Qualification of test personnel, Residual current devices (rcds), Higher-level systems – Hypertherm THC ArcGlide User Manual
Page 28
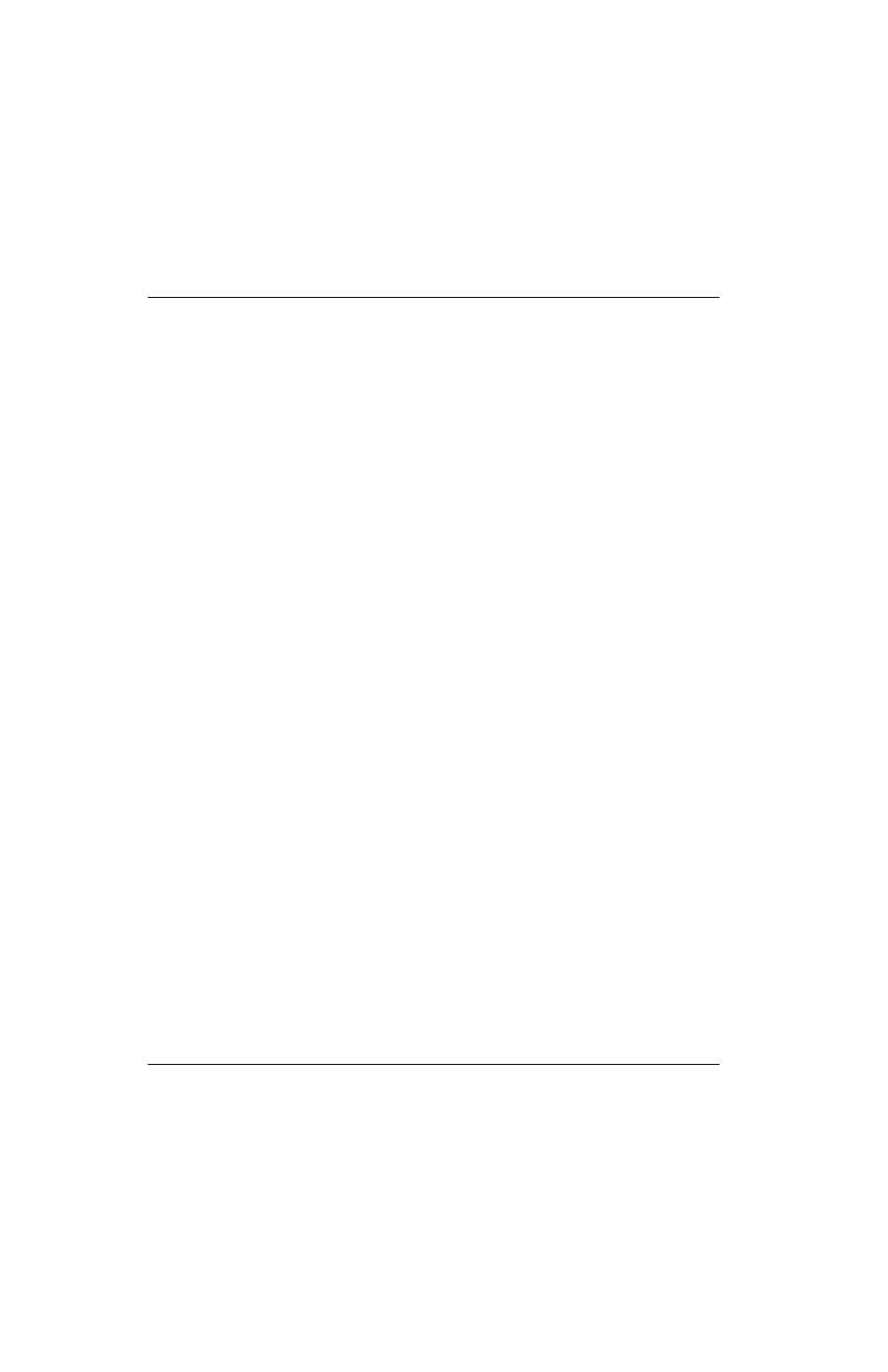
SC-28
Safety and Compliance
English
Product Stewardship
Hypertherm also removes some protective devices that would cause
false test results. Where required by local national regulations, a label
shall be attached to the equipment to indicate that it has passed the
tests prescribed by IEC 60974-4. The repair report shall indicate the
results of all tests unless an indication is made that a particular test has
not been performed.
Qualification of test personnel
Electrical safety tests for shape cutting equipment can be hazardous and
shall be carried out by an expert in the field of electrical repair, preferably
someone also familiar with welding, cutting, and allied processes. The
safety risks to personnel and equipment, when unqualified personnel are
performing these tests, may be much greater than the benefit of periodic
inspection and testing.
Hypertherm recommends that only visual inspection be performed unless
the electrical safety tests are specifically required by local national
regulations in the country where the equipment is installed.
Residual current devices (RCDs)
In Australia and some other countries, local codes may require the use of
a Residual Current Devices (RCD) when portable electrical equipment is
used in the workplace or at construction sites to protect operators from
electrical faults in the equipment. RCDs are designed to safely
disconnect the mains electrical supply when an imbalance is detected
between the supply and return current (there is a leakage current to
earth). RCDs are available with both fixed and adjustable trip currents
between 6 to 40 milliamperes and a range of trip times up to
300 milliseconds selected for the equipment installation, application and
intended use. Where RCDs are used, the trip current and trip time on
RCDs should be selected or adjusted high enough to avoid nuisance
tripping during normal operation of the plasma cutting equipment and
low enough in the extremely unlikely event of an electrical fault in the
equipment to disconnect the supply before the leakage current under a
fault condition can pose a life threatening electrical hazard to operators.
To verify that the RCDs continue to function properly over time, both the
trip current and the trip time should be tested periodically. Portable
electrical equipment and RCDs used in commercial and industrial areas
in Australia and New Zealand are tested to the Australian standard
AS/NZS 3760. When you test the insulation of plasma cutting
equipment to AS/NZS 3760, measure the insulation resistance
according to Appendix B of the standard, at 250 VDC with the power
switch in the ON position to verify proper testing and to avoid the false
failure of the leakage current test. False failures are possible because the
metal oxide varistors (MOVs) and electromagnetic compatibility (EMC)
filters, used to reduce emissions and protect the equipment from power
surges, may conduct up to 10 milliamperes leakage current to earth
under normal conditions.
If you have any questions regarding the application or interpretation of
any IEC standards described here, you are required to consult with an
appropriate legal or other advisor familiar with the International
Electrotechnical standards, and shall not rely on Hypertherm in any
respect regarding the interpretation or application of such standards.
Higher-level systems
When a system integrator adds additional equipment; such as cutting
tables, motor drives, motion controllers or robots; to a Hypertherm
plasma cutting system, the combined system may be considered a
higher-level system. A higher-level system with hazardous moving parts
may constitute industrial machinery or robotic equipment, in which case
the OEM or end-use customer may be subject to additional regulations
and standards than those relevant to the plasma cutting system as
manufactured by Hypertherm.
It is the responsibility of the end-use customer and the OEM to perform a
risk assessment for the higher-level system, and to provide protection
against hazardous moving parts. Unless the higher-level system is
certified when the OEM incorporates Hypertherm products into it, the
installation also may be subject to approval by local authorities. Seek
advice from legal counsel and local regulatory experts if you are uncertain
about compliance.
External interconnecting cables between component parts of the higher
level system must be suitable for contaminants and movement as
required by the final end use installation site. When the external
interconnecting cables are subject to oil, dust, water, or other
contaminants, hard usage ratings may be required.
When external interconnecting cables are subject to continuous
movement, constant flexing ratings may be required. It is the
responsibility of the end-use customer or the OEM to ensure the cables
are suitable for the application. Since there are differences in the ratings
and costs that can be required by local regulations for higher level
systems, it is necessary to verify that any external interconnecting cables
are suitable for the end-use installation site.