9 basic pump protection, Basic pump protection – Yaskawa iQpump Drive User Manual User Manual
Page 84
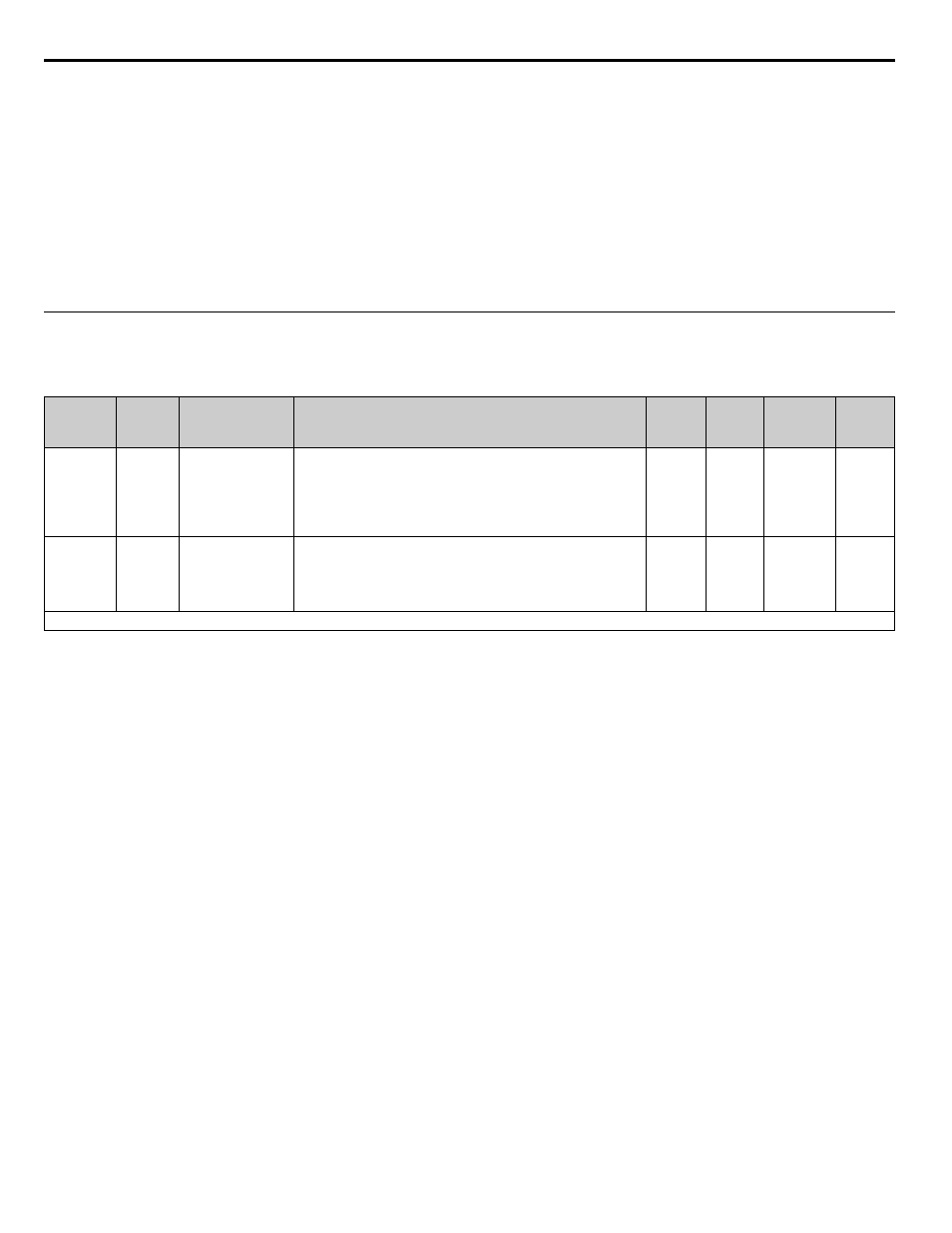
4.9 Basic Pump Protection
84
YASKAWA TM.iQp.01 iQpump Drive User Manual
4.9
Basic Pump Protection
The iQpump drive offers dedicated functions to protect the pump system from possible occurrences. The following section explains the
basic pump protection that the iQpump drive offers. One or more of the basic protection functions can protect from occurrences such as:
• Dry Well
• Air in System
• Blocked Impeller
• No Water
• Low Feedback (e.g. Low System Pressure Detection)
• High Feedback (e.g. High System Pressure Detection)
◆ Pump System Shutdown When System Setpoint Cannot Be Maintained
The iQpump drive continuously monitors pump system regulation and is able to shutdown the pump system after a programmable time in
case the system is not able to maintain the system setpoint. The Pump Protection function consists of 2 parameters:
Table 4.16
■
P1-11 Maximum Setpoint Difference: (Factory Default is 0.0 = Disabled)
The iQpump drive can be configured to display a Not Maintaining Setpoint (NMS) fault when the difference between the setpoint and the
feedback exceeds the Maximum Setpoint Difference (P1-11). When the Maximum Setpoint Difference has been exceeded, the drive will
trip on NMS fault and will coast to a stop when the fault occurs.
Setting P1-11 to a value of 0 will disable this function. This function is only active during operation in the Auto Mode.
The Maximum Setpoint Difference (P1-11) works in conjunction with the Not Maintaining Setpoint and Loss of Prime Time (P1-12).
The units for this parameter are determined by the System Units (P1-02)
■
P1-12 Not Maintaining Setpoint and Loss of Prime Time: (Factory Default is 60 sec.)
The iQpump drive can be configured to display a Maximum Setpoint Difference (P1-11) fault when the difference between the setpoint
and the feedback are exceeded for the time programmed in the Not Maintaining Setpoint and Loss of Prime Time (P1-12). The drive will
coast to a stop after the level has been exceed for the specified time programmed in P1-12.
This function is only active during operation in the Auto Mode.
The Not Maintaining Setpoint and Loss of Prime time (P1-12) is also used for the Prime Loss Level (P1-14) function. refer to Prime Loss
Level (P1-14) for further description.
The Not Maintaining Setpoint and Loss of Prime Time (P1-12) works in conjunction with Maximum Setpoint Difference (P1-11) and
Prime Loss Level (P1-14).
Note: The time value programmed into P1-12 is shared by Maximum Setpoint Difference (P1-11) and Prime Loss Level _(P1-14)
functions. However, independent times are maintained. If one function time, such as P1-11, has elapsed, the other functions time (P1-14)
is still maintained until this time has elapsed.
Parameter
No.
Modbus
Address
Parameter Name
Digital Operator
Display
Description
Setting
Range
Factory
Setting
Menu
Location
Page
No.
P1-11
<0032>
0106H
Maximum Setpoint
Difference
Max SetPoint Diff
When the Drive is running and the difference between the setpoint
and the feedback exceeds the level in P1-11 for the time specified in
P1-12, the Drive will trip on a “Not Maintaining Setpoint (NMS)”.
The Drive will coast to a stop when a fault occurs. A value of 0
disables this function. This function is only active during running
while operating in auto mode.
0.0 to
6000.0
(system
units
P1-02)
0.0
(system
units
P1-02)
Pump Quick
Setup
—
P1-12
<0032>
0107H
Not Maintaining
Setpoint and Loss of
Prime Time
Setpoint-LOP Tim
Delay time before a Not Maintaining SetPoint or Loss of Prime Time
fault occurs. Pump protection criteria specified in P1-11 or P1-14
must be met for the Drive to fault. The Drive will coast to a stop
when a fault occurs. A value of 0 disables both Loss of Prime and
Not Maintaining SetPoint faults.
0 to 3600
60 sec
Pump Quick
Setup
Denotes that parameter can be changed when the Drive is running.