive power terminals) to go out. When it does, swap the wires in the motor
junction box for T1 & T2 or on the output terminals of the motor OLR (S10). Tighten the terminal lugs, reapply the
power, turn to HAND; and re-check the rotation direction.
! 8. With correct motor rotation, press the MONITOR key, if necessary, to return to the “-DRIVE-/Operation” menu.
Using the
"
,
#
, and DATA/ENTER keys, manually run the Drive throughout its entire operating range, while
observing operation. If excessive vibration of the driven load is noted at specific input frequencies, the Jump
Frequency function may be used to eliminate this vibration, by programming d3-01 through d3-04.
! 9. Determine whether the remote speed command is a 0-10 VDC or a 4-20 mA signal. The positive side of the signal
should be connected to terminal A2 of the Drive terminal strip. The COMMON of the remote speed command
signal should be connected to terminal AC of the Drive. See the connection diagram on page 1 of the Bypass
schematic. [Note: The factory default is 4-20 mA, to change to 0 to 10 VDC adjust parameter H3-08 to “0: 0-10VDC”
and move Drive DIP switch S1-2, on the Drive terminal PCB to the OFF position.]
! 10. Observe if the remote speed command can achieve the minimum and maximum speeds desired. If not, perform the
following (see Chapter 5):
For 0-10 VDC input at Terminal A2
1. With no input, adjust the Bias (H3-11 setting) until an output of “0.0 Hz” is obtained.
2. With full scale input, adjust the Gain (H3-10 setting) until an output of “60.0 Hz” (or other desired maximum
frequency) is obtained.
For 4-20 mA input at Terminal A2
1. With 4 mA input, adjust Bias (H3-11 setting) until an output of “0.0 Hz” is obtained.
2. With 20 mA input, adjust Gain (H3-10 setting) until an output of “60.0 Hz” (or other desired maximum
frequency) is obtained.
! 11. Turn the HAND/OFF/AUTO switch to AUTO, then request a run command and speed reference signal from the
building automation system to confirm remote (auto) operation.
! 12. In preparation for testing the Bypass, observe the trip setting of the circuit breaker (CB1). The trip point is factory set
at the lowest possible setting and must be adjusted for each application. This breaker will trip due to inrush current and
load inertia unless it is reset!
•
For fan applications adjust the trip setting to ten times motor FLA.
•
For pump applications adjust the trip setting to six times motor FLA.
If circuit breaker tripping is experienced at these settings during motor starting on Bypass, increase the setting
gradually until the motor can be started without circuit breaker tripping.