Calibration, 1 to check input calibration, 1 precautions – Super Systems 3 Series User Manual
Page 81: 2 to check mv input calibration, 3 to check thermocouple input calibration, 4 to check rtd input calibration, To check input calibration, Precautions, To check mv input calibration, To check thermocouple input calibration
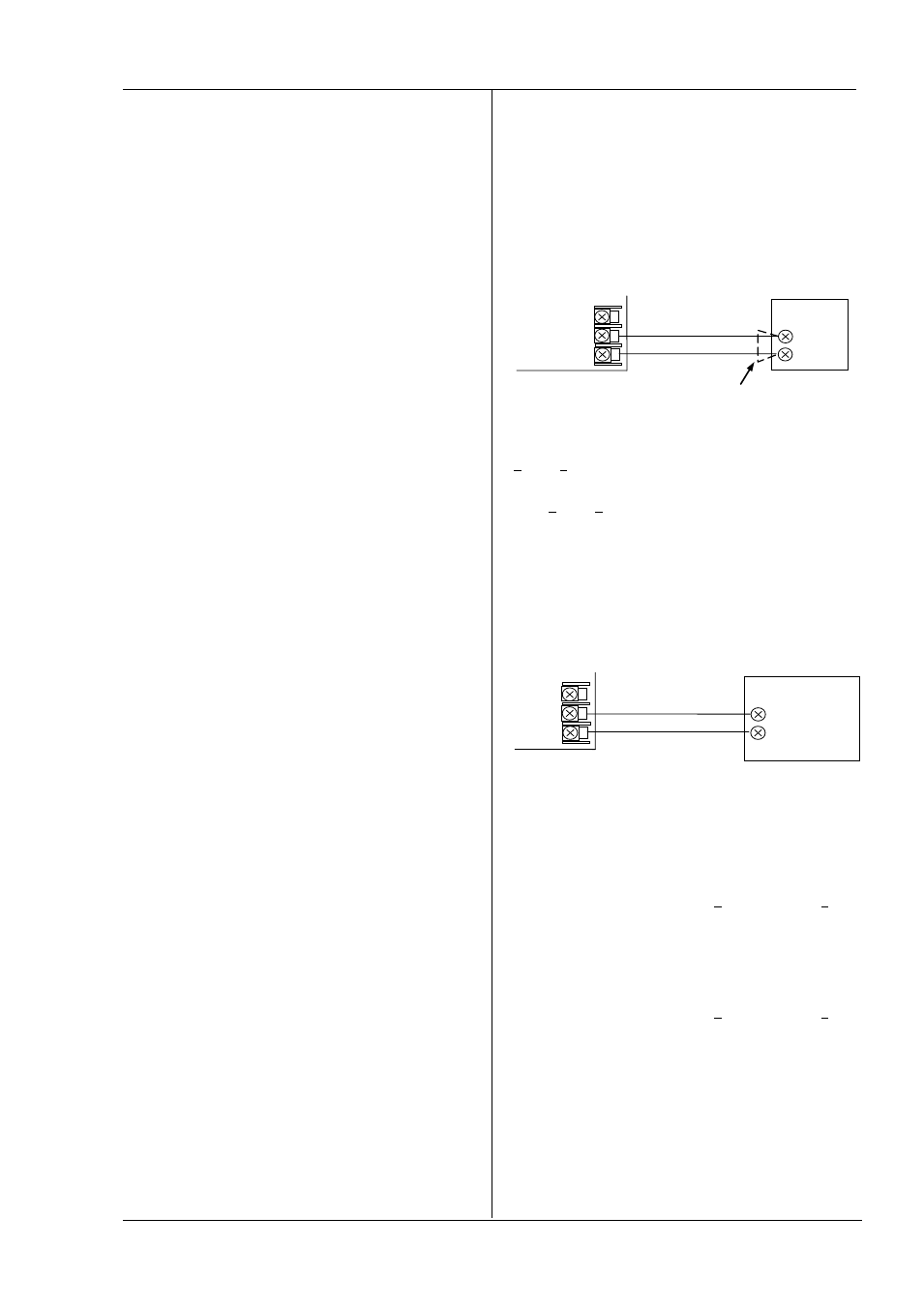
Series 3
Operations Manual
81
14. Calibration
The controller is calibrated during manufacture using
traceable standards for every input range. It is, therefore,
not necessary to calibrate the controller when changing
ranges. Furthermore, the use of a continuous automatic
zero correction of the input ensures that the calibration of
the instrument is optimised during normal operation.
To comply with statutory procedures such as the Heat
Treatment Specification AMS2750, the calibration of the
instrument can be verified and re-calibrated if considered
necessary in accordance with the instructions given in this
chapter.
For example AMS2750 states: "Instructions for calibration
and recalibration of "field test instrumentation" and "control
monitoring and recording instrumentation" as defined by the
NADCAP Aerospace Material Specification for pyrometry
AMS2750D clause 3.2.5 (3.2.5.3 and sub clauses), including
Instruction for the application and removal of offsets defined
in clause 3.2.4.”
14.1
To Check Input Calibration
The PV Input may be configured as mV, mA, thermocouple
or platinum resistance thermometer.
14.1.1
Precautions
Before checking or starting any calibration procedure the
following precautions should be taken:
1. When calibrating mV inputs make sure that the
calibrating source output is set to less than 250mV
before connecting it to the mV terminals. If
accidentally a large potential is applied (even for
less than 1 second), then at least one hour should
elapse before commencing the calibration.
2. RTD and CJC calibration must not be carried out
without prior mV calibration.
3. A pre-wired jig built using a spare instrument
sleeve may help to speed up the calibration
procedure especially if a number of instruments
are to be calibrated.
4. Power should be turned on only after the controller
has been inserted in the sleeve of the pre-wired
circuit. Power should also be turned off before
removing the controller from its sleeve.
5. Allow at least 10 minutes for the controller to
warm up after switch on.
14.1.2
To Check mV Input Calibration
The input may have been configured for a process input of
mV, Volts or mA and scaled in Level 3. The example
described in section 8.3.1 assumes that the display is set up
to read 2.0 for an input of 4.000mV and 500.0 for an input of
20.000mV.
To check this scaling, connect a milli-volt source, traceable
to national standards, to terminals V+ and V- using copper
cable as shown in the diagram below.
Figure 1: Connections for mV Input Calibration
☺
Ensure that no offsets have been set in the controller.
Set the mV source to 4.000mV. Check the display reads 2.0
+0.25% + 1LSD (least significant digit).
Set the mV source to 20.000mV. Check the display reads
500.0 +0.25% + 1LSD.
14.1.3
To Check Thermocouple Input Calibration
Connect a milli-volt source, traceable to national standards,
to terminals V+ and V- as shown in the diagram below.
The
mV source must be capable of simulating the thermocouple
cold junction temperature. It must be connected to the
instrument using the correct type of thermocouple
compensating cable for the thermocouple in use.
Figure -2: Connections for Thermocouple Calibration
Set the mV source to the same thermocouple type as that
configured in the controller.
Adjust the mV source for to the minimum range. For a type
J thermocouple, for example, the minimum range is -210
O
Adjust the mV source for to the maximum range. For a type
J thermocouple, for example, the minimum range is 1200
C.
However, if it has been restricted using the Range Low
parameter then set the mV source to this limit. Check that
the reading on the display is within +0.25% of reading +
1LSD.
O
Intermediate points may be similarly checked if required.
C.
However, if it has been restricted using the Range High
parameter then set the mV source to this limit. Check that
the reading on the display is within +0.25% of reading +
1LSD.
14.1.4
To Check RTD Input Calibration
Connect a decade box with total resistance lower than 1K
and resolution to two decimal places in place of the RTD as
indicated on the connection diagram below before the
instrument is powered up. If at any instant the instrument
was powered up without this connection then at least 10
minutes must elapse from the time of restoring this
connection before RTD calibration check can take place.
Thermocouple Compensating
cable
Thermocouple
simulator set to
T/C type
+
-
Controller
VI
V-
V+
Copper cable
mV Source
+
-
Controller VI
V-
V+