Flowserve Logix MD+ ValveSight User Manual
Page 50
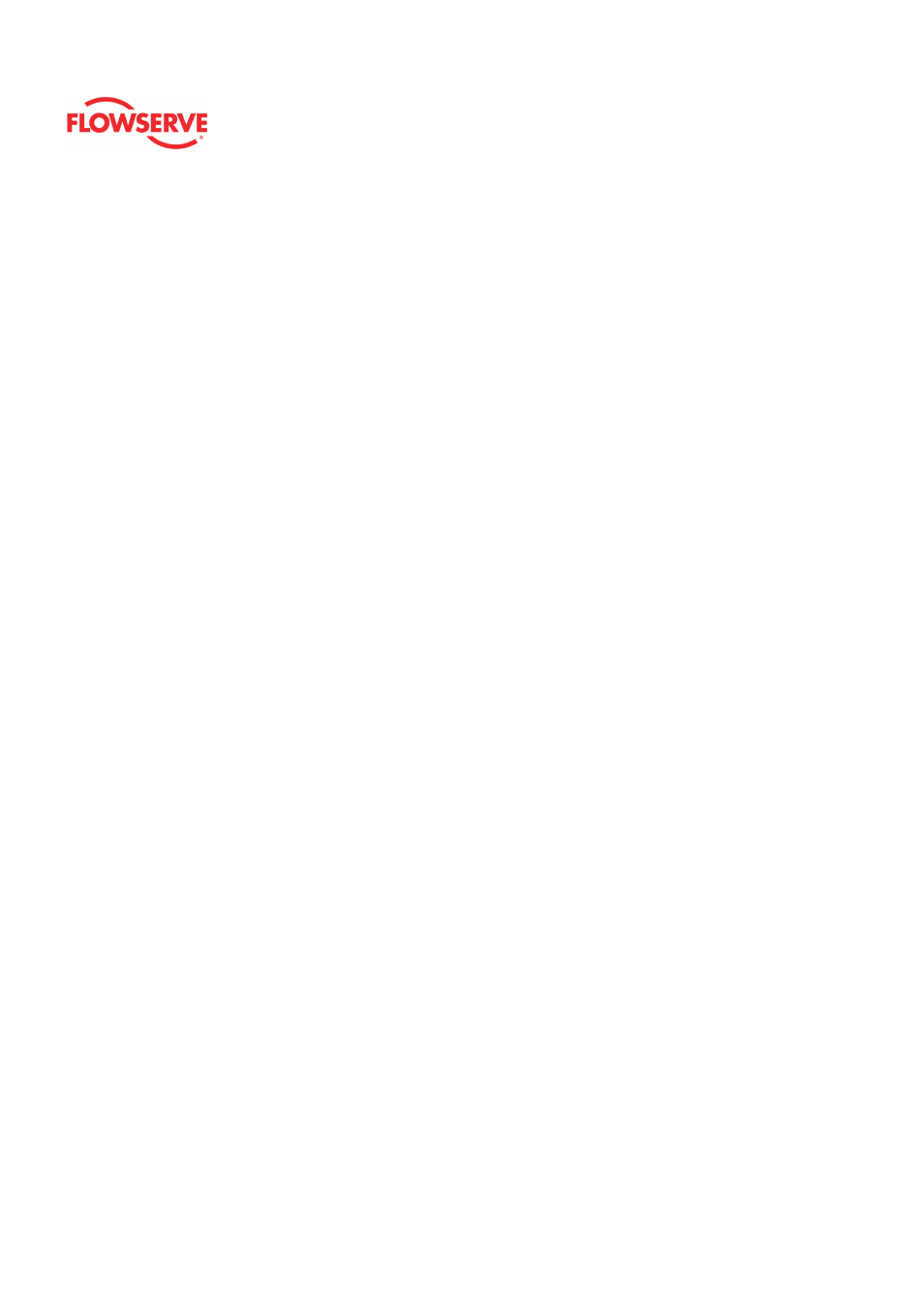
ValveSight™ Diagnostics DTM Manual for Logix MD+ Positioner with HART®
FCD-
LGENSF0014-00
© Flowserve Corporation
50
•
Possible Solutions: Check linkages and air supply to make sure the
system is properly connected. If the time out occurred because the
actuator is very large then simply retry the QUICK-CAL and the
positioner will automatically adjust for a larger actuator by doubling the
time allowed for movement. This error may be cleared by briefly
pushing the QUICK-CAL/ACCEPT.
Settle Time Out
•
Definition: During calibration, the position feedback sensor showed
movement, but did not settle.
•
Possible Solutions: Check for loose linkages or a loose positioner
sensor. This error may appear on some very small actuators during the
initial calibration. Recalibrating may clear the problem, or this error may
be cleared by briefly pushing the QUICK-CAL/ACCEPT button.
ILO Time Out
•
Definition: During calibration the Inner Loop Offset (ILO) value did not
settle. This could result in less accurate positioning.
•
Possible Solutions: Repeat the stroke calibration to get a more
accurate ILO value. To proceed using the less accurate ILO value, this
error may be cleared by briefly pushing the QUICK-CAL/ACCEPT
button. Lowering the setting on the gain selection switch may help if the
actuator is unstable during the calibration.
AO Range Small
•
Definition: During an Analog Output Calibration the difference between
the milliamp signal at 0% and the milliamp signal at 100% was too
small.
•
Possible Solutions: Recalibrate making sure to use a larger difference
between signal limits. This notification can be cleared by briefly
pressing the QUICK-CAL/ACCEPT button.
Command Range Small
•
Definition: During a Command Loop Calibration, the difference
between the signal at 0% and the signal at 100% was too small. The
system is designed to accept a difference greater than 5 mA.
•
Possible Solutions: Recalibrate making sure to use a larger
difference between command signal limits. The difference must exceed
5 mA.
Command < ADC Range
•
Definition: During Command Loop Calibration, the 0% signal was out
of the Analog to Digital Converter (ADC) range.
•
Possible Solutions: The system is designed to accept a signal that is
above 10 ADC counts. Recalibrate making sure the ADC counts are
above that limit.
Command > ADC Range
•
Definition: During Command Loop Calibration, the 100% signal was
out of the Analog to Digital Converter (ADC) range.
•
Possible Solutions: The system is designed to accept a signal that is
below 4085 ADC counts. Recalibrate making sure the ADC counts are