Stop> input and output register map, Decel, 1 to max. deceleration in rda, (ml3**28) – Yaskawa MP2000 User Manual
Page 104: Stop> block fault condition
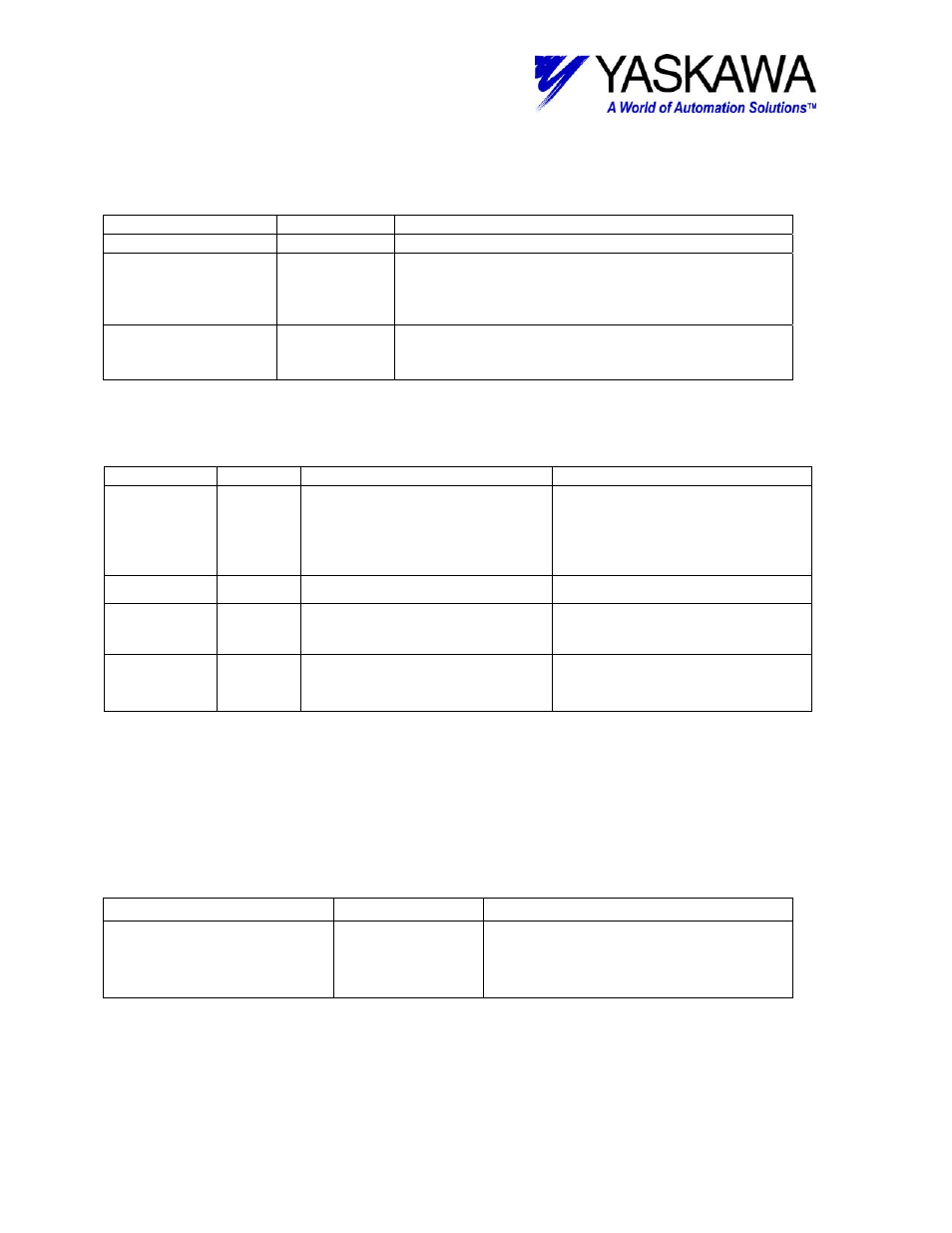
TECHNICAL NOTE
<STOP> Input and Output Register Map
Output Registers
Output Type
Description
RUNNING
Bit
High while block has control and move is in progress.
DONE
Bit
Goes high when the axis comes to a full stop. IE.
actual speed feedback in RDA is zero (ML3**16=0),
and motion command mode feedback indicates zero
(IW3**16=0) When the axis stops completely,
ERROR
Bit
Latches high if any error occurs in block (see table
below) or on the servo axis (see IL**02 and IL**04).
This is Reset if EXECUTE bit goes low.
Input Registers
The following registers are used as inputs to the function block. They select the options
and define the parameters that the user needs to make the function work as necessary.
Input
Type
Description
Range and state
Execute
Bit
Block enable
Rising edge executes block
TRUE – nothing else can take
control of the axis
FALSE & Block Done - Block
disabled, all outputs set to zero
AXIS
Word
Axis number related to the block.
1~16
DECEL
Long
Deceleration during stop in counts
per second squared.
1 to Max. Deceleration in RDA,
(ML3**28).
DATA09W
Address
Address of the first working
register.
Nine words of register space are
used by this function.
<STOP> Block Fault Condition
The following table outlines several situations that may cause an error, and will turn on
the blocks “Error” output bit. The block “Error” output will cleared if the EXECUTE bit
goes low, but the Error ID (MW3**81) will remain in the RDA. To reset the Error ID, use
the Alarm Reset Function Block.
Note that each axis has its own Error ID stored in its RDA axis section, offset by 200 for
each axis. Example: Axis#1 stores to MW30181, Axis #2 stores to MW30281, etc.
Internal error bit
Cause
Attention
axisinerr
AB00000F
The axis number
entered on the
input is not an
acceptable value
The function blocks can only control 1 to
16 axis. Any value greater or smaller then
this will cause an error. This does not set
the RDA Error ID.
File: MP2000_IndividualFunctionDocument_RevC 104/168
Doc Number: eng.MCD.05.101
11/17/2005