Provided in, Table 33, Listed in – Yaskawa CIMR-LU Drives User Manual
Page 109
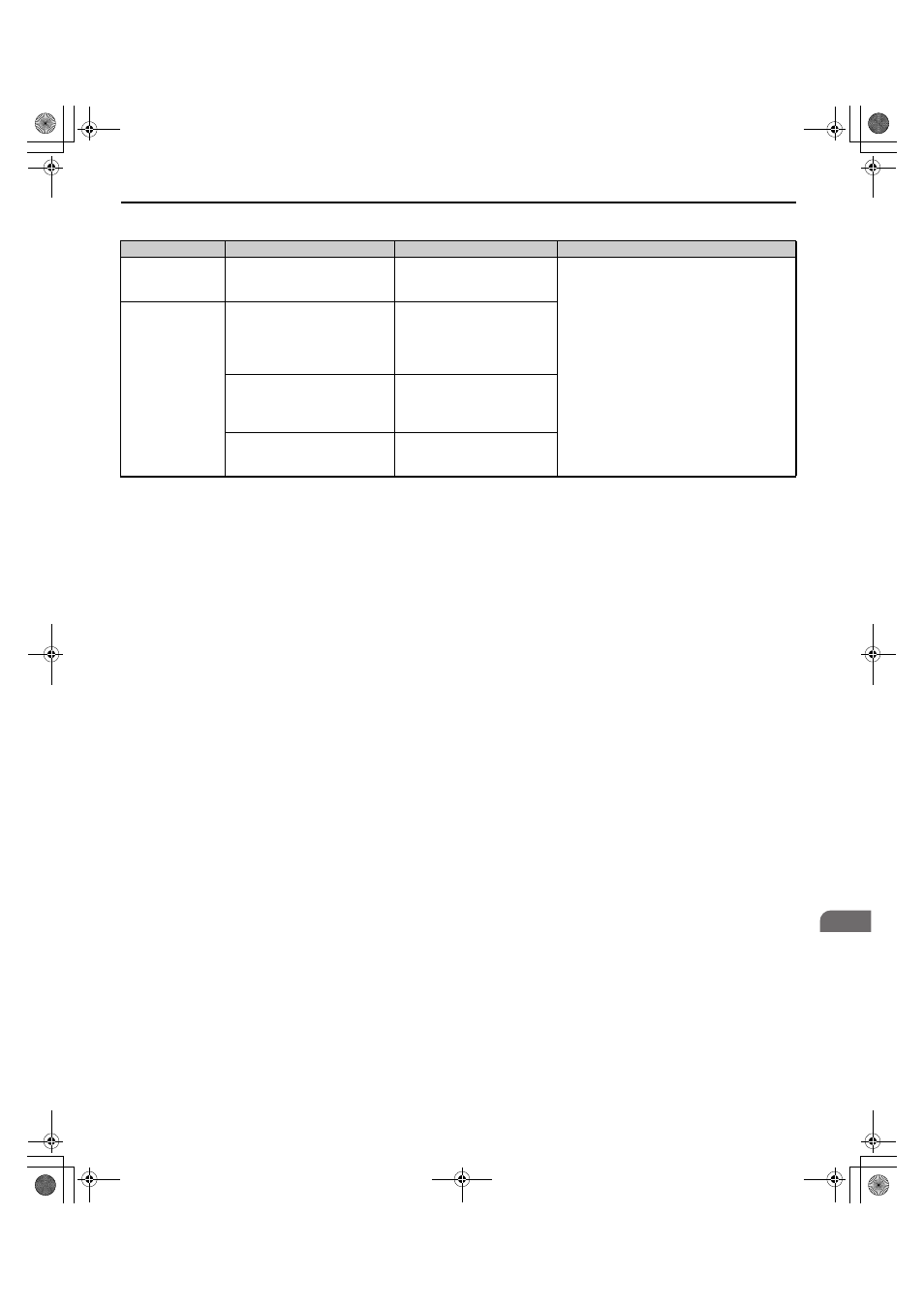
4 Start-Up Programming & Operation
YASKAWA ELECTRIC TOEP C710616 38F YASKAWA AC Drive L1000A Quick Start Guide
109
S
tart-U
p
Prog
rammin
g
&
Op
er
at
io
n
4
Table 33 Power Supply Ratings for Rescue Operation
Parameter Setup
Adjust drive parameters as described below when using Rescue Operation.
• Select the type of Rescue Operation power supply for the drives main circuit in parameter S4-06.
• When using a UPS, set the UPS power value to parameter S4-07. Use parameter S4-08 to decide if the Rescue
Operation speed shall be limited automatically depending on the UPS power.
• If deterioration of the battery or UPS shall be detected, also set up parameters S4-12 and S4-13. Measure the DC bus
voltage during operation using the rescue power supply and set the measured value to parameter S4-12. Set the
deterioration detection level to parameter S4-13.
• Set parameters S4-01 to S4-04 if light load direction search shall be automatically performed when Rescue Operation is
started.
Wiring Examples
Switching the main power supply to a battery or UPS requires magnetic contactors that must be controlled by an external
controller. Wiring methods and the sequence used for the magnetic contactors depend on the application. This instruction
manual describes the following configurations:
• A single-phase, 230 V UPS is used as backup power supply for a 200 V, 400 V or 600 V class drive.
• Two separate batteries for the main power and control power supplies. Main power battery voltage is below 250 Vdc for
200 V class drives, 500 Vdc for 400 V class drives, or 720 Vdc for 600 V class drives.
• Two separate batteries. One is used for the main power supply, a second battery supplies the controller via an optional
24 V Backup Power Supply Unit.
• A single battery with minimum 250 Vdc for 200 V class drives, 500 Vdc for 400 V class drives, or 720 Vdc for 600 V
class drives is used for the main and control power supply.
Select the configuration that matches your application. Follow the corresponding instructions for wiring and drive
settings. For configurations not covered in the list above, contact your Yaskawa representative or our sales office directly
for consultation.
Motor Type
Speed Feedback
DC Bus Voltage
Control Circuit Voltage
Induction Motor
Without PG Encoder or
Incremental PG Encoder with PG-
B3 or PG-X3 option card
200 V class drives: 48 to 340 Vdc
400 V class drives: 48 to 680 Vdc
600 V class drives: 48 to 850 Vdc
When supplied from a battery or the drive DC bus:
200 V class drives: 250 to 340 Vdc
400 V class drives: 280 to 680 V (recommended:
500 to 680 Vdc)
600 V class drives: 280 to 850 V (recommended:
720 to 850 Vdc)
When supplied via a 24 Vdc control power backup
unit:
200 V, 400 V and 600 V class drives: 24 Vdc
Permanent Magnet
Motor
Incremental PG Encoder with PG-
X3 option card
“End8” to “End10” error occurs
during Initial Magnet Pole Search
Auto-Tuning.
200 V class drives: 280 to 340 Vdc
400 V class drives: 560 to 680 Vdc
600 V class drives: 700 to 850 Vdc
Incremental PG Encoder with PG-
X3 option card
No error occurs during Initial
Magnet Pole Search Auto-Tuning.
200 V class drives: 72 to 340 Vdc
400 V class drives: 144 to 680 Vdc
600 V class drives: 207 to 850 Vdc
Absolute PG Encoder with PG-F3
or PG-E3 option card
200 V class drives: 48 to 340 Vdc
400 V class drives: 48 to 680 Vdc
600 V class drives: 48 to 850 Vdc
TOEP_C710616_38F_5_0.book 109 ページ 2013年12月4日 水曜日 午前9時56分