Procedure for working with cycle 19 working plane – HEIDENHAIN iTNC 530 (340 49x-05) Cycle programming User Manual
Page 284
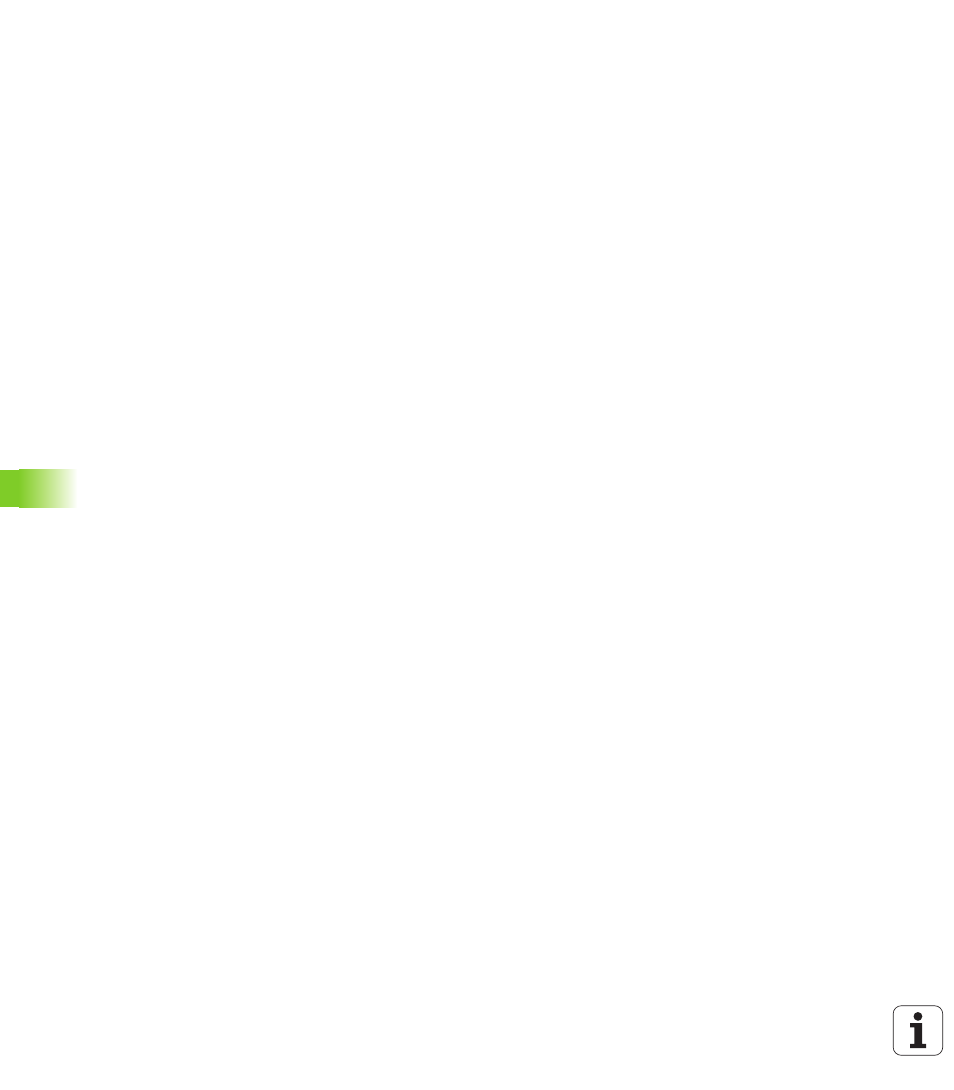
284
Cycles: Coordinate Transformations
1
1
.9 W
O
RKING PLANE (Cy
c
le 1
9
, DIN/ISO: G80, sof
tw
a
re
option 1)
Procedure for working with Cycle 19 WORKING
PLANE
1 Write the program
U
Define the tool (not required if TOOL.T is active), and enter the full
tool length.
U
Call the tool.
U
Retract the tool in the tool axis to a position where there is no
danger of collision with the workpiece (clamping devices) during
tilting.
U
If required, position the rotary axis or axes with an L block to the
appropriate angular value(s) (depending on a machine parameter).
U
Activate datum shift if required.
U
Define Cycle 19 WORKING PLANE; enter the angular values for the
rotary axes.
U
Traverse all principal axes (X, Y, Z) to activate compensation.
U
Write the program as if the machining process were to be executed
in a non-tilted plane.
U
If required, define Cycle 19 WORKING PLANE with other angular
values to execute machining in a different axis position. In this case,
it is not necessary to reset Cycle 19. You can define the new angular
values directly.
U
Reset Cycle 19 WORKING PLANE; program 0° for all rotary axes.
U
Disable the WORKING PLANE function; redefine Cycle 19 and
answer the dialog question with NO ENT.
U
Reset datum shift if required.
U
Position the rotary axes to the 0° position, if required.
2 Clamp the workpiece
3 Preparations in the operating mode
Positioning with Manual Data Input (MDI)
Pre-position the rotary axis/axes to the corresponding angular value(s)
for setting the datum. The angular value depends on the selected
reference plane on the workpiece.