Super Systems 3 Series User Manual
Page 72
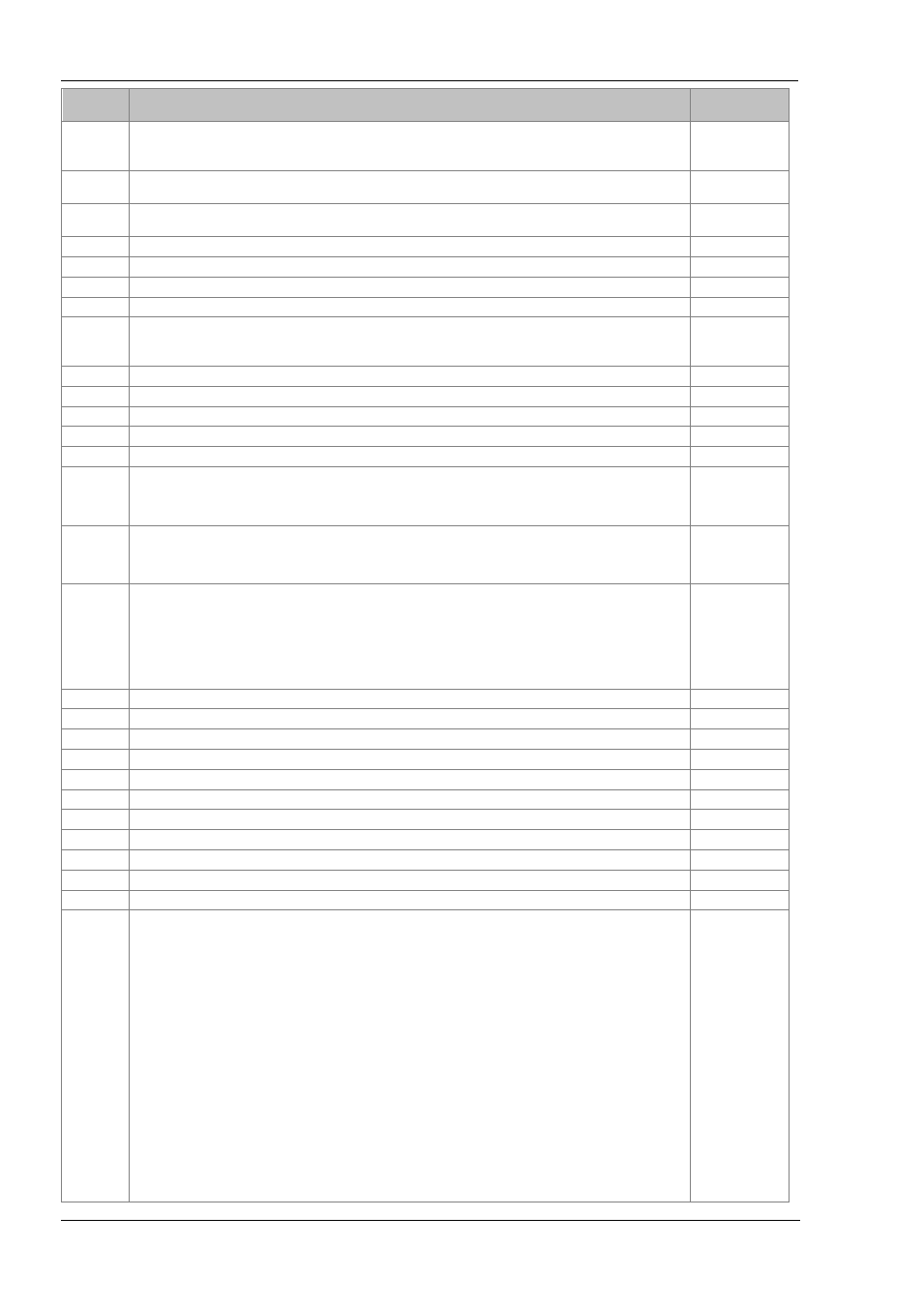
Operations Manual
Series 3
72
Parameter
Mnemonic
Parameter Name
Modbus Address
Decimal
CTRL.A
Control Action
0 = Reverse Acting
1 = Direct Acting
7
Ti
Integral Time
(0 = No Integral Action)
8
Td
Derivative Time
(0 = No Derivative Action)
9
RNG.LO
Input Range Low Limit
11
RNG.HI
Input Range High Limit
12
A1.---
Alarm 1 Threshold
13
A2.---
Alarm 2 Threshold
14
SP.SEL
Active Setpoint Select
0 = Setpoint 1
1 = Setpoint 2
15
D.BAND
Channel 2 Deadband
16
CB.Lo
Cutback Low
17
CB.HI
Cutback High
18
R2G
Relative Cool/Ch2 Gain
19
MTR.T
Motor Travel Time
21
SP1
Setpoint 1
NB – do not write continuously changing values to this variable. The memory technology used in this product has a limited
(100,000) number of write cycles. If ramped setpoints are required, consider using the internal ramp rate function or the
remote comms setpoint (Modbus address 26 )in preference.
24
SP2
Setpoint 2
NB – do not write continuously changing values to this variable. The memory technology used in this product has a limited
(100,000) number of write cycles. If ramped setpoints are required, consider using the internal ramp rate function or the
remote comms setpoint (Modbus address 26 )in preference.
25
Rm.SP
Remote (comms) setpoint. If selected using the remote setpoint selection (address 276 below, may also be controlled using
the instrument HMI or a digital input) then this is used as a setpoint providing a value has been received within a window of
about 5 seconds. If no value is received then the controller falls back to the currently selected setpoint (SP 1 or SP 2) with an
error indication. The Remote Setpoint may have a local trim (SP Trim, address 27) added to it to compensate for variations in
temperature in a particular zone.
This parameter is not saved when the instrument is switched off. It may be written to continuously over communications
without risk of damage to the instrument non-volatile memory.
26
LOC.t
Local Trim – added to the remote setpoint to compensate for local temperature variations in a control zone.
27
MR
Manual Reset
28
OP.HI
Output High Limit
30
OP.LO
Output Low Limit
31
SAFE
Safe Output Value for Sensor Break or other fault conditions.
34
SP.RAT
Setpoint Rate Limit Value (0 = no rate limit)
35
P.Err
Calculated Error (PV-SP)
39
A1.HYS
Alarm 1 Hysteresis
47
A2.HYS
Alarm 2 Hysteresis
68
A3.HYS
Alarm 3 Hysteresis
69
A4.HYS
Alarm 4 Hysteresis
71
StAt
Instrument Status. This is a bitmap:
B0 – Alarm 1 Status
B1 – Alarm 2 Status
B2 – Alarm 3 Status
B3 – Alarm 4 Status
B4 – Auto/Manual Status
B5 – Sensor Break Status
B6 – Loop Break Status
B7 – CT Low load current alarm status
B8 – CT High leakage current alarm status
B9 – FEATURE NOT AVAILABLE
B10 – PV Over-range (by > 5% of span)
B11 – CT Overcurrent alarm status
B12 – New Alarm Status
B13 – FEATURE NOT AVAILABLE
B14 – Remote (comms) SP Fail
B15 – Auto-tune Status
In each case, a setting of 1 signifies ‘Active’, 0 signifies ‘Inactive’.
75