Yaskawa iQpump Drive User Manual User Manual
Page 67
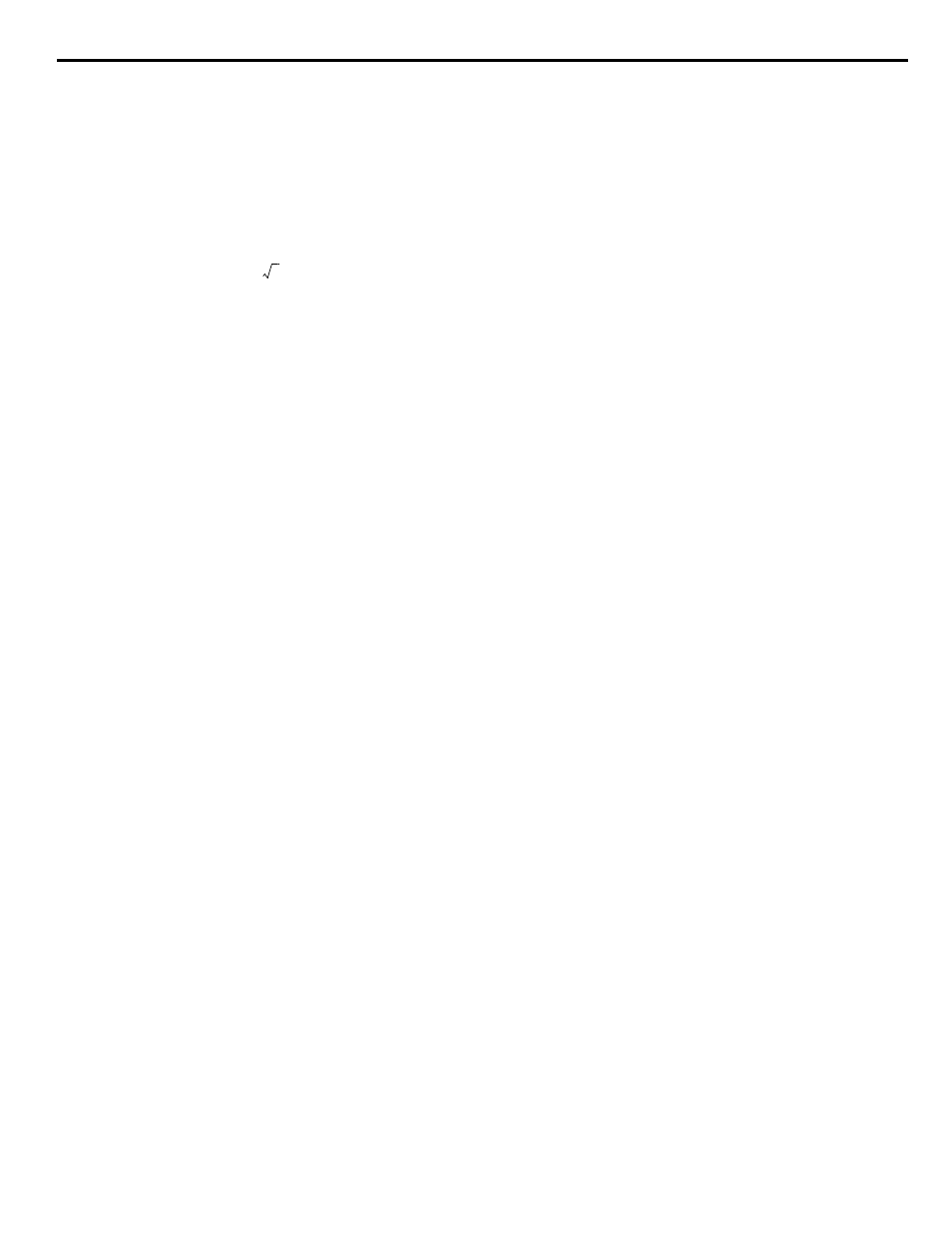
4.1 Start Up
YASKAWA TM.iQp.01 iQpump Drive User Manual
67
9. Never allow wire leads to touch metal surfaces. Short-circuit may result.
10. Never connect AC main power output terminals U/T1, U/T2 and W/T3.
11. Never connect power factor correction capacitors or noise filters to the iQpump drive output.
12. Use 600 Vac vinyl-sheathed wire or equivalent. Wire size should be determined considering voltage drop of leads.
Line voltage drop (V) =
x wire resistance (
Ω/km) x wire length (m) x current (A) x 10
-3
13. It is recommended that the motor lead length not exceed 164 feet (50 meters) and motor wiring be run in a separate conduit from
the power wiring. If lead length must exceed this distance, reduce the carrier frequency (see Figure 2.6) and consult Yaskawa
toll free at 1-800-YASKAWA (927-5292) for other motor protection measures.
14. Signal and control leads must be separated from main circuit leads (R/L1, S/L2, T/L3, U/T1, V/T2, W/T3).
15. Determine proper wire size for power and motor leads. Refer to Table 2.1 and Table 2.2 for details.
16. Review proper ground connections for the iQpump drive. Refer to Chapter 2 for details. The iQpump drive must be solidly
grounded using the main circuit ground terminal. Ground resistance should be less than 100
Ω for a 208-240 Vac iQpump drive.
Ground resistance should be less than 10
Ω for a 480 Vac iQpump drive. Select wire size suitable for the size of terminal screw.
Make the length as short as possible.
Never ground the iQpump drive in common with welding machines, motors or other large-current electrical equipment.
Where several iQpump drives are used, ground each iQpump drive directly or daisy-chain to the ground pole(s).
DO NOT FORM A LOOP WITH THE GROUND LEADS. See Table 2.4.
17. Review terminal functions of signal and control circuits. Refer to Table 2.8.
18. Verify if any customer safety devices are required (e.g. External Pump Fault).
19. Record the following motor nameplate information:
Voltage: _____________________Motor Rated Amps: ____________________
20. Verify that the commercial power supply is within the rated iQpump drive input voltage:
Power Supply: ____________________VAC Drive Input Voltage: ____________________VAC
21. Verify that the leads in the 3-Phase electric motor conduit box are configured for the proper voltage.
22. Ensure Motor Rated Current is less than or equal to iQpump drive Output Amps. If multiple motors are being used, make sure
that the Motor Rated Current sum is less than or equal to iQpump drive Output Amp rating. Please note that if multiple motors
are being operated from one iQpump drive, each motor must have its own overload and short circuit protection.
23. Wire all necessary power leads to the iQpump drive. DO NOT CONNECT MOTOR TO iQpump DRIVE YET.
24. Wire all necessary ground wires to the iQpump drive.
3