Common cutting faults – Hypertherm HT2000-200 Volt User Manual
Page 106
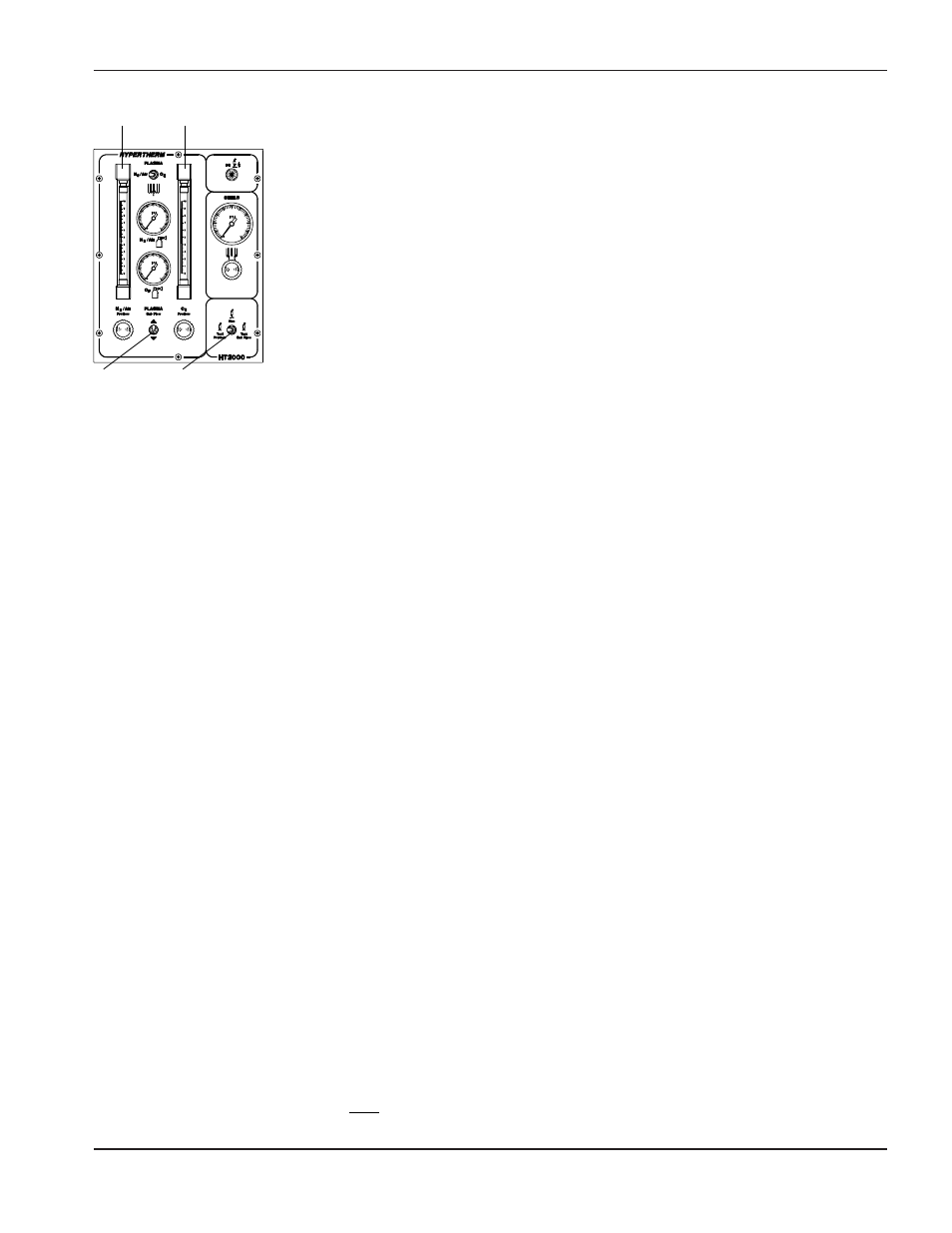
HySpeed HT2000
Instruction Manual
6-11
OPERATION
19
Adjust Cut Flow Gases and Prepare for Cutting
13. Set
S2
on the gas console to
Test Cut Flow.
14. Look at the oxygen (
FM2
) and/or nitrogen-air (
FM1
) flowmeters on the
gas console and set the
Cut Flow
plasma gas flow rate % by referring to
the
Cut Charts
and toggling the
Cut Flow
switch (
S3
) up or down.
Note: If you have changed consumable parts or if the power
supply has been off for more than one hour, purge gas
lines by leaving system in
Test Cut Flow
for one minute.
15. Set
S2
to
Run
after the test preflow and test operate flow rates have
been set.
The system is now ready for operation.
FM1
FM2
Common Cutting Faults
• Torch pilot arc will initiate, but will not transfer. Cause can be:
1. Work cable connection on cutting table not making good contact.
2. Malfunction in system. See
Section 8
.
• The workpiece is not totally penetrated, and there is excessive sparking on top of the workpiece. Causes
can be:
1. Current is set too low (check
Cut Chart
information).
2. Cut speed is too high (check
Cut Chart
information).
3. Torch parts are worn (see
Changing Consumable Parts
).
4. Metal being cut is too thick.
• Dross forms on the bottom of the cut. Causes can be:
1. Cutting speed is too slow or too fast (check
Cut Chart
information).
2. Arc current set too low (check
Cut Chart
information).
3. Torch parts are worn (see
Changing Consumable Parts
).
• Cut angle not square. Causes can be:
1. Wrong direction of machine travel.
High quality side is on the right with respect to the forward motion of the torch.
S2
S3