Caution, Xi wiring – Yaskawa Sigma-5 Large Capacity Users Manual: Design and Maintenance-Rotary Motors-Mechatrolink-II Communication Reference User Manual
Page 11
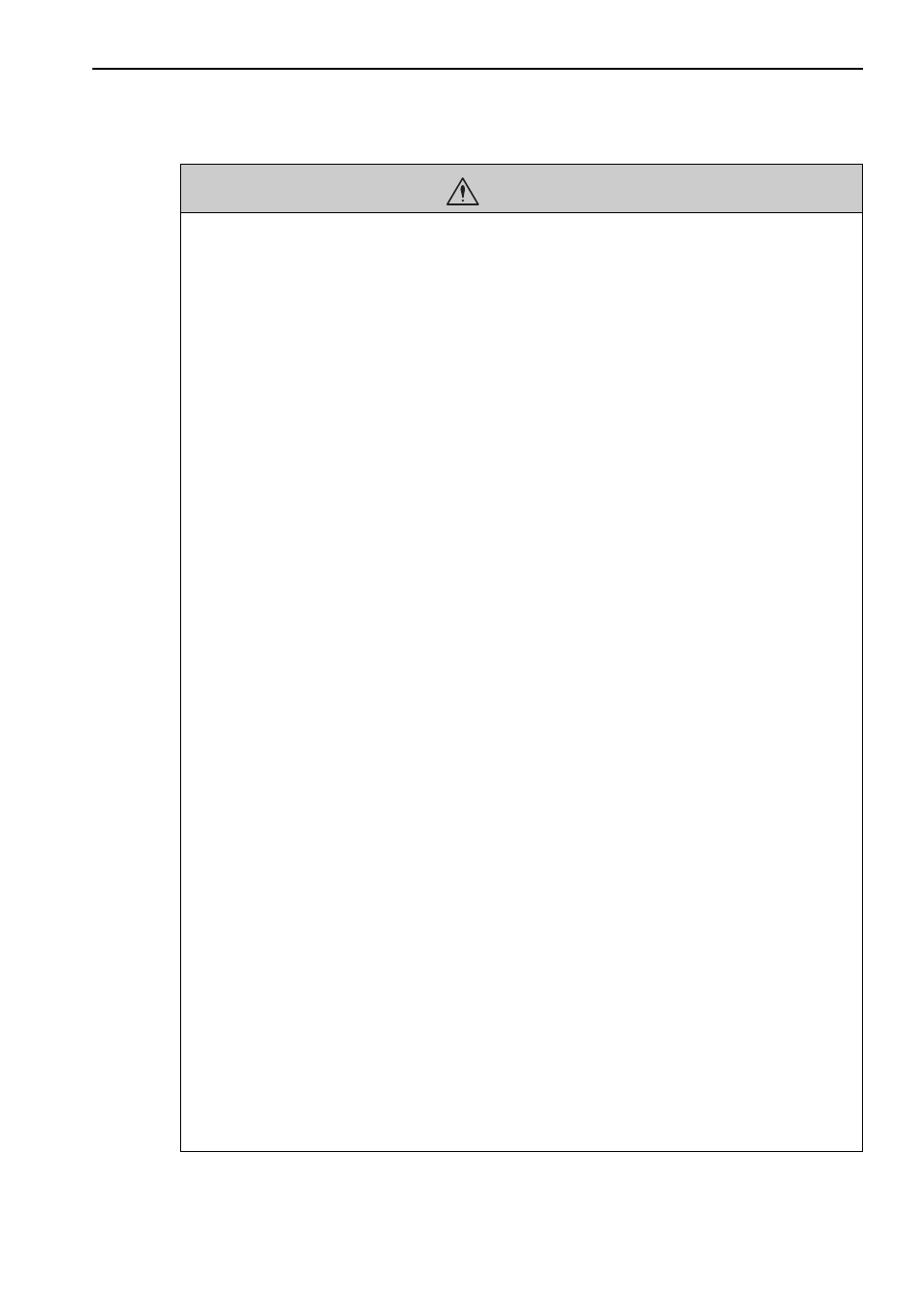
xi
Wiring
CAUTION
• Be sure to wire correctly and securely.
Failure to observe this caution may result in motor overrun, injury, or malfunction.
• Do not connect a commercial power supply to the U, V, or W terminals for the servomotor connec-
tion.
Failure to observe this caution may result in injury or fire.
• Securely connect the main circuit terminals.
Failure to observe this caution may result in fire.
• Do not bundle or run the main circuit cables together with the I/O signal cables or the encoder
cables in the same duct. Keep them separated by at least 30 cm.
Failure to do so may result in malfunction.
• Use shielded twisted-pair wires or multi-core shielded twisted-pair wires for I/O signal cables and
encoder cables.
• Use the bus bars that are included with the converter, and connect the P and N terminals on the
SERVOPACK and converter securely.
• The maximum cable length is 3 m for I/O signal cables, 50 m for connection cables for servomotor
main circuit or encoder cables, and 10 m for control power supply cables to 400-V converters (+24
V, 0 V).
• Do not touch the power terminals while discharging the main circuit’s capacitor, because high volt-
age may still remain in the SERVOPACK and the converter. For details on the charging time of the
main circuit’s capacitor, refer to 3.1.5 Discharging Time of the Main Circuit’s Capacitor.
Before starting to do wiring or inspections, confirm that the power has been completely discharged (charge
indicator: OFF) by using a tester to measure the voltage between the P and N terminals for DC power.
• Be sure to observe the following precautions when wiring the main circuit’s terminals and connec-
tors on a SERVOPACK or converter.
• Do not turn ON the power to a SERVOPACK or converter until all wiring, including the wiring to the
main circuit terminals, has been completed.
• Remove detachable main circuit terminals from the SERVOPACK and the converter prior to wiring.
• Insert only one power line per opening in the main circuit terminals.
• Make sure that no part of the core wire comes into contact with (i.e., short-circuits) adjacent wires.
• Install a battery at either the host controller or the battery unit of the encoder, but not both.
It is dangerous to install batteries at both ends simultaneously, because that sets up a loop circuit between the
batteries.
• Always use the specified power supply voltage.
An incorrect voltage may result in fire or malfunction.
• Make sure that the polarity is correct.
Incorrect polarity may cause ruptures or damage.
• Take appropriate measures to ensure that the input power supply is supplied within the specified
voltage fluctuation range. Be particularly careful in places where the power supply is unstable.
An incorrect power supply may result in damage to the product.
• Install external breakers or other safety devices against short-circuiting in external wiring.
Failure to observe this caution may result in fire.
• Take appropriate and sufficient countermeasures for each form of potential interference when
installing systems in the following locations.
• Locations subject to static electricity or other forms of noise
• Locations subject to strong electromagnetic fields and magnetic fields
• Locations subject to possible exposure to radioactivity
• Locations close to power supplies
Failure to observe this caution may result in damage to the product.
• Do not reverse the polarity of the battery when connecting it.
Failure to observe this caution may damage the battery, the SERVOPACK, or servomotor, or cause an explo-
sion.
• Wiring or inspection must be performed by a technical expert.
• Use a 24-VDC power supply for the control power of 400-V converter with double insulation or rein-
forced insulation.