Common machine-cutting faults, 4 – maintenance – Hypertherm THC ArcGlide User Manual
Page 178
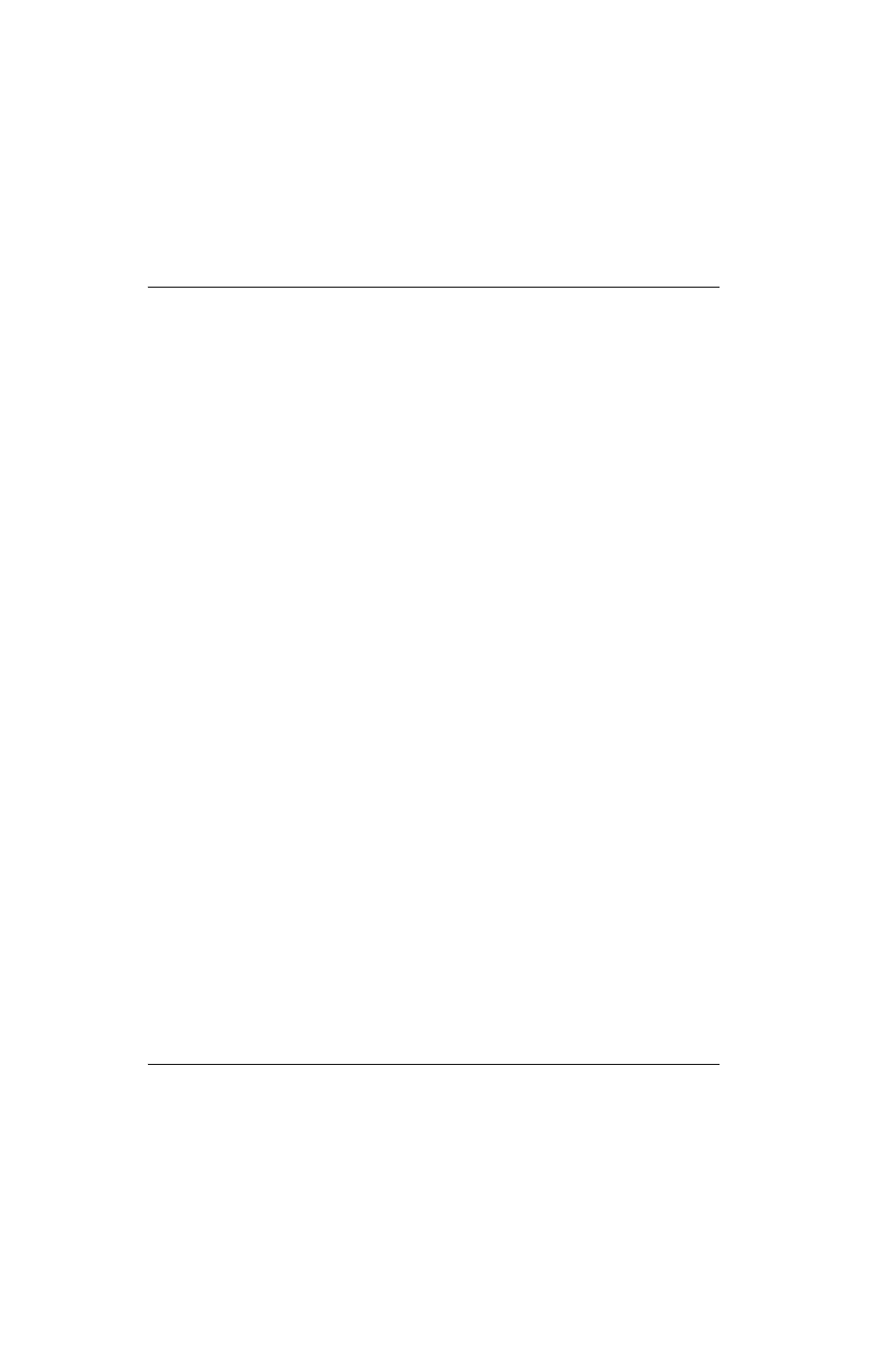
178
ArcGlide THC Instruction Manual 806450
4 – Maintenance
Common machine-cutting faults
This section lists faults an operator can encounter and the possible causes for each fault.
The arc fails to transfer.
The work lead is not making good contact with the cutting machine, or the cutting machine is not making good
contact with the workpiece.
The transfer or cut height is too large.
The surface of the workpiece is rusty, oiled, or painted.
The workpiece is not completely pierced, and there is excessive sparking on top of the workpiece.
The metal being cut is too thick for the selected amperage.
The Pierce Delay (Pierce Time in Phoenix software) is set too low.
The workpiece surface is not clean of rust or paint.
The consumables are worn and need to be replaced.
The work lead is not making good contact with the cutting machine, or the cutting machine is not making good
contact with the workpiece.
The current (amperage) is set too low. (Review the cut chart information.)
The cut speed is too high. (Review the cut chart information.)
Excessive dross forms on the bottom of the cut.
The consumables are worn and need to be replaced.
The cutting speed is too slow. (Review the cut chart information.)
A plasma system gas setting is not correct. (Review the cut chart information.)
The cut angle is not square.
The torch is not perpendicular to the workpiece.
The consumables are worn and need to be replaced.
The direction of the torch travel is incorrect. The high-quality cut is always on the right with respect to the forward
motion of the torch.
The cut height is too large or too small. (Review the cut chart information.)
The cutting speed is not correct. (Review the cut chart information.)
The current (amperage) is not correct. (Review the cut chart information.)
The torch is damaged.
The consumable life is shortened.
The arc current, arc voltage, travel speed, motion delay, gas flow rates, or cut height are not set as recommended in
the cut charts.
Attempting to cut highly magnetic metal workpiece, such as one with a high nickel content. Long consumable life is
difficult to achieve when cutting a workpiece that is magnetized or becomes magnetized easily.
Firing the torch in the air (beginning or ending the cut off of the workpiece surface). Starting at the edge is
acceptable as long as the arc makes contact with the workpiece when started.