Machines with hirth-coupled axes – HEIDENHAIN iTNC 530 (340 49x-05) Cycle programming User Manual
Page 455
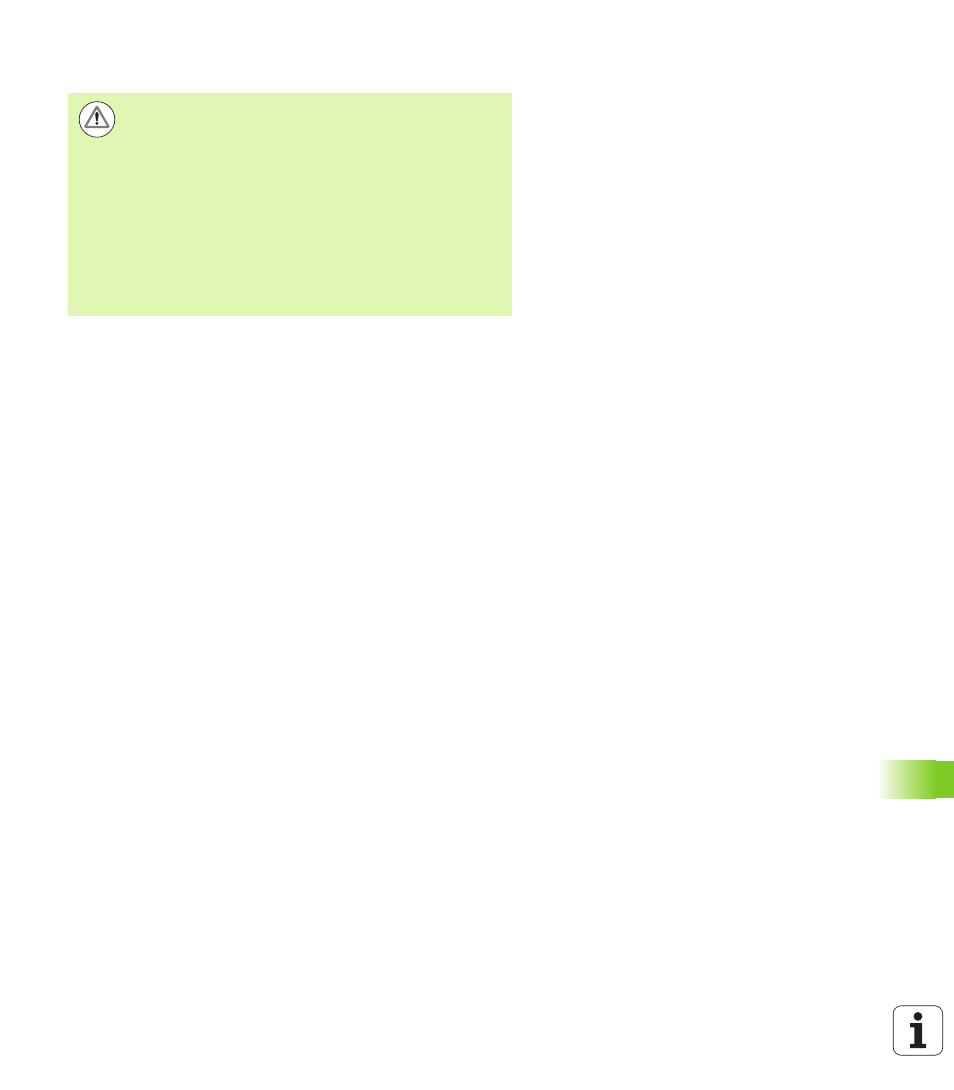
HEIDENHAIN iTNC 530
455
1
8
.4 MEA
S
URE KINEMA
TICS (Cy
c
le
451, DIN/ISO: G451; option)
Machines with Hirth-coupled axes
The measuring positions are calculated from the start angle, end angle
and number of measurements for the respective axis.
Example calculation of measuring positions for an A axis:
Start angle Q411 = -30
End angle Q412 = +90
Number of measuring points Q414 = 4
Calculated angular step = ( Q412 - Q411 ) / ( Q414 -1 )
Calculated angular step = = ( 90 - -30 ) / ( 4 - 1 ) = 120 / 3 = 40
Measuring position 1 = Q411 + 0 * angular step = -30°
Measuring position 2 = Q411 + 1 * angular step = +10°
Measuring position 3 = Q411 + 2 * angular step = +50°
Measuring position 4 = Q411 + 3 * angular step = +90°
In order to be positioned, the axis must move out of the
Hirth coupling. So remember to leave a large enough
safety clearance to prevent any risk of collision between
the touch probe and calibration ball. Also ensure that there
is enough space to reach the safety clearance (software
limit switch).
Define a retraction height Q408 greater than 0 if software
option 2 (M128, FUNCTION TCPM) is not available.
If necessary, the TNC rounds the calculated measuring
positions so that they fit into the Hirth grid (depending on
the start angle, end angle and number of measuring
points).