Hypertherm V9 Series Phoenix Rev.11 User Manual
Page 107
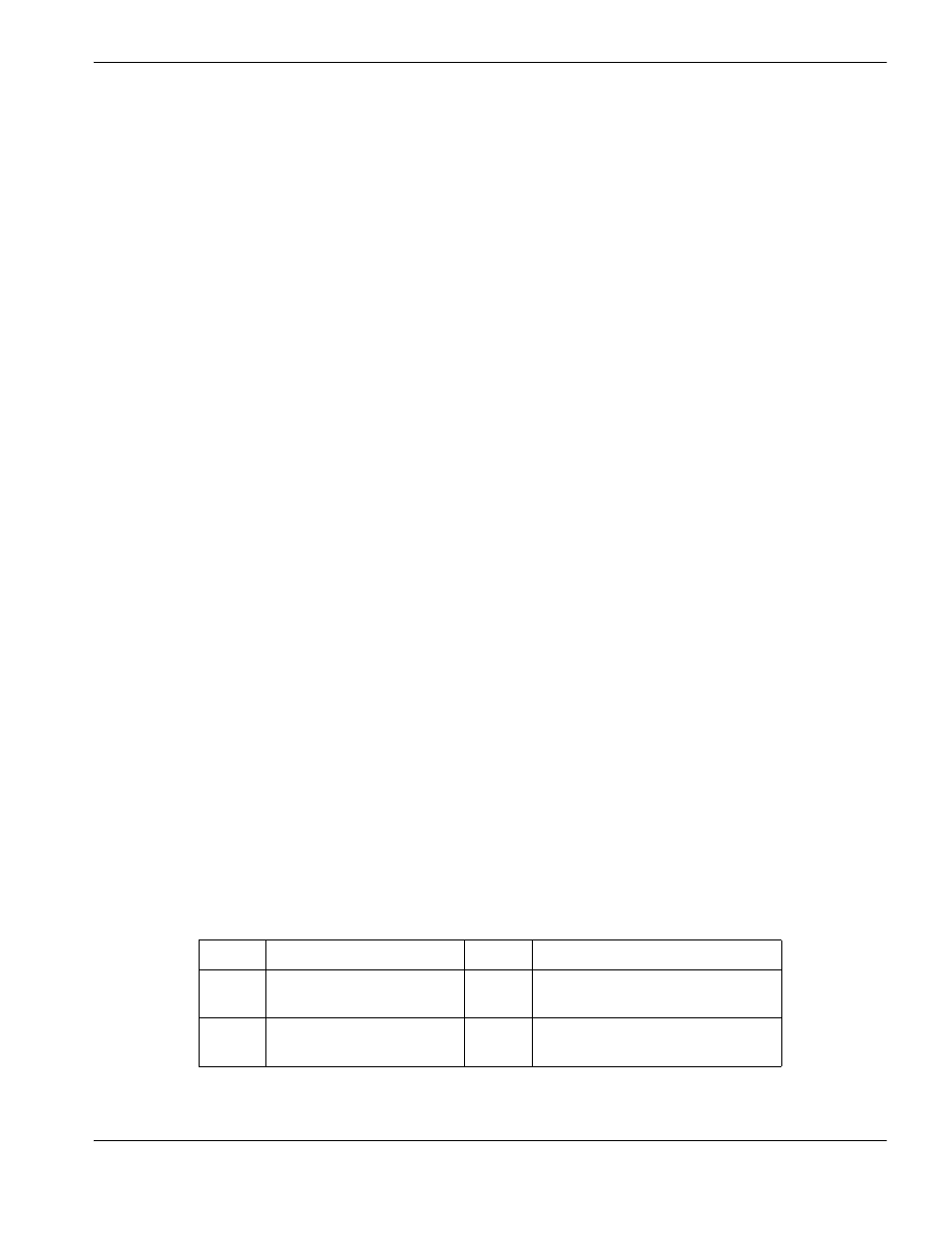
Phoenix 9.76.0 Installation and Setup Manual 806410
107
3 – Torch Height Control Axis Setup
Servo Error Tolerance
Servo Error Tolerance is the maximum amount of servo following error. If the cutting system accumulates following error
that exceeds the Servo Error Tolerance them motion stops and the CNC displays an position error. Set the Servo Error
Tolerance to three times the steady-state following error when traveling at the maximum speed. The maximum speed
represents the most demanding moves for the lifter and should result in the highest following error.
Use the following test to determine the steady-state following error when traveling at the maximum THC speed.
Note: Before running the test, remove the torch from the lifter to prevent any damage to the torch when you jog
the lifter up and down.
1. Choose Setups > Watch, then choose Following Error for the THC axis.
2. In Machine Setups > Speeds, set the THC Home/Fast IHS Speed to the same value as Maximum THC Speed.
3. Choose Manual (press F11 on the keyboard, or choose the Manual icon) > Manual Options, then select Fast IHS
Speed for THC Jog Speed.
4. Jog the lifter from the top to the bottom of the slide several times and record the highest following error shown during
the test.
Note: If the following error continues to increase instead of reaching a steady-state, the acceleration setting for
the THC axis may be set too high. On the Machine Setups > Speeds screen, enter a lower value for THC
Acceleration Rate. Repeat step 4 and observe the following error again. If the following error does not level off to
a steady state, decrease the THC Acceleration Rate again.
5. Multiply the following error by 3 and enter it as the value for Servo Error Tolerance in the Machine Setups > Sensor
THC Axis screen.
6. Return to the Speeds screen and reset THC Home/Fast IHS Speed to its original value (For Sensor THC, 1270
mm/min or 50 inches/min).
Stall Force Tolerance
Stall force is a method of detecting the workpiece during initial height sense. Use stall force when cutting underwater or
in other conditions in which ohmic contact is not feasible. Stall force is a measure of following error that accumulates
when the torch tip contacts the workpiece and the lifter continues downward movement but is stopped by the workpiece.
When the following error exceeds the stall force tolerance value, the CNC knows the position of the workpiece and
retracts the torch.
For best operation, use a drive that provides a current limit input, such as the Yaskawa drive provided with Hypertherm’s
Sensor THC. Connect the THC Torque Limit output from the CNC to the current limit inputs of the drive. Using the
software provided by the drive manufacturer, identify the current limit parameters and set them to reduce current when
the THC Torque Limit output is on. The Yaskawa Sigma II drive has these parameters:
Code
Description
Value
Comment
CLMIF
Forward External Torque
Limit
20%
Downward motion during IHS
CLMIR
Reverse External Torque
Limit
200%
Upward motion during IHS and
homing.