Yaskawa i80M Connecting Manual User Manual
Page 179
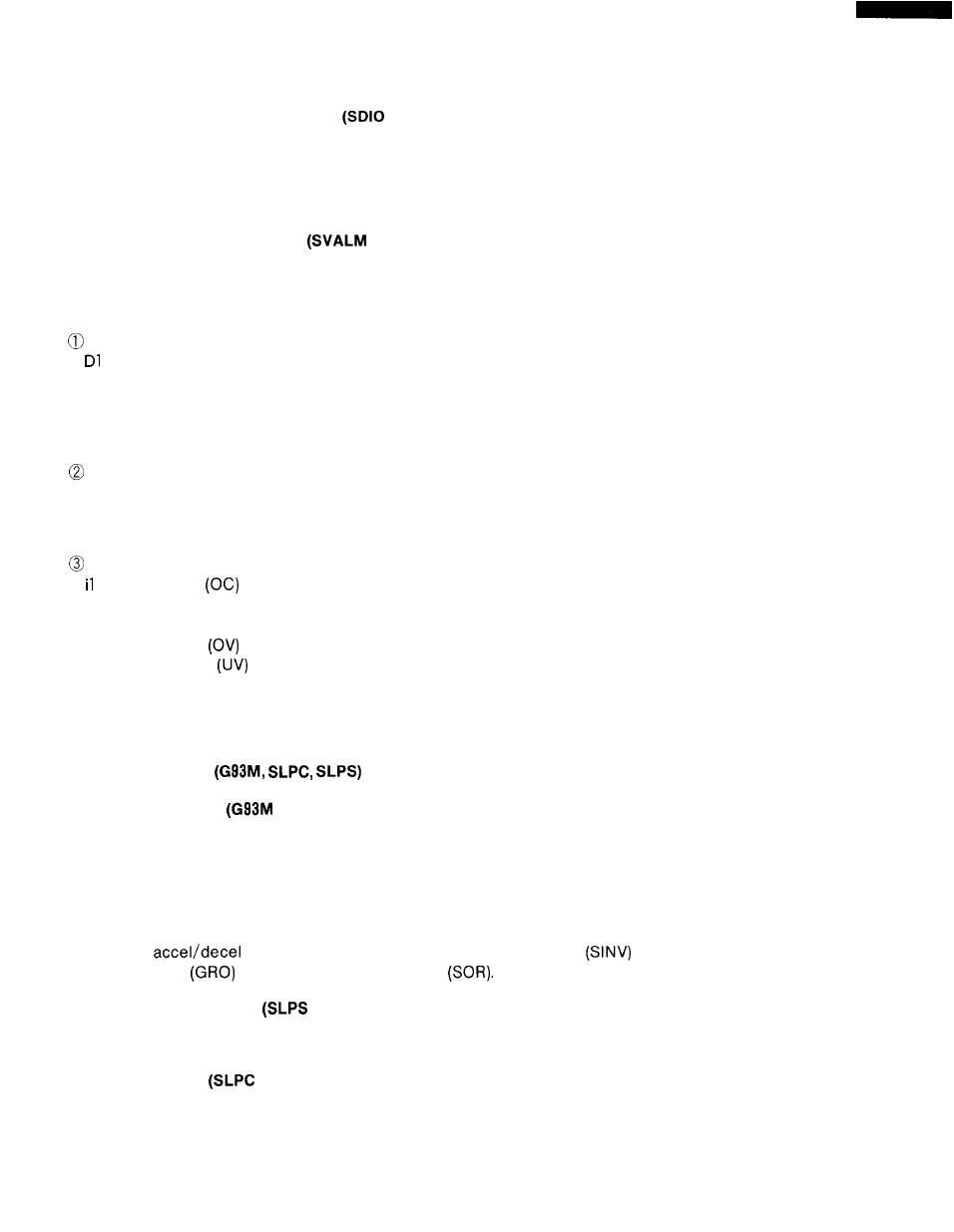
20.2.63 S COMMAND BINARY INPUTS
#31120 -sD123 #31147)
These inputs digitally sepecify the spindle speed command with 24-bit resolution instead of us-
ing an analog voltage commad. Although 24-bit resolution is provided for the NC, the actual re-
solution is limited by the output spindle drive input resolution.
20,2.64 SERVO ALARM OUTPUT
#35033)
When the control detects any of the following alarm conditions, this output signal notifies the
machine of the alarm condition.
●
Alarm conditions
Alarm conditions detected by the DSP
) Overload (LD)
D2) Runaway
D3) PG open circuit
D4) Excessive deviation
D5) Overspeed (OS)
Alarm conditions detected by the monitor CPU
Ml) Positioning error
M2) ABSO error (encoder abnormality)
M3) Communication failure
Alarm conditions detected by the i-AMP
) Overcurrent
i2) MCCB trip
i3) Regeneration failure
i4) Overvoltage
i5) Undervoltage
i6) Heat sink overheat
i7) Current command cable burnout
i8) Open phase
20.2.65 SOLID TAP
(1) Solid Tap Mode ON
# 35381)
This solid tap signal is output when G93 is executed.
The machine receives this signal and turnes on the spindle forward signal. Then, after confirm-
ing the spindle zero speed, returns the SLPC (spindle loop command input signal).
NOTE
1.
For the spindle with soft start circuit, simultaneously cancel the signal and SLPC ON.
2. To control
through NC, turn off the spindle reverse input
gear
shift ON input
and spindle orientation input
(2) Spindle Loop Command
#36512)
When NC makes the position control loop to spindle for solid tap operation, SLPS signal is out-
put. G93 block will be completed by outputting this signal.
(3) Spindle Loop ON
#31 174)
This signal is used to form the spindle control loop for NC.
NC confirms the spindle stop after this signal is ON. Then NC forms the position control loop
to the spindle and return SLPS.
179