HEIDENHAIN TNC 335 Technical Manual User Manual
Page 17
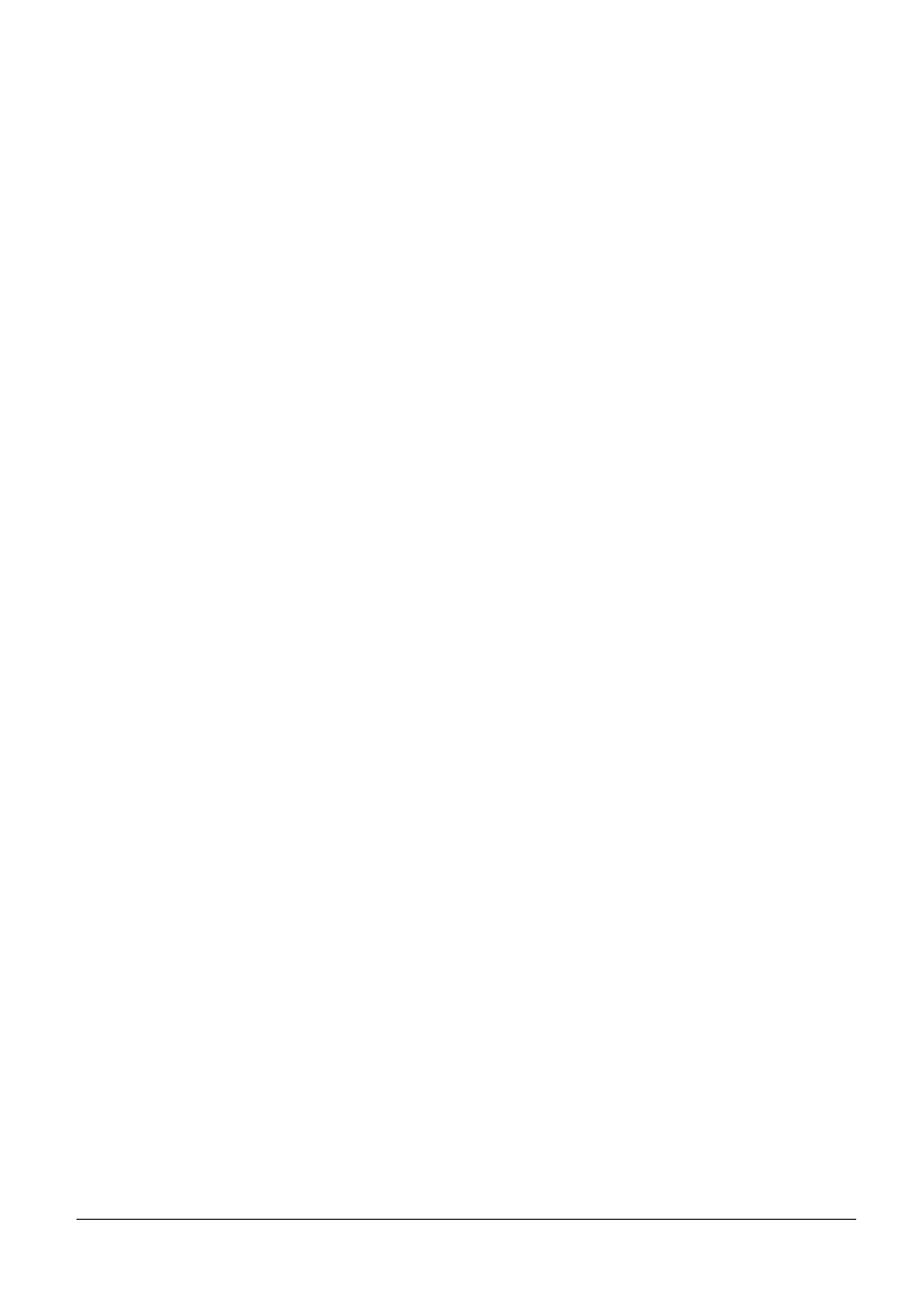
1-2
TNC 360/TNC 335
Update information No. 1
9/93
•
If bit 2 is set in machine parameter MP7300, the last inserted (programmed) tool is
automatically activated during switch-on.
•
By setting the static PLC marker M2612 the PLC can now prevent the exchange of pocket
numbers in the central tool memory during a P output.
•
Function FN19 was introduced, with which two numerical or Q parameter values with an
accuracy of 1/1000 (i.e., three places after the decimal point) are transferred into the PLC
doublewords D280 and D284. A value of 2.5, for example, is filed in the doublewords as 2500.
The unit of measure of the calling NC program is set in marker M2150 (millimeter=0/inch=1).
During transfer the NC sets the strobe marker M2149. The transfer must be acknowledged by
the PLC with the marker M2611.
•
The number of PLC labels was increased to 1024.
•
Marker M2614 was introduced. Setting this marker blocks the output of PLC functions
(M/S/T/Q output) by the NC. The marker is set and reset by the PLC; it is read by the NC.
•
Marker M2827 was introduced. It is set by the PLC and causes the following behavior in case
of an external EMERGENCY STOP and erasable positioning error:
Machining is not aborted ("control in operation" symbol off, strobe signal reset). Instead,
machining is merely interrupted as in an NC STOP (control-in-operation symbol blinks). This
permits machining to be resumed with NC START after the error has been corrected. This
marker functions only for the output of M/S/T/Q strobes.
•
Now a maximum of 32 Q parameters can be transferred for user cycles. To do this, the 'DLG-
DEF' or 'DLG-CALL' blocks must be programmed several times in the user cycle, whereby in
the third DLG block only the first five entries can be evaluated.
•
The following Q parameters were introduced:
Q114
current tool length
Q115 to Q118 measured values of the 4th axis after a programmed probing cycle
•
The type of tool compensation (R0/RR/RL/R+/R-) is stored in Q parameter Q123:
Q123 = 0 means R0
= 1 means RR
= 2 means RL
= 3 means R+
= 4 means R-
•
Application as positioning module:
If machine parameter MP 4010 = 1 is programmed (PLC program from RAM), no machine
parameters will be taken from the PLC EPROM when the positioning module is switched on. If
the CRC sum of the machine parameters is incorrect they will be taken from the PLC EPROM.