Hypertherm HTA Rev 6.00 Install Guide User Manual
Page 118
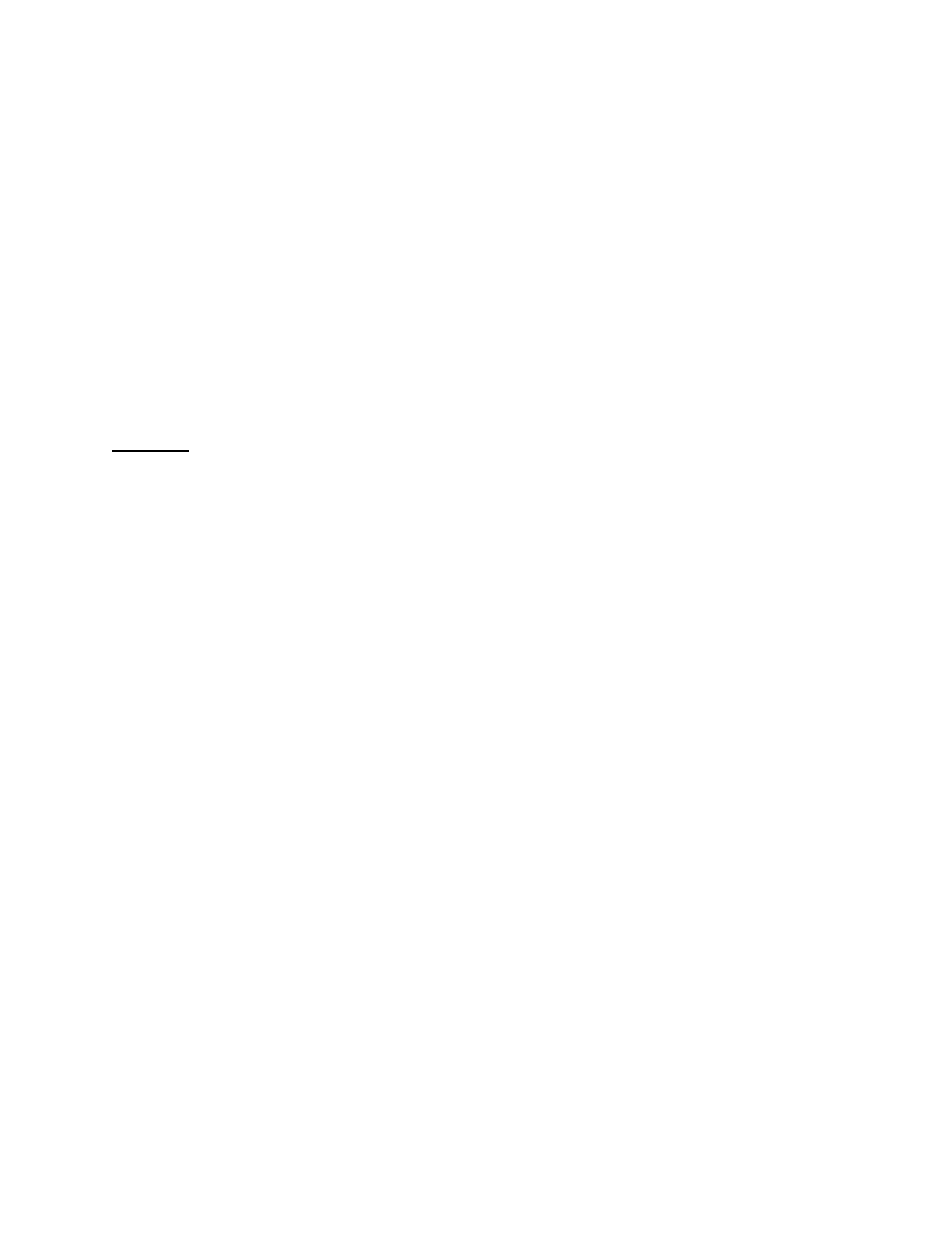
106
Installation & Setup Guide
4) Recommended Tuning Procedures for Hypertherm Automation Motion Controls
Using the information previously provided as a core understanding of the position loop process we
can now look at tuning motion for the desired motion performance. Due to potential safety hazards
and the potential possibility for machine damage from incorrect tuning it is recommended that this
operation be performed by trained and experienced personnel.
Prior to performing motion tuning, values for DAC Polarity, Encoder Polarity for each axis and
maximum machine speed should be calculated and entered into control setups. Servo Error
Tolerance for the axes should be set to maximum ( 5 inch max for X/Y motion ).
Initially, it is recommended that basic tuning start with the motors disengaged from the machine to
allow the user to confirm controlled motion and response of the motion axes. An initial Acceleration
Rate of 10 Mg’s can be used to begin the motion tuning. It is important to remember that after the
motors are engaged to the machine for motion, the load requirements for each axis will change
requiring additional tuning. Additionally if the acceleration rate in increased after the initial tuning,
additional adjustments to Gain tuning may be required for proper machine motion.
Procedure
We recommend tuning the system by performing manual moves at a slow speed with all gains set to
zero with the exception of Proportional Gain. Proportional Gain should start with a small value of 10.
Engage the motors to the machine frame and beginning raising the Proportional Gain to allow
movement. If the axes starts to vibrate or oscillate this indicate the selected gain value is too high
and should be lowered. It may also require de-tuning the response of the Drive amplifier.
Now that you have some basic control of the system set up the Watch Window to display Position
and Following Error for the selected Axes. Load and automatically “trial” the Test Pattern simple
shape from the shape library. You will be able to follow response of the system by watching the
performance of the Motor /Encoder feedback and its ability to maintain path on the control preview
screen.
Systematically increase Proportional gain until it has little or no effect on the following error or until
instability becomes noticeable. Then reduce proportional gain to eliminate instability. Adjust
Derivative gain to 10% of the proportional gain value. For a Velocity Loop Servo Drive, Integral gain
should be set to zero. After tuning for the best response, increase Feed Forward gain systematically
to further reduce following error if necessary. It is not required that you eliminate following error but it
is wise to ensure that Following Error for each axis is similar. Please Note: Feed Forward Gain will
reduce steady state following error, but may cause overshoot.
It is important to note that some following error is desirable, following error terms should be nearly the
same from one axis to another, and the polarity of the following error term must be the same as the
direction of travel.
Finally, check the system tuning by placing a pen on the system. “Draw” the test pattern provided in
the simple shape library and observe the cornering capability, arc/ circle contouring and the ability to
position at the center crossings. When troubleshooting tuning issues, varying the size and trial speed
can often provide valuable information through observations of the pen tracing.
After the system has been successfully tuned, adjust the Servo Error Tolerance to equal twice the
normal Following Error for the axes ( note: This is a common approach to setting the Servo Error
Tolerance but is up to the discretion of the service agent ) . This is allows the system to operate
without nuisance faults caused by temporary resistance to the motion, such as dirt on motion rails or
temporary tension from motor cabling, etc.