3 derivative term ‘td, 4 relative cool gain ‘r2g, Derivative term ‘td – Super Systems 3 Series User Manual
Page 49: Relative cool gain ‘r2g
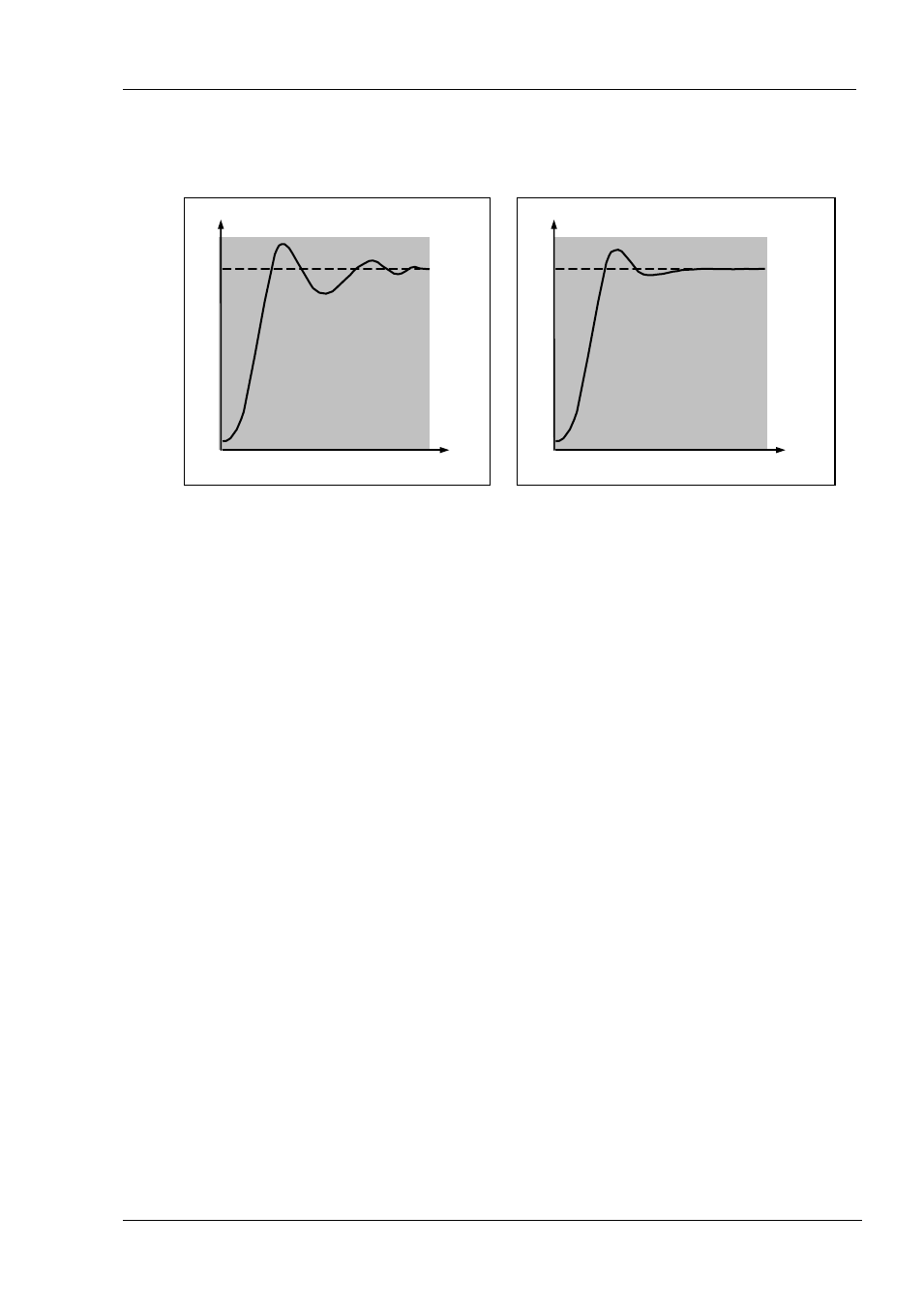
Series 3
Operations Manual
49
11.2.3
Derivative Term ‘TD’
Derivative action, or rate, provides a sudden shift in output as a result of a rapid change in error. If the measured value falls
quickly, derivative provides a large change in output in an attempt to correct the perturbation before it goes too far. It is most
beneficial in recovering from small perturbations.
The derivative modifies the output to reduce the rate of change of error. It reacts to changes in the PV by changing the output to
remove the transient. Increasing the derivative time will reduce the settling time of the loop after a transient change.
Derivative is often mistakenly associated with overshoot inhibition rather than transient response. In fact, derivative should not
be used to curb overshoot on start up since this will inevitably degrade the steady state performance of the system. Overshoot
inhibition is best left to the approach control parameters, High and Low Cutback.
Derivative is generally used to increase the stability of the loop, however, there are situations where derivative may be the cause
of instability. For example, if the PV is noisy, then derivative can amplify that noise and cause excessive output changes. In these
situations it is often better to disable the derivative and re-tune the loop.
If set to Off(0), no derivative action will be applied.
In Series 3 controllers, derivative is calculated on change of PV. For applications such as furnace temperature control, it is
common practice to use Derivative on PV to prevent thermal shock caused by a sudden change of output as a result of a change in
setpoint.
11.2.4
Relative Cool Gain ‘R2G’
The proportional band parameter ‘PB’ adjusts the proportional band for the heating output. Relative cool gain adjusts the cooling
proportional band relative to the heating proportional band. If the rate of heating and rate of cooling are widely different, it may
be necessary to manually adjust Relative Cool Gain to achieve the optimum settings for the cooling proportional band. A nominal
setting of around 4 is often used.
Note, this parameter is set automatically when Auto-tune is used unless the parameter ‘AT.R2G’ is set to ‘No’.
Temperature
Time
SP
Proportional + Integral response
Temperature
Time
SP
Response with derivative action
included