Choice of number of measuring points – HEIDENHAIN iTNC 530 (340 49x-05) Cycle programming User Manual
Page 456
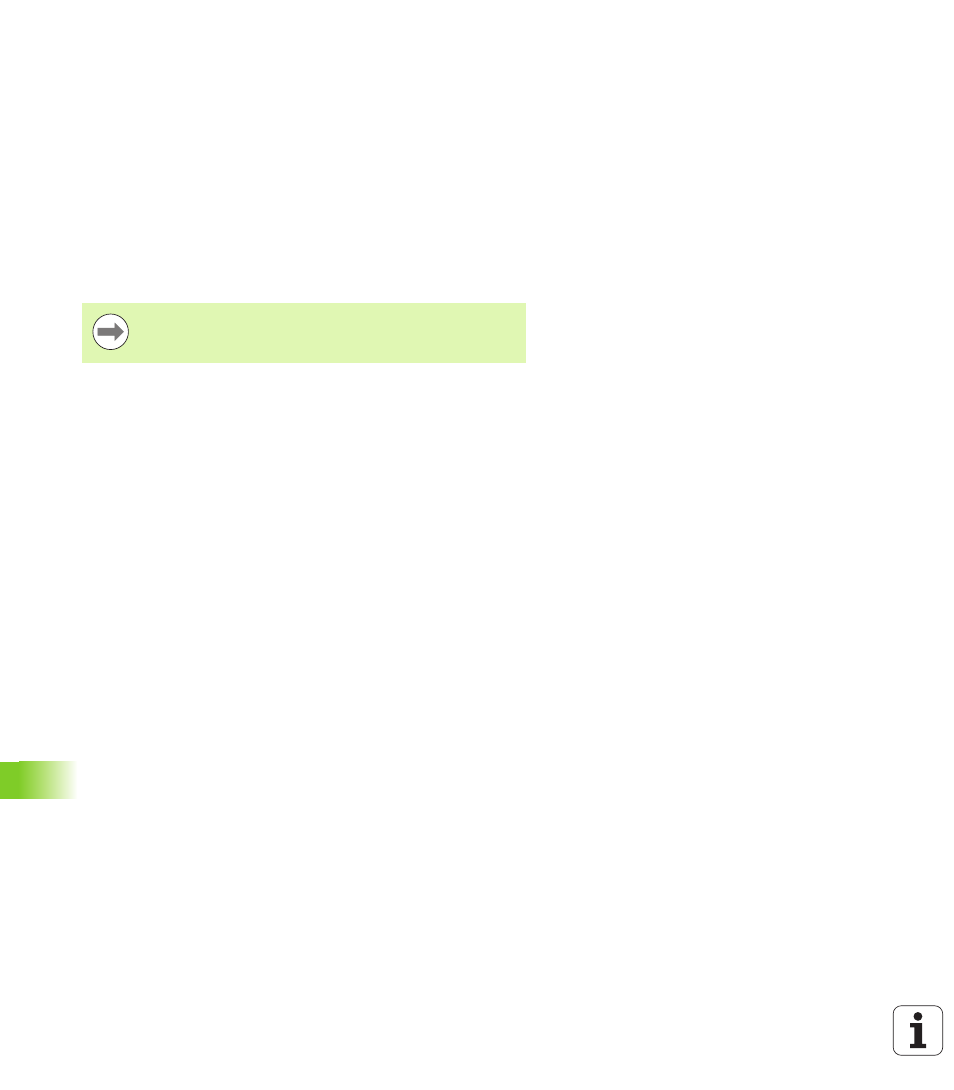
456
Touch Probe Cycles: Automatic Kinematics Measurement
1
8
.4 MEA
S
URE KINEMA
TICS (Cy
c
le
451, DIN/ISO: G451; option)
Choice of number of measuring points
To save time you can make a rough optimization with a small number
of measuring points (1-2).
You then make a fine optimization with a medium number of
measuring points (recommended value = 4). Higher numbers of
measuring points do not usually improve the results. Ideally, you
should distribute the measuring points evenly over the tilting range of
the axis.
This is why you should measure an axis with a tilting range of 0° – 360°
at 3 measuring points at 90°, 180° and 270°.
If you want to check the accuracy accordingly, you can enter a higher
number of measuring points in the Check mode.
Choice of the calibrating ball position on the
machine table
In principle, you can fix the calibrating ball to any position to the
machine table. If it is possible, you can also fasten the calibration ball
on fixtures or workpieces (e.g. using a magnetic clamp). The following
factors can influence the result of measurement:
On machines with rotary tables/tilting tables:
Clamp the calibrating ball as far as possible away from the center of
rotation.
Machines with very large traverse:
Clamp the calibration ball as closely as possible to the position
intended for subsequent machining.
You must not define a measuring point at 0° or 360°.
These positions do not provide any metrologically relevant
data.