ProSoft Technology MVI56-AFC User Manual
Page 271
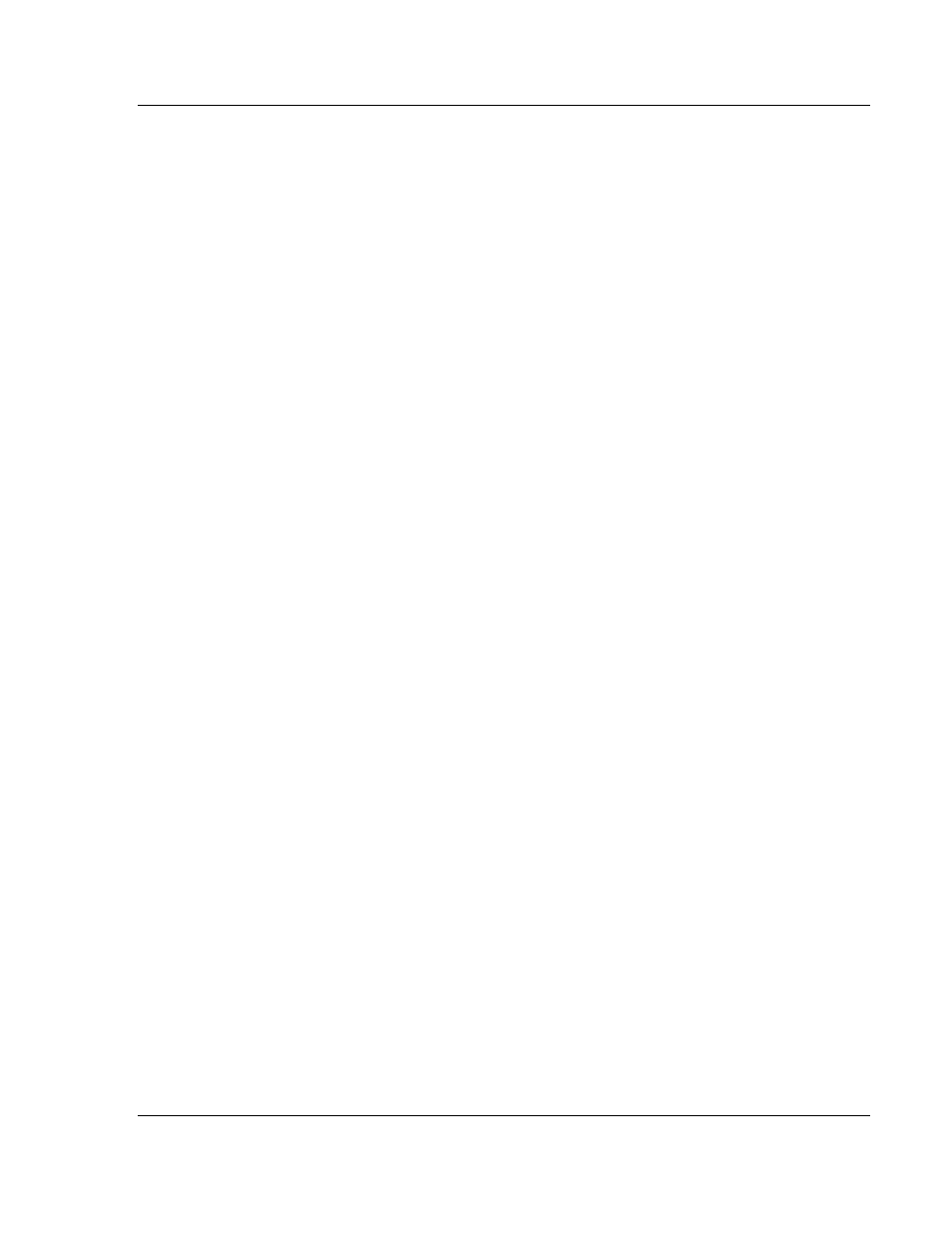
MVI56-AFC ♦ ControlLogix Platform
Reference
Liquid and Gas Flow Computer
User Manual
ProSoft Technology, Inc.
Page 271 of 316
February 25, 2011
14.1.1 On-line Communication & Configuration
The module is designed for online configuration via the configuration port. A
user-friendly Windows 95/98/2000/NT/XP-based Module Configuration and
Reporting/Monitoring Manager allows easy access to all configuration data for
editing and saving on your computer.
Project configurations may be uploaded, downloaded, and saved to disk under
user-selectable filenames. The module takes just minutes to configure using the
MS Windows-based AFC Manager.
14.1.2 Reports
Event Log Report: All security-sensitive configuration data (for example,
orifice diameter) is date and time stamped and mapped to the local Modbus
memory map. This data can be imported into any spreadsheet program and
saved to disk or printed to a local printer.
Hourly and Daily Archive Reports: Mapped to local Modbus memory. This
data can be imported into any spreadsheet program and saved to disk, or
printed as hard copy.
System Configuration: May be transferred to or from the module. The
configuration file can also be printed for hard reference or archiving.
Audit Scan: A report can be saved to disk or printed to the local printer.
14.1.3 Modbus Interface
The two Modbus Slave ports allow the unit to be used as a SCADA interface and
to broaden access to the AFC module’s data table.
Ports 2 and 3 support RS-232, RS-422 and RS-485 modes
Supports baud rates of up to 19200 baud
All ports may be configured for RTU or ASCII Modbus mode.
All Modbus Slave ports provide access to all configuration and measurement
data mapped to the Modbus table.
Module contains two internal slaves (Primary and Virtual)
Over 130,000 Modbus registers of the Primary Slave table may be re-
mapped to up to 20,000 Modbus registers of the Virtual Slave for contiguous
polling from a SCADA master.
Port 3 can be configured as a Modbus master node
Supports Modbus functions 3, 4, 5, 6, 15, and 16 as a slave (5 and 15 only on
pass-thru operation)
Supports Modbus functions 1, 2, 3, 4, 15, and 16 as a master
Scratch Pad Modbus block of 6000 words for transfer of arbitrary data
between the processor and the SCADA host via the module.