Hypertherm Phoenix 8.0 User Manual
Page 378
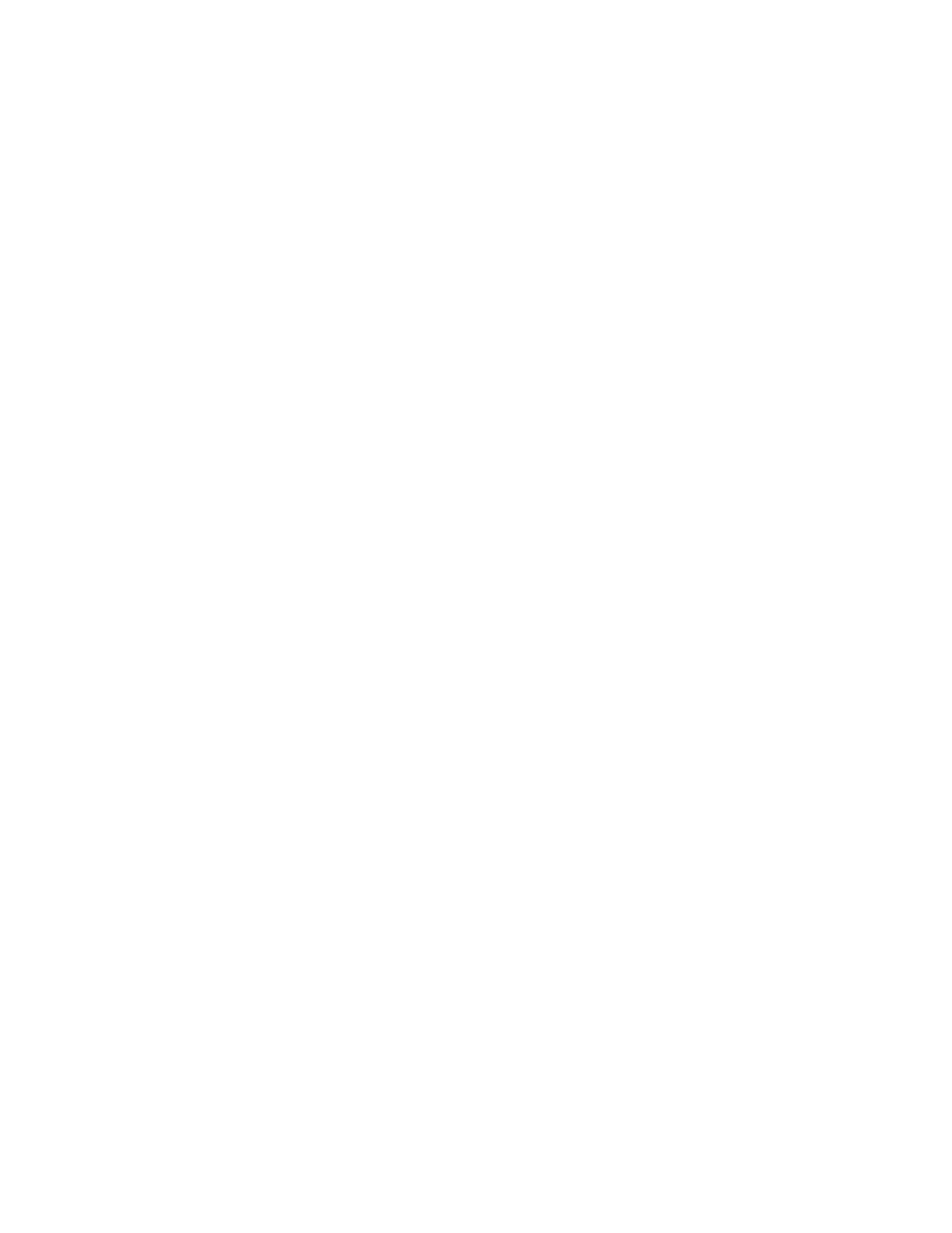
Password Setups
371
Encoder Counts per inch
Enter a value that is the number of encoder edges per inch of machine travel. It is
possible to enter fractional encoder units and the CNC will keep track of these fractions
automatically. Encoder Counts per inch are equal to the resolution of the encoder,
multiplied by the encoder revolutions per inch (based on the machine drive gearing).
For example, the resolution of a 4X – 1000 line encoder counts both edges (lines) of
channel A and channel B to equal 4 counts per line multiplied by the 1000 lines per
revolution would equal 4000 counts per revolution. If the encoder revolutions per inch to
travel is 1:1, we would have 4000 encoder counts per inch of travel.
Encoder Counts/Inch = 4 Counts/Line x 1000 Lines/Rev x 1 Rev/Inch = 4000
Note: This value should match the value used for the Rail for proper operation.
Drive Type
This parameter is used to tell the CNC what type of control loop to run. If you are
running an external velocity loop drive (indicated by having an integrated tachometer in
the motor), select Velocity. If you are running in torque mode (no tachometer), select
Current.
DAC Polarity
This parameter allows changing of the analog output polarity to establish proper control
loop feedback without any wiring changes.
Encoder Polarity
This parameter allows changing of the encoder input polarity to establish proper counting
for positive machine motion without any wiring changes.
Encoder Decode Mode
Currently the CNC only supports 4X encoder decode mode. This has been done to
increase positional accuracy.
Use Home Limit Switch
Selecting “Yes” will enable the Home feature for the Dual Gantry Axis. Note: The Z
Home Switch must first be defined and mapped to an input location in the I/O screen to
enable this feature.
Switch Offset Distance
The Switch Offset Distance is used to specify any physical position offset between the
Dual Gantry and Rail Home Switch positions. This allows the CNC to very accurately
position the two axes for operation and remove any skew of the gantry.
Backlash Compensation
The Backlash Compensation parameter is used to offset or compensate for any backlash
in the mechanics of the drive system.