Cycle parameters – HEIDENHAIN iTNC 530 (340 49x-05) Cycle programming User Manual
Page 115
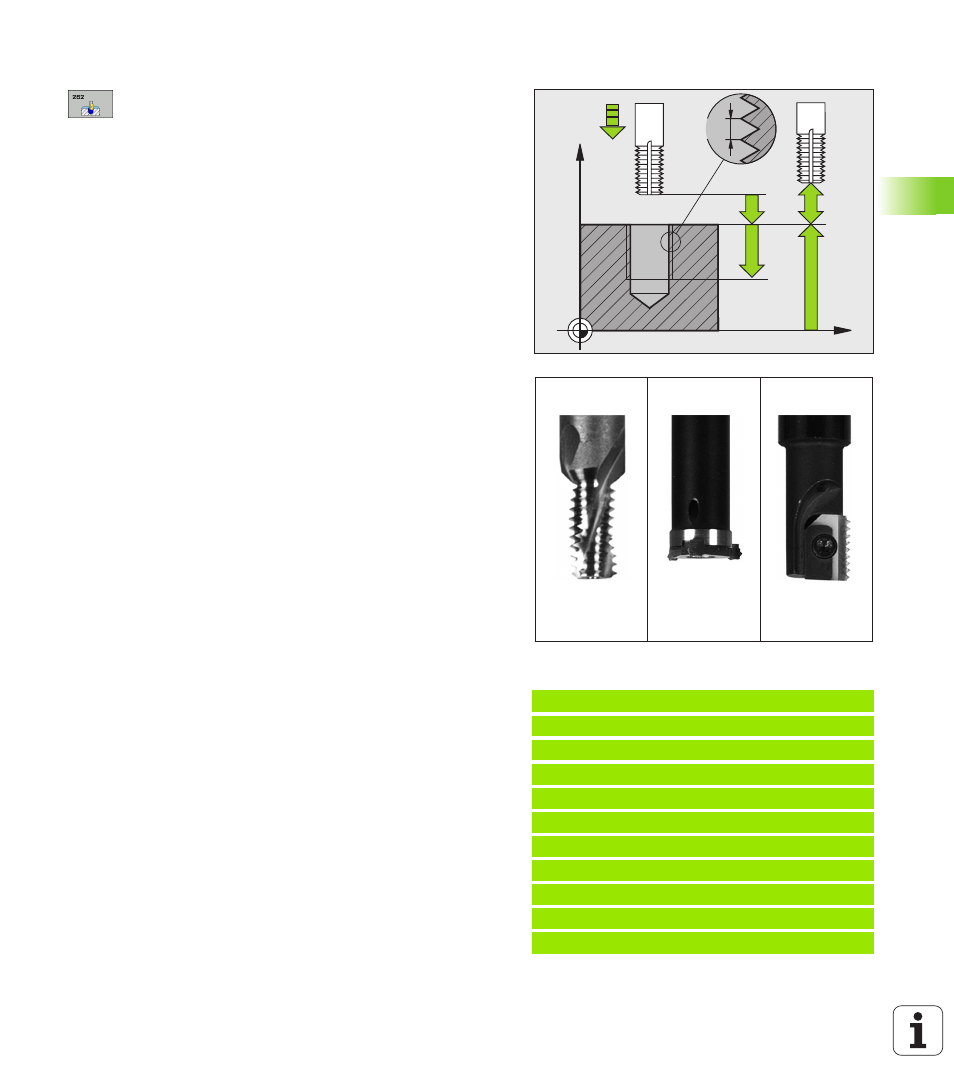
HEIDENHAIN iTNC 530
115
4.6 THREAD MILLING (Cy
c
le
262, DIN/ISO: G262)
Cycle parameters
U
Nominal diameter
Q335: Nominal thread diameter.
Input range: 0 to 99999.9999
U
Thread pitch
Q239: Pitch of the thread. The algebraic
sign differentiates between right-hand and left-hand
threads:
+ = right-hand thread
– = left-hand thread
Input range -99.9999 to 99.9999
U
Thread depth
Q201 (incremental): Distance between
workpiece surface and root of thread. Input range: -
99999.9999 to 99999.9999
U
Threads per step Q355:
Number of thread revolutions
by which the tool is moved:
0 = one 360° helical line to the thread depth
1 = continuous helical path over the entire length of
the thread
>1 = several helical paths with approach and
departure; between them, the TNC offsets the tool by
Q355, multiplied by the pitch. Input range: 0 to 99999
U
Feed rate for pre-positioning
Q253: Traversing
speed of the tool in mm/min when plunging into the
workpiece, or when retracting from the workpiece.
Input range 0 to 99999.999 alternatively FMAX, FAUTO,
PREDEF
.
U
Climb or up-cut
Q351: Type of milling operation with
M3
+1 = climb milling
–1 = up-cut milling
Alternatively PREDEF
U
Setup clearance
Q200 (incremental): Distance
between tool tip and workpiece surface. Input range
0 to 99999.9999, alternatively PREDEF
U
Workpiece surface coordinate
Q203 (absolute):
Coordinate of the workpiece surface. Input range:
-99999.9999 to 99999.9999
U
2nd setup clearance
Q204 (incremental): Coordinate
in the spindle axis at which no collision between tool
and workpiece (fixtures) can occur. Input range 0 to
99999.9999, alternatively PREDEF
U
Feed rate for milling
Q207: Traversing speed of the
tool during milling in mm/min. Input range: 0 to
99999.999; alternatively FAUTO.
Example: NC blocks
25 CYCL DEF 262 THREAD MILLING
Q335=10
;NOMINAL DIAMETER
Q239=+1.5 ;PITCH
Q201=-20
;DEPTH OF THREAD
Q355=0
;THREADS PER STEP
Q253=750
;F PRE-POSITIONING
Q351=+1
;CLIMB OR UP-CUT
Q200=2
;SETUP CLEARANCE
Q203=+30
;SURFACE COORDINATE
Q204=50
;2ND SETUP CLEARANCE
Q207=500
;FEED RATE FOR MILLING
X
Z
Q203
Q253
Q239
Q201
Q204
Q200
Q355 = 1
Q355 > 1
Q355 = 0