Hypertherm Phoenix 8.0 User Manual
Page 380
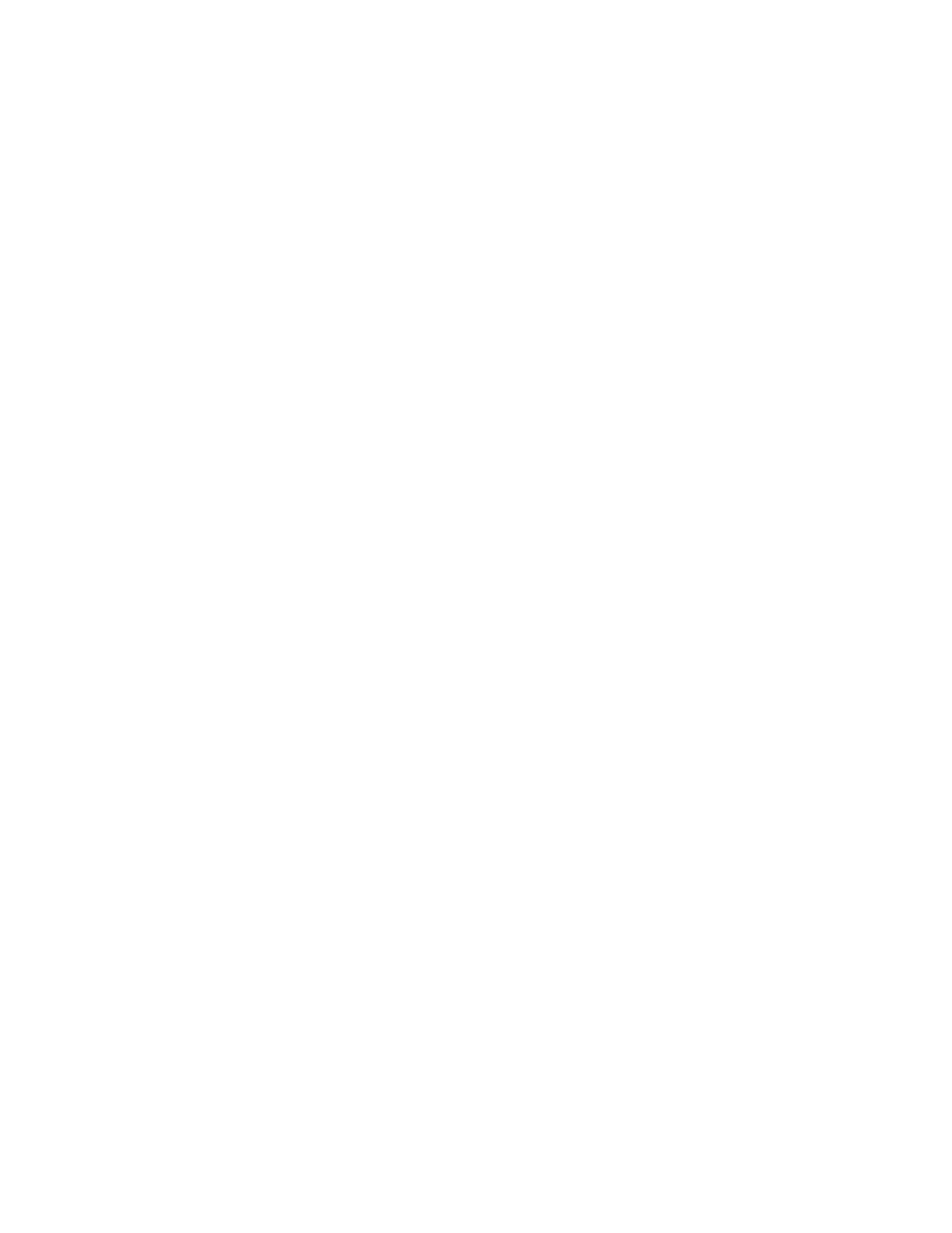
Password Setups
373
With a proportional gain too low, the system will respond in a loose or sloppy manner.
This can be seen in the test pattern when the outside corners become rounded and the
circle segments do not all meet in the center.
Integral Gain
Integral Gain improves the positioning accuracy of the control loop. Integral Gain can be
used to compensate for static friction or gravity. Excessive Integral Gain can result in
system instability.
For most shape cutting machines, this parameter should be set to zero (0).
Derivative Gain
Derivative Gain helps to dampen out sudden changes in velocity. The higher the
Derivative Gain, the slower the response time to the control loop.
For most velocity loop drives, this parameter will be set to zero (0).
Feedforward Gain
Feedforward Gain can be used to drive the following error to zero during machine
motion. In all digital control loops there is a finite amount of error that is introduced by
the velocity command. Increasing Feedforward Gain can reduce this introduced error.
Velocity Gain
When using a current loop amplifier, the internal velocity loop in the CNC can be used to
provide dampening without an external tachometer.
Using the internal velocity loop with a current loop amplifier can result in higher static
stiffness, smoother machine motion, and less overshoot.
Servo Error Tolerance
Allows the user to program the amount of servo loop Following Error to be allowed prior
to display an error message. The parameter is limited to a maximum value of 90 degrees.
Encoder Counts per rev
Enter a value that is the number of encoder edges per revolution of the Contour Bevel
Head axis. It is possible to enter fractional encoder units and the CNC will keep track of
these fractions automatically. Encoder Counts per rev are equal to the resolution of the
encoder multiplied by the encoder revolutions per rev.
For example: The Resolution of a 4X – 1000 line encoder counts both edges (lines) of
channel A and channel B to equal 4 counts per line time multiplied by the 1000 lines per
revolution would equal 4000 counts per revolution.
Encoder Counts/Rev = 4 Counts/Line x 1000 Lines/Rev = 4000
Drive Type