Yaskawa GPD503 Drive User Manual
Page 24
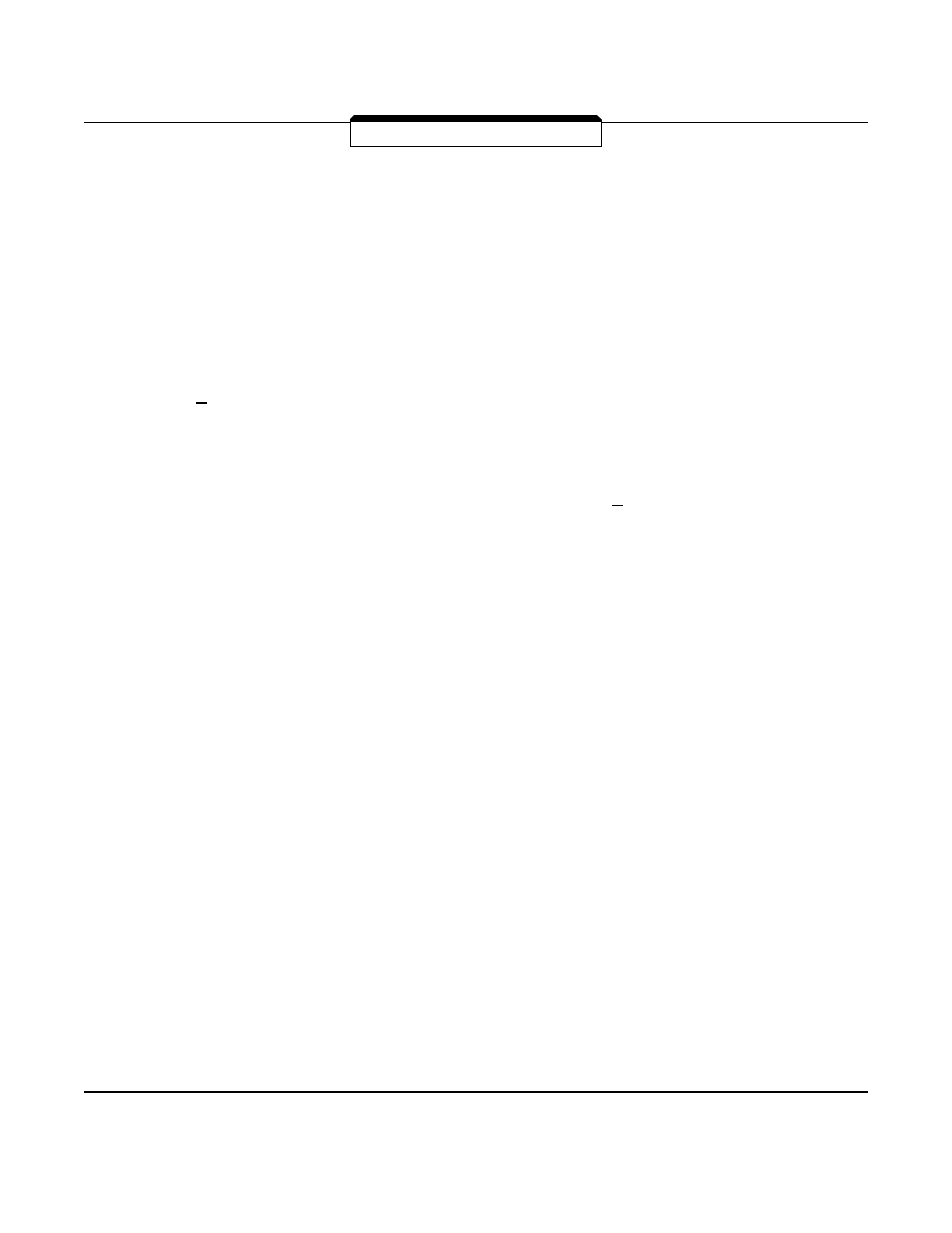
NOTES FOR FIGURE 1-3
✱
– Indicates components not supplied.
■
– Indicates customer connection terminal. Wire only to terminals shown.
( ) – Indicates alternate terminal marking, i.e., (R) and L1.
▲
– Function labels shown for these terminals are determined by factory settings of System Constants
Sn–15 through Sn-18.
●
– Function labels shown for these terminals are determined by factory settings of System Constants
Sn–20 through Sn-22.
■
– Function labels shown for these terminals are determined by factory setting of System Constant
Sn-05 ( X X X X ).
z
– Function label shown for this terminal is determined by factory setting of System Constant Sn-19.
1.
If only a remote Manual Speed pot (1RH) is used, 3SS is not needed; in that case, a jumper must be
added between terminals 5 and 11. This jumper will override both the Auto and Digital Operator
frequency references, regardless of the programming of Sn-04 X X X X. If you are using a remote speed
command or the Digital Operator, DO NOT install this jumper.
2.
The GPD 503 Electronic Thermal Overload function (Sn-17, Cn-09) meets standards set by UL and CSA
for motor thermal overload protection. If local code requires separate mechanical overload protection,
an overload relay should be installed, interlocked with the GPD 503 as shown. It should be the manual
reset type to prevent automatic restart following a motor fault and subsequent contact reclosure after
cool down.
3.
Insulated twisted shielded wire is required.
2-conductor #18 GA. (Beldon #8760 or equivalent).
3-conductor #18 GA. (Beldon #8770 of equivalent).
Connect shield ONLY AT GPD 503 END. Stub and isolate other end.
4.
Digital Operator is standard on every GPD 503. Remote operators, as shown, may not be required.
5.
Customer to connect terminal G (E) to earth ground.
6.
Wire only one Auto Reference input.
7.
If the Dynamic Braking (DB) option is used, wire per Appendix 7 instructions.
1-8