1 device configuration – Yaskawa Varispeed 626M5 User Manual
Page 136
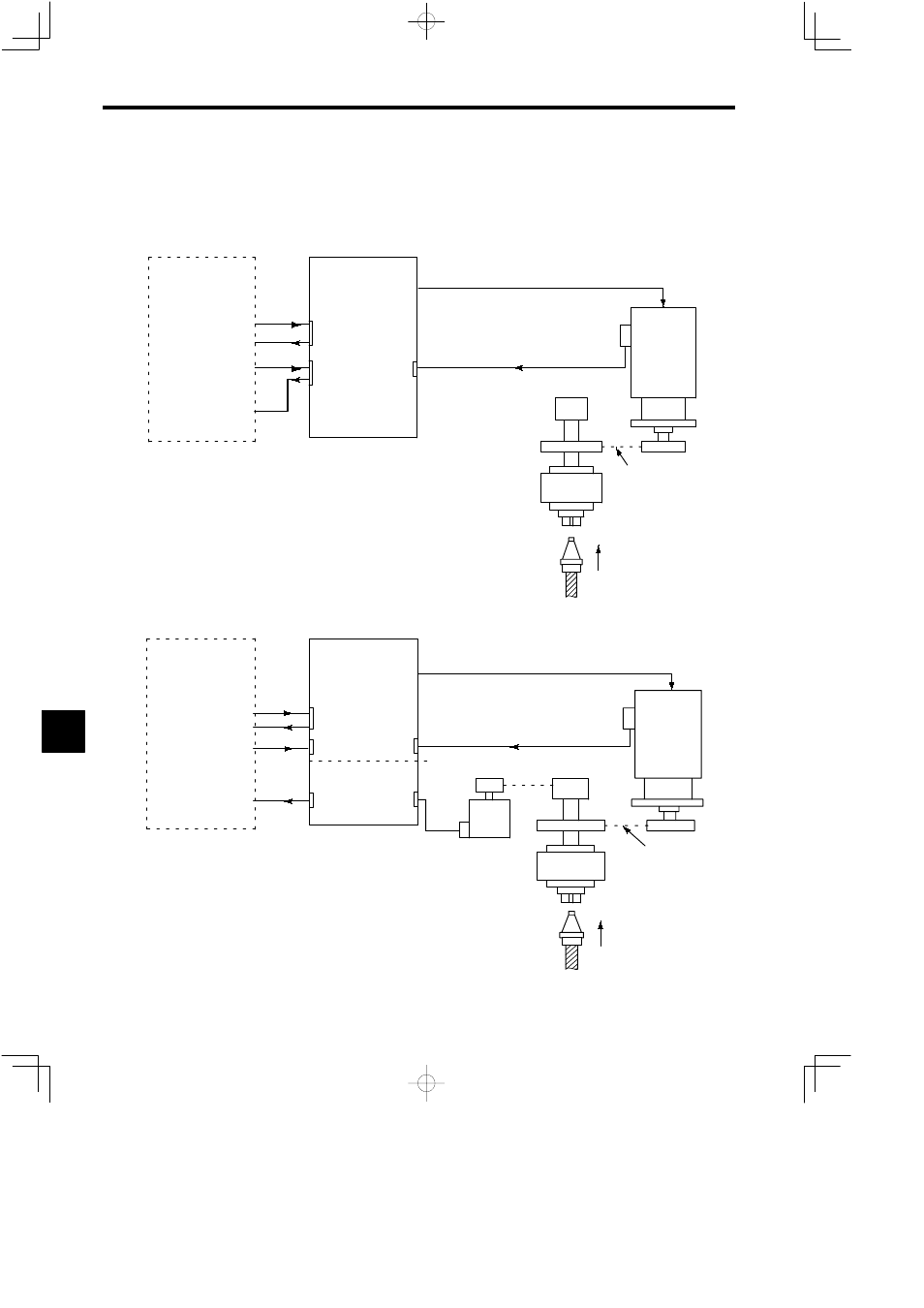
Orientation Control Using an Encoder
8 -2
8.1 Device Configuration
Orientation control with an Encoder is used for positioning based on dividing 1 rotation into 4,096 steps (i.e.,
a resolution of 0.088_), 12-bit binary, or 3-digit BCD stop angle references using the load shaft (machine-tool
main shaft, etc.) Encoder, and the Encoder Orientation Card. Positioning can be performed using the motor en-
coder signal if the load shaft and motor shaft are coupled 1:1 and there is no play.
NC panel
Motor encoder signal
Transmission
mechanism
(gear,belt,etc)
Tool
1 : 1
Main shaft
Stop position
reference
Orientation
Orientation signal
gear selection
VS−626M5
6CN
1CN
2CN
AC main
shaft motor
No Encoder
Orientation Card
required
Motor encoder signal
Fig 8.1
Main Shaft Orientation Device Configuration for Motor Encoder Method
NC panel
Orientation signal
gear selection
Orientation
Stop position
reference
Load shaft encoder
signal
Encoder Orientation
Card
Motor encoder signal
(Timing belt)
1:1
Load
shaft
encoder
Main shaft
Tool
AC main
shaft motor
Transmission
mechanism
(gears, belt, etc.)
VS−626M5
6CN
1CN
9CN
2CN
8CN
Fig 8.2
Main Shaft Orientation Device Configuration for Spindle Shaft Encoder Method
8