Hypertherm HPR800XD Auto Gas Rev.2 User Manual
Page 130
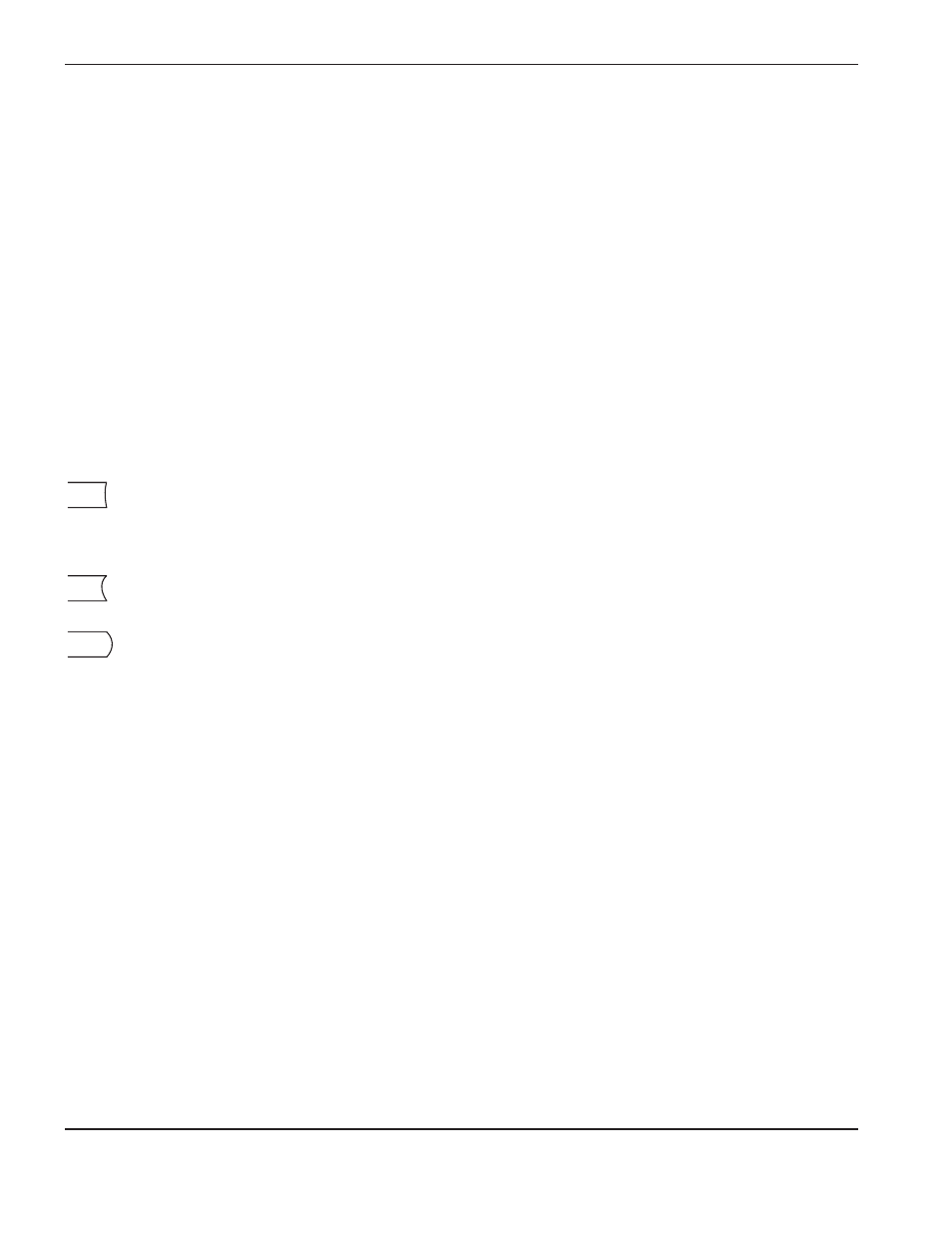
OperatiOn
4-24
HPR800XD Auto Gas –
806500
Dross
Low-speed dross forms when the torch’s cutting speed is too slow and the arc shoots ahead. It forms as a heavy,
bubbly deposit at the bottom of the cut and can be removed easily. Increase the speed to reduce the dross.
High-speed dross forms when the cutting speed is too fast and the arc lags behind. It forms as a thin, linear bead of
solid metal attached very close to the cut. It is welded to the bottom of the cut and is difficult to remove. To reduce
high-speed dross:
• Decrease the cutting speed.
• Decrease arc voltage, to decrease the torch-to-work distance.
Notes: Dross is more likely to form on warm or hot metal than on cool metal. For example, the first cut
in a series of cuts will likely produce the least dross. As the workpiece heats up, more dross
may form on subsequent cuts.
Dross is more likely to form on mild steel than on stainless steel or aluminum.
Worn or damaged consumables may produce intermittent dross.
Straightness of the cut surface
A typical plasma cut surface is slightly concave.
The cut surface may become more concave, or convex. Correct torch height is required to keep the cut
surface acceptably close to straight.
A strongly concave cut
surface
occurs when the torch-to-work distance is too low. Increase the arc voltage
to increase the torch-to-work distance and straighten the cut
surface
.
A convex cut
surface
occurs when the torch-to-work distance is too great or the cutting current is too high.
First, reduce the arc voltage, then reduce the cutting current. If there is overlap between different cutting
currents for that thickness, try the consumables designed for the lower current.