Gear> function block operation notes – Yaskawa MP2000 User Manual
Page 35
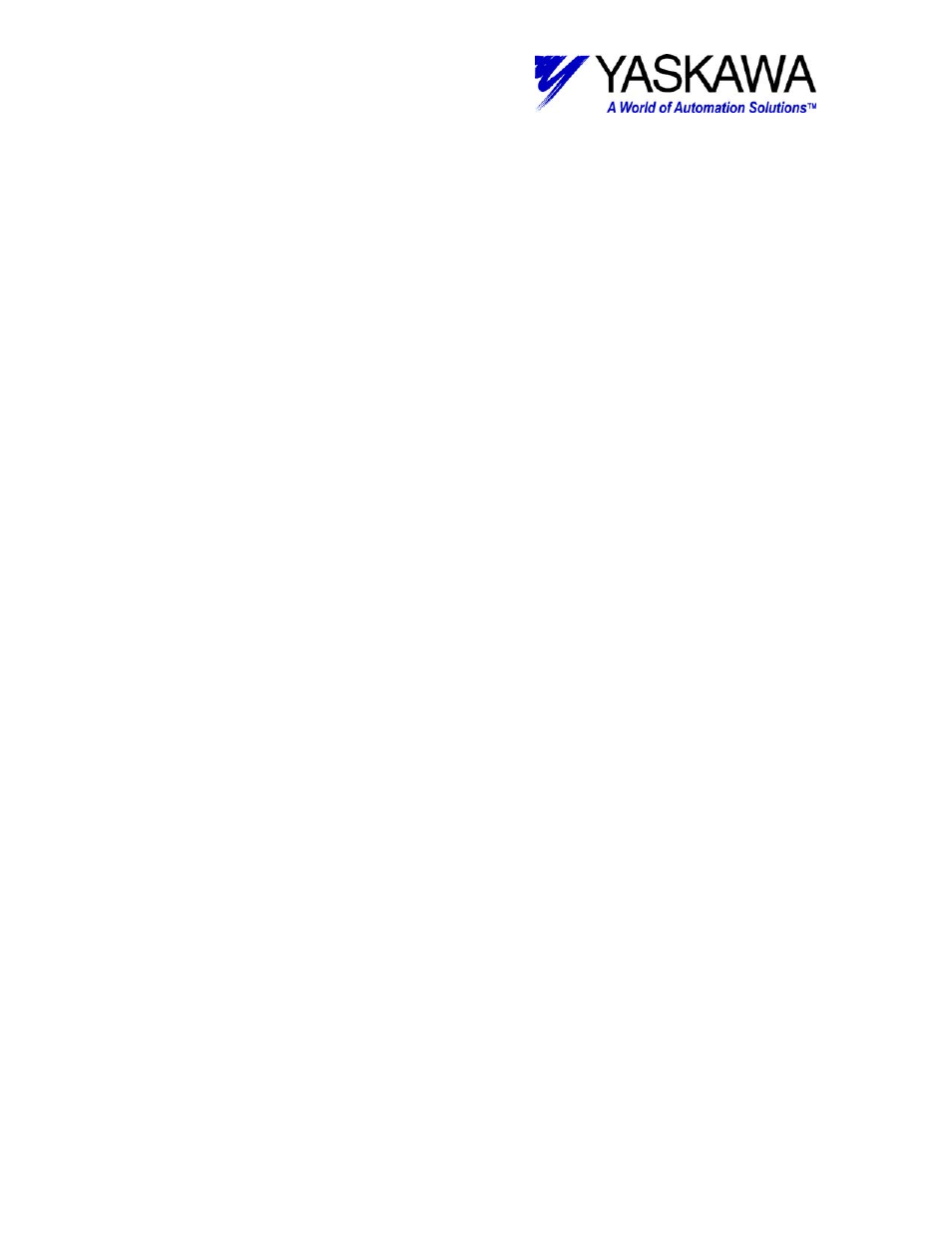
TECHNICAL NOTE
File: MP2000_IndividualFunctionDocument_RevC 35/168
Doc Number:
EF.MCD.05.101
11/17/2005
<GEAR> Function Block Operation Notes
• Slave Offset and Change Dynamics function blocks may be useful when using
this block.
• Rising edge of EXECUTE input initiates block operation, and several block input
values are read once. These inputs are: RIGID, AXIS, MSTR-SLV. This event
will also verify & set the ACCEL & DECEL values in the servopack to zero. Note
that this only means that the MP controller will control the ACCEL/DECEL rates
as set in the RDA (acceleration time (ML3**46) and deceleration time (ML3**48))
and the servopack will not limit the accel/decel.
• IMPORTANT NOTE: Gearing sets Acceleration and Deceleration in the
servopack to 0 ms. (acceleration time (ML3**46) →(OL**36), →(Pn80B), and
deceleration time (ML3**48) →(OL**38) →(Pn80E)). In Gearing the Accel/Decel
rates are controlled inside the Gearing block.
After the Gearing Block is used
and its motion has stopped (motion command IW**08=0), before initiating any
other motion blocks, a Change Dynamics block must be used to restore the
Accel and Decel values in the servopack. This will restore the expected
operation of the other motion blocks.
• The following inputs are always read when EXECUTE bit is high: GEARIN,
GEAROUT, RATIO-N, RATIO-D, RAW-DATA.
• To use the function block, the EXECUTE bit must be held ON. If the EXECUTE
bit goes OFF while axis is gearing, the block will set the axis in speed mode
(Motion command 7(constant speed sending)) at the speed it was going at that
moment, but all outputs will be set to zero.
• If the GEAROUT bit goes high while the execute bit is high, and the block is
gearing, then the axis will decelerate to a stop, at the set deceleration in the
RDA.
• The Slave offset value in the RDA is set to zero when the gearing block is
engaged.
• If the RIGID input is set high, the slave axis will be set in a phase lock mode at
GEARIN timing. The slave will over-speed (limited to max speed of slave) to
catch up in position if necessary, when the slave axis matches the (master phase
position)*(gear ratio), and (master speed)*(gear ratio), the tracking bit will turn on.
See graph below.
• If the RIGID input is set low, the slave axis will only speed match. The slave axis
will ramp up to speed, when the slave axis matches speed of the master, the
tracking bit will turn on.
• The
GEARING
output bit will be held high as long as the EXECUTE input is held
high and the GEAROUT bit stays low, and no other block takes control.
• The maximum speed the slave axis can operate at is limited by the RDA
Maximum speed setting for that axis. If the master pulse input commands the
slave to go faster then this speed, the axis will travel at the max. speed, set the
ERROR output to high, and set the TRACKING output to low. The error bit will
return to off state when commanded speed becomes less than max velocity
setting. An error bit will be registered in the RDA. Note that this condition does
not occur during acceleration over-speed for rigid gearing.