Hypertherm HPR260 Manual Gas Preventive Maintenance Program Rev.5 User Manual
Page 313
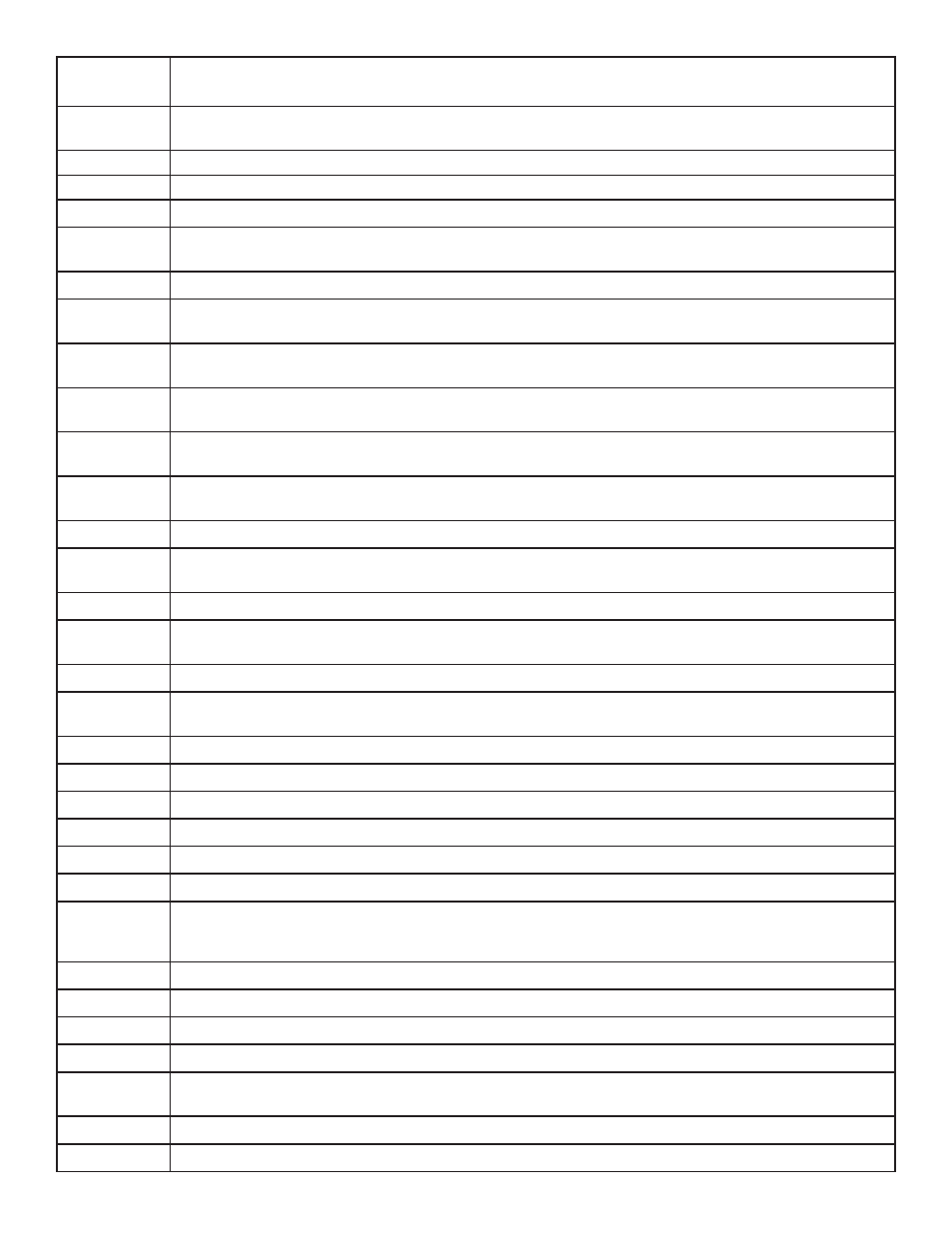
Changed
Page
Description of change for revision 5 (date of change - 4/2008)
i - x
Updated EMC and Warranty information to the latest version. Updated table of contents to reflect changes
for the new revision.
2.4
Added information to the gas quality and pressure requirements table. Added notes below the table.
2.5
Updated Amperage and Power information in the table.
2.9 and 3.15
Added a bullet point about keeping the vent hole clear.
2.10
Added a second bullet point with bend radius information. The maximum bend radius for the torch leads is
152.4 mm (6 in).
3.6 – 3.10
Added new recommended grounding and shielding practices information.
3.11
Added a line to the first bullet point " Allow 1 m (3 ft) of space on all sides of the power supply for ventilation
and service.
3.16
Changed negative lead part numbers for 60 m (200 ft) and 75 m (250 ft) from 123771 and 123772 to
123778 and 123779.
3.24
Corrected the part number for the 10 m (35 ft) CNC interface cable. It was 123314 and is was changed to
123214.
3.30
Changed the part numbers for the 60 m (200 ft) and 75 m (250 ft) work leads. They were 4/0 and are now
2/0 cables.
3.31 and 3.33
Removed reference to plastic insulator in step 4. It is no longer used. Replaced the term braiding with
braided sleeve (3.33).
3.32
Added new pilot arc connection instructions.
3.34
Removed the instruction to lubricate the threads on the quick-disconnect receptacle. They should not be lu-
bricated.
3.36
Updated values in the recommended slow-blow fuse size column.
3.38 – 3.40
Updated torch coolant requirements to include specific requirements for standard, cold and hot operating
conditions. Added more information under water purity requirements.
3.41
Changed the text in the caution box.
4.9, 4.13, 4.14,
and 4.16
Added 50 amp consumables (4-9), kerf width compensation for 50 amp cutting (4-13 and 4-14), and 50
amp cut chart (4-16).
4.12
Removed "consumable for bevel cutting" reference. "Bevel cutting" already references appendix C.
4.15
Corrected the flow rates.
4.29
Corrected the numbers for initial pierce height (mm) for 15 and 20 mm material thicknesses.
4.33
Corrected cutting speeds in the Metric cut chart.
5.5 – 5.7
Added "Gas system purge cycle" and "Gas system valve usage" information.
5.9
Added text saying that the screens used will vary depending on the CNC that is being used.
5.10 – 5.19
Added 1 page to the error code troubleshooting and revised error codes as necessary. All HPR error codes
are listed in all HPR manuals, including the auto gas specific codes. Added new code numbers 066,
140 - 143, 180, and 181
5.21
Changed the name in the first column from “ID” to “State code”
5.28 – 5.34
Added new coolant flow troubleshooting information.
5.35 and 5.36 Updated gas leak test procedure.
5.37
Added caution about using revision "J" software
5.41
Added 50 amp information and updated information for other amperages in the pilot arc current table and
the transfer current table.
5.44
Added call-outs for pressure sensors (P1-P4) and for solenoid valves (SV1-SV14) in the selection console.
5.45
Added call-outs for pressure sensors (P5-P8) and for Berkert valves (B1-B4) in the metering console.