11 module 9125: run an nc block – HEIDENHAIN TNC 335 Technical Manual User Manual
Page 497
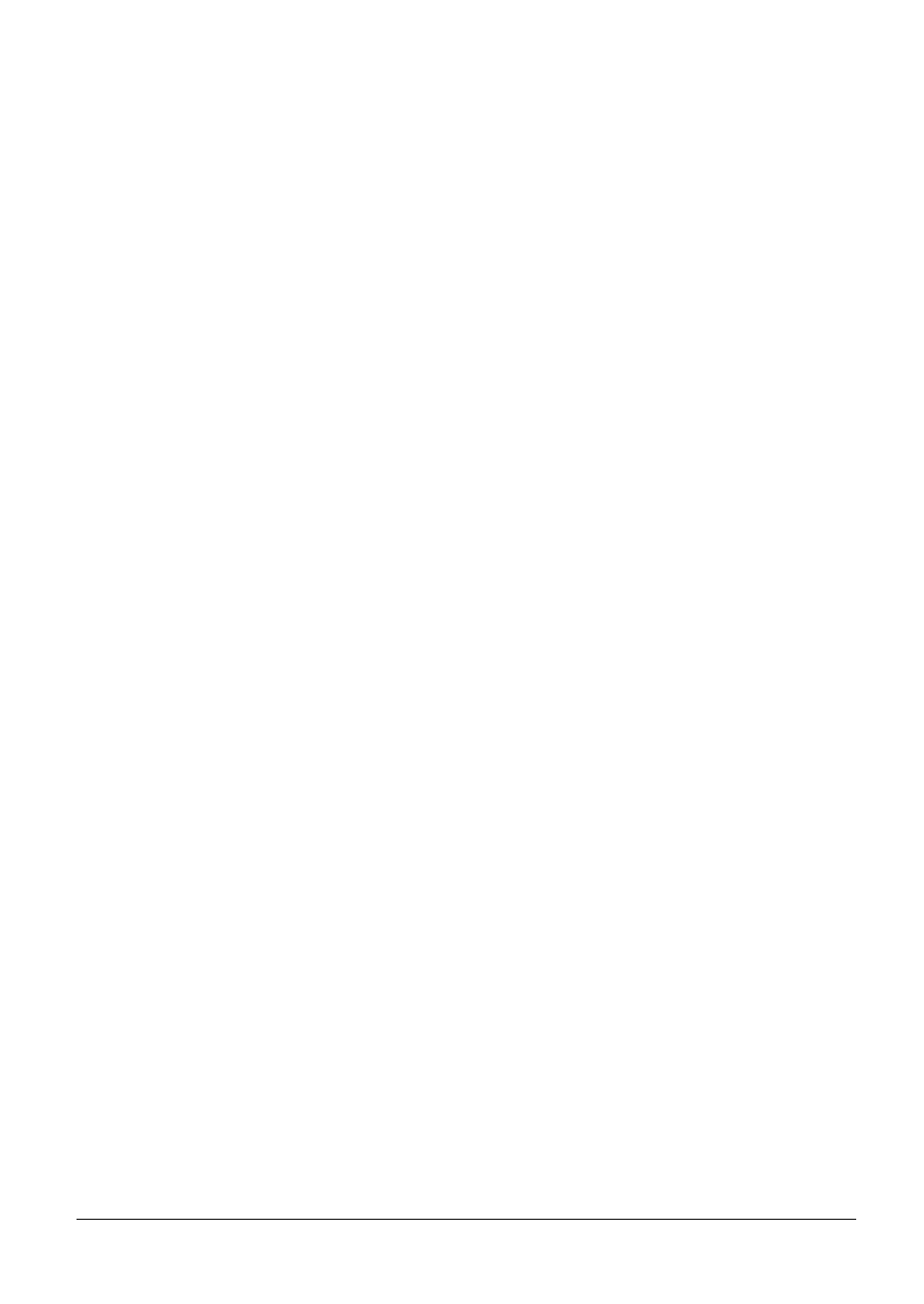
7-118
TNC 360
4 PLC Modules
8/95
Call:
PS
B/W/D/K <Axis> (0..3 for X/Y/Z/IV)
PS
B/W/D/K <Override>
(Format 0,01%)
CM 9124
PL
B/W/D
<Error code>
0: Override was set
1: Transferred axis is invalid
2: The axis is not defined as a PLC axis
3: Override value is incorrect
Error status after Call: M3171
=0: Override was set
=1: For error condition see above
4.9.11 Module 9150 Run an NC block
With module 9150 the PLC can, during an active M/S/T output, define an NC block that is then
executed after acknowledgment of the M/S/T strobe before the control continues with the NC
program. An NC program can also be defined if a program is not being run. It is then executed
immediately.
Call:
PS B/W/D/K <Command code>
PS B/W/D/K <Address the parameter block in the B/W/D range>
CM 9150
PL B/W/D <Error code>
Error code:
0 = NC block was inserted
1 = NC program was started, but no M/S/T strobe
2 = Unknown error code
3 = False address in the B/W/D range
Error status after call: M3171
= 0 NC block was inserted
= 1 for error condition see above
At present the command code <0> is implemented for TOOL CALL
Parameters :
B<Adr+0> active elements bit-coded
Bit 0 =1: Tool number, otherwise modal
Bit 1 =1: Tool axis, otherwise modal
Bit 2 =1: Spindle rpm, otherwise modal
Bit 3 =0
Bit 4 =0
B<Adr+1> Tool axis (0/1/2/3 = X/Y/Z/IV)
W<Adr+2> Tool number
D <Adr+ 4> Spindle rpm (format 0.001 rpm)