L6 torque detection, L6-01 torque detection selection 1, L6-02 torque detection level 1 – Yaskawa E7L Drive Bypass User Manual
Page 159: L6-03 torque detection time 1, Programming 5 - 67
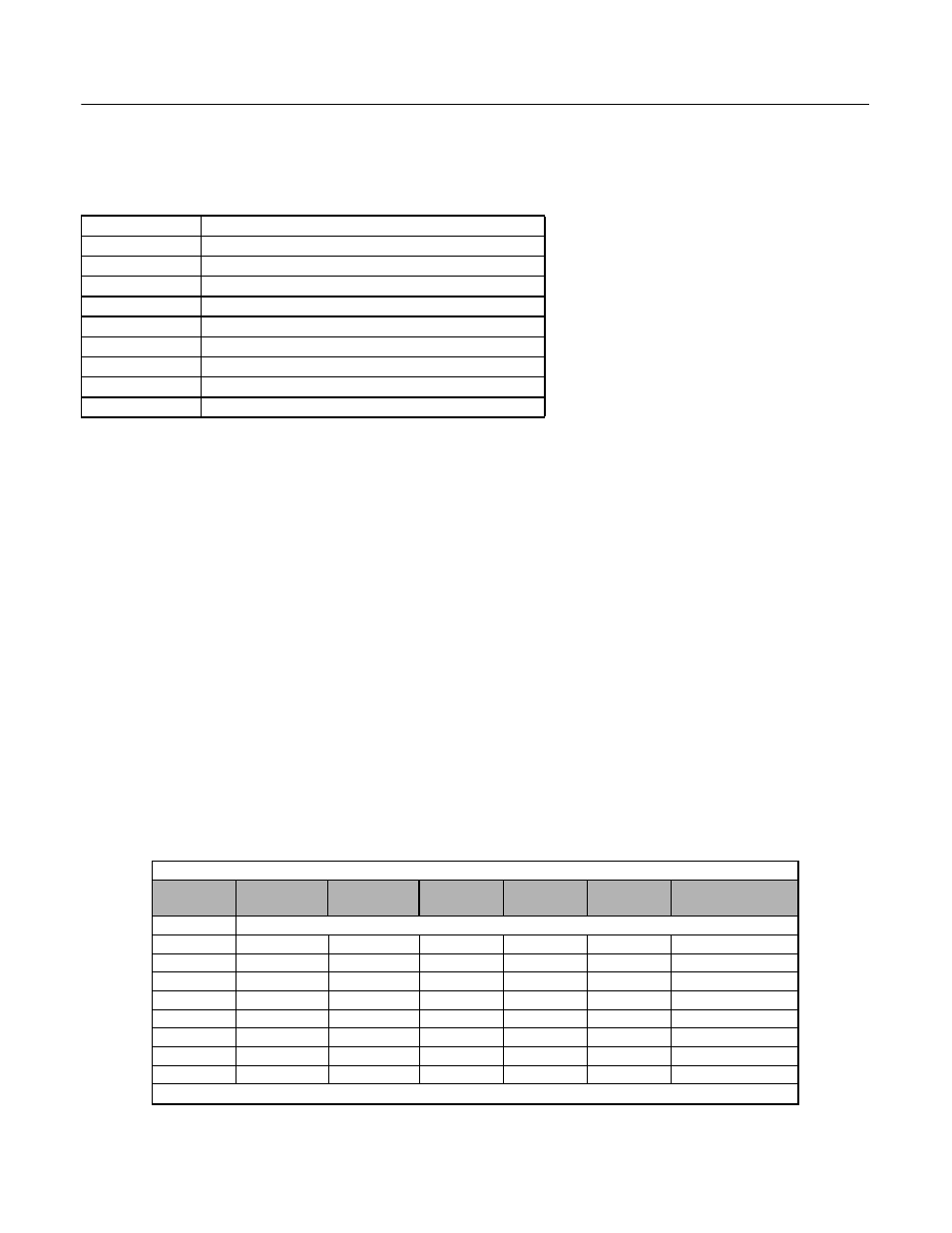
Programming 5 - 67
L6 Torque Detection
L6-01 Torque Detection Selection 1
L6-02 Torque Detection Level 1
Setting Range:
0 to 300% of Drive rated output current
Factory Default: 15% of Drive rated output current
L6-03 Torque Detection Time 1
Setting Range:
0.0 to 10.0 Seconds
Factory Default: 10.0 Seconds
The Drive can be programmed to indicate when either an overtorque or an undertorque conditions exist. A digital output must
be programmed for “Torque Detection”, (H2-01/H2-02= “B: Trq Det 1 N.O.” or “17: Trq Det 1 N.C.). A warning of an
overtorque condition can indicate a jam and an undertorque condition can indicate a broken belt, no water in a pump, or other
loss of load.
To configure Torque Detection requires the following decisions:
1. Do you wish to check for an overtorque condition or an undertorque condition?
2. Do you wish to check for the torque condition whenever the Drive is running or only at speed agree? Nuisance detection
during acceleration, when variable torques are normally required, can be avoided.
3. Do you want the Drive to fault if the torque condition is detected or only alarm and continue operation?
The following table can help choose the proper setting for Torque Detection Selection 1 to get the wanted results.
Setting
Description
0
Disabled (factory default)
1
OL@SpdAgree - Alm
2
OL At Run -Alm
3
OL@SpdAgree - Flt
4
OL At Run - Flt
5
UL@SpdAgree - Alm
6
UL at Run - Alm
7
UL@SpdAgree - Flt
8
UL At Run - Flt
Table 5.17 L6-01 Setting Choices
L6-01
Setting
Overtorque
Undertorque
Fault
Alarm
Always
Detected
Only Detected @
Spd Agree
0
Torque Detection Disabled
1
X
X
X
2
X
X
X
3
X
X
X
4
X
X
X
5*
X
X
X
6
X
X
X
7
X
X
8
X
X
*Suggested settings for Loss of Load indication