Hypertherm HTA Rev 6.00 Install Guide User Manual
Page 116
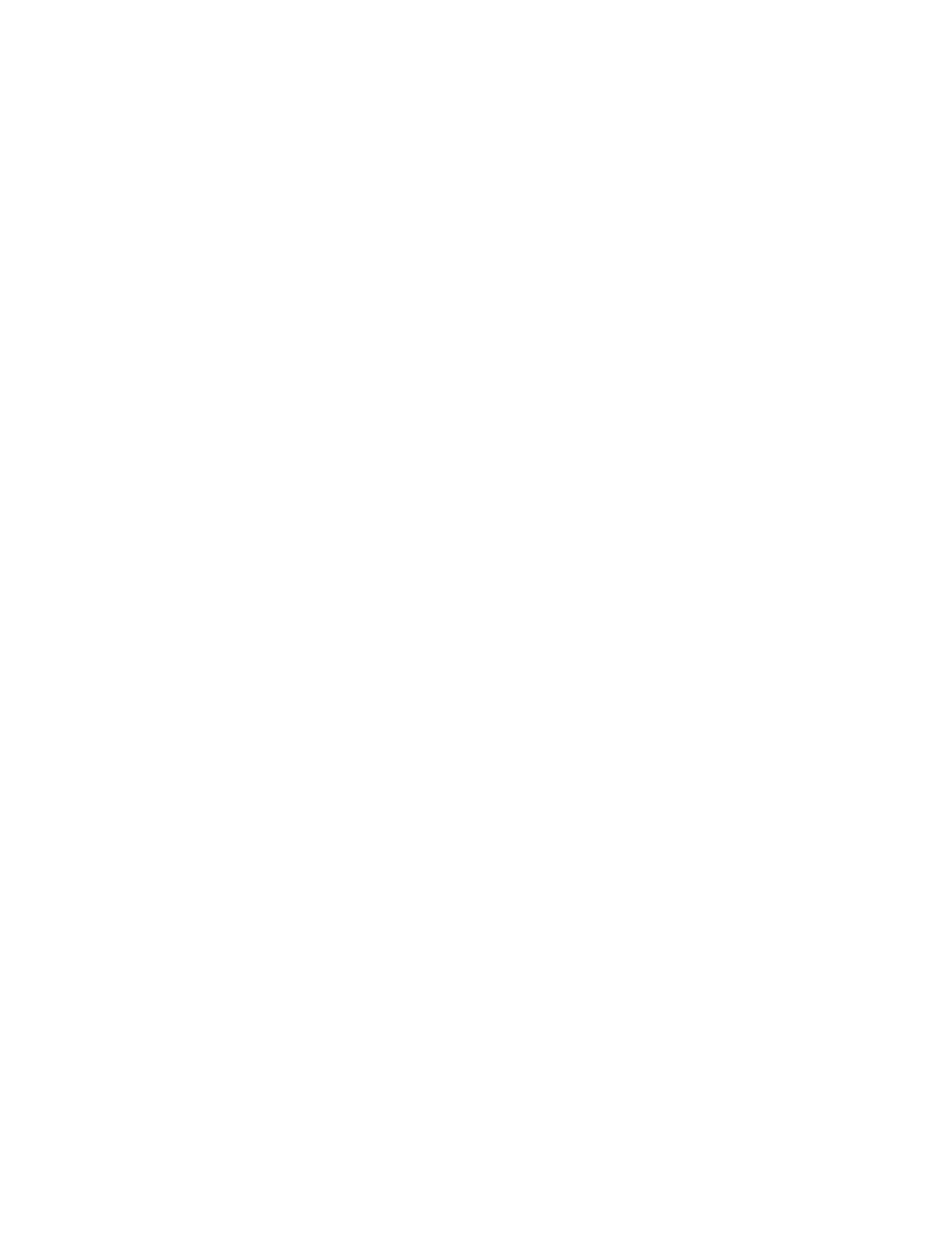
104
Installation & Setup Guide
1c) What is a Position / Servo Error?
A Position Error or Servo Error occurs when the distance between the ideal motion position and the
actual motion position exceeds a pre-defined Servo Error tolerance value. A Position Error indicates
that the response from the motion command was not executed, executed too slowly or executed
incorrectly. The Servo Error Tolerance is user definable value within the control and is usually set to
be a value twice the noted following error during normal operation. This allows the system to operate
without nuisance faults caused by temporary resistance to the motion, such as dirt on motion rails or
temporary tension from motor cabling, etc.
Note: It is important to remember that in the Closed Position Loop, the output command will adjust to
try and maintain the desired speed and positioning. As a result, a loss of Encoder Feedback would
result in the control sending out it’s maximum motion command to the motor causing it to “run away”
without control. Conversely, failure of the motor to turn while feedback is enabled, will result in a
position error and the command output will stop when the fault occurs.
2) Determining the Encoder Counts per Inch Parameter and Maximum Machine Speed
Remembering that the position loop uses the pulses/ counts from the encoder to calculate distance, it
is important to determine how many encoder pulses are equal to a specific distance of machine
motion. The control uses the Encoder Counts Per Inch/mm value as the constant to calculate
distance and speed.
The Encoder Counts per Inch/mm is a calculation based on the number of pulses generated by the
encoder for one revolution of the motor and how much distance is traveled from that motor motion
through the gearing being used.
So this relationship shown as a formula would be:
Counts / Line x
Counts / Rev x
1 Rev / Inch =
Encoder Counts/ Inch
encoder mode e.g 4x
Pulses per Rev
gear box ratio &
rack /pinion ratios
For example: The resolution of a 4X - 1000 line encoder counts both edges ( lines ) of channel A and
channel B to equal 4 counts per line multiplied by the 1000 lines per revolution equaling 4000 counts
per revolution. If the encoder revolutions per inch of travel are 1:1, we would have 4000 encoder
counts per inch of travel.
4 Counts/ Line x 1000 Lines/ Rev x 1 Rev/ Inch = 4000 Encoder Counts/ Inch
Determining Maximum Machine Speed
The following information is used to establish the proper value for determining max machine speed.
Multiply the max RPM of the motor by the number of inches of travel per revolution to get the resulting
Maximum Machine Speed in Inches per Minute.
For example*
4000 RPM Motors x .125 inches per rev = 500 inches per minute
*Note: Through test or calculation it is determined that the table moves 1/8 inches per revolution of
the encoder.
With the Maximum Speed, Encoder Counts per Inch, DAC and Encoder polarities determined and
entered into control setups, a simple test of machine motion can be made in the control Drive
Diagnostics screen. This test should be made with the motors disengaged for saftey. This is a basic