Hypertherm Phoenix 8.0 User Manual
Page 449
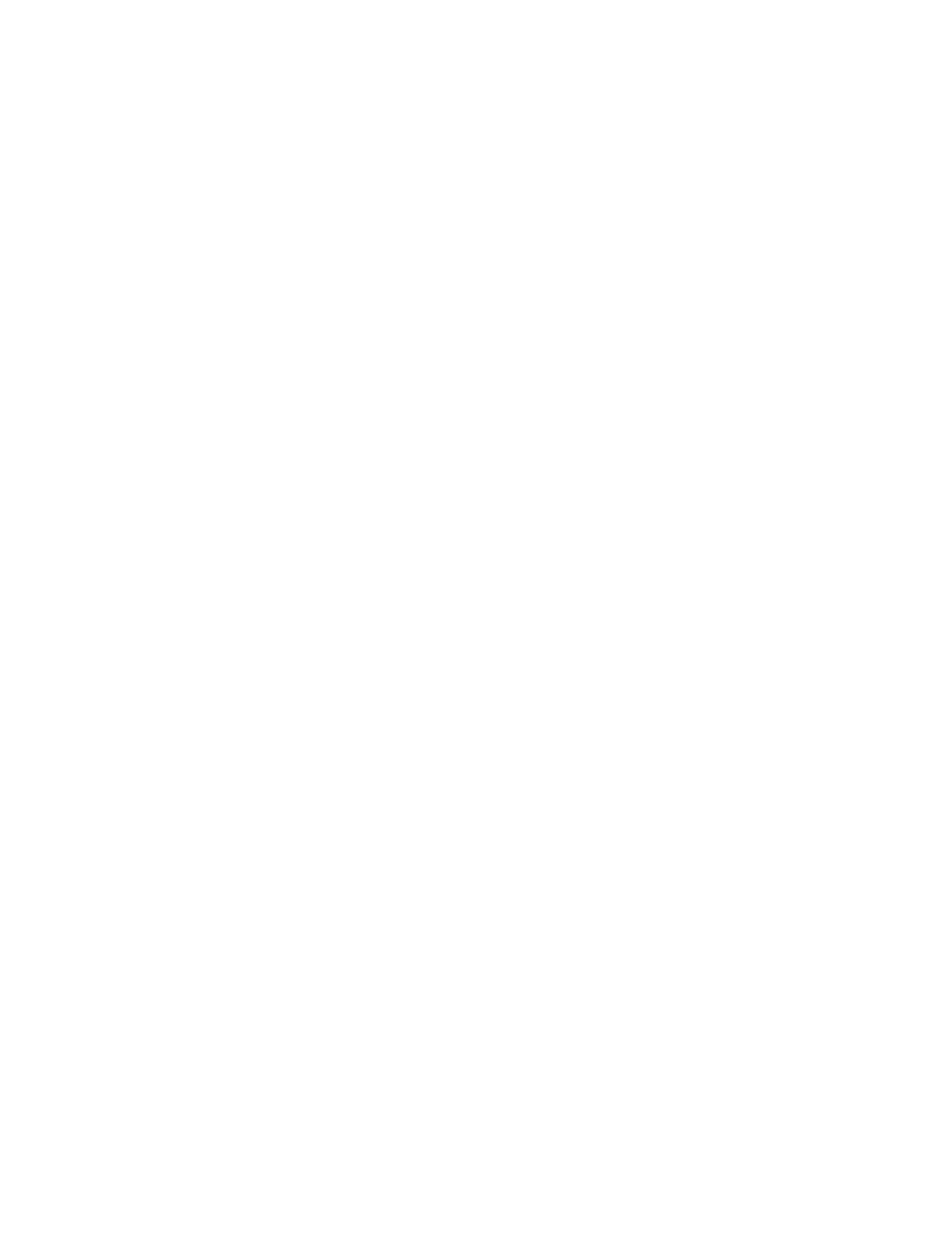
Motion Overview
442
Derivative Gain at 10% of Proportional Gain as a rule of thumb. Do not overdo
Derivative Gain as it can have a detrimental effect on the overall response of the system.
Feed Forward
Feed forward “pushes” the commanded output ahead to reduce or eliminate the difference
between the actual position and the commanded position during motion, called dynamic
following error. Feed forward corrects for a “lag” in the system and has an effect similar
to proportional gain. Do not make large increases in feed forward gain because it can
cause positive following error and excessive overshoot.
Velocity Gain
When using a current loop amplifier, the internal velocity loop in the control can provide
dampening without an external tachometer.
Using the internal velocity loop with a current loop amplifier can result in higher static
stiffness, smoother machine motion, and less overshoot.
Recommended Tuning Procedures for Hypertherm Automation Motion
Controls
Using the information previously provided as a core understanding of the position loop
process, we can now look at tuning motion for the desired motion performance. Due to
potential safety hazards and the potential possibility for machine damage from incorrect
tuning, it is recommended that this operation be performed by trained and experienced
personnel.
Prior to performing motion tuning, values for DAC Polarity, Encoder Polarity and
maximum machine speed should be calculated and entered into control setups. Servo
Error Tolerance for the axes should be set to maximum (5 inch max for X/Y motion).
Initially, it is recommended that basic tuning start with the motors disengaged from the
machine to allow the user to confirm controlled motion and response of the motion axes.
An initial Acceleration Rate of 10 Mg’s can be used to begin the motion tuning. It is
important to remember that after the motors are engaged to the machine for motion, the
load requirements for each axis will change requiring additional tuning. Additionally, if
the acceleration rate is increased after the initial tuning, additional adjustments to Gain
tuning may be required for proper machine motion.
Procedure for Velocity Type Drives
We recommend tuning the system by performing manual moves at a slow speed with all
gains set to zero with the exception of Proportional Gain. Proportional Gain should start
with a small value of 10. Engage the motors to the machine frame and beginning raising
the Proportional Gain to allow movement. If the axes start to vibrate or oscillate, this
indicates the selected gain value is too high and should be lowered. It may also require
de-tuning the response of the Drive amplifier.