Hypertherm V9 Series Phoenix Rev.11 User Manual
Page 62
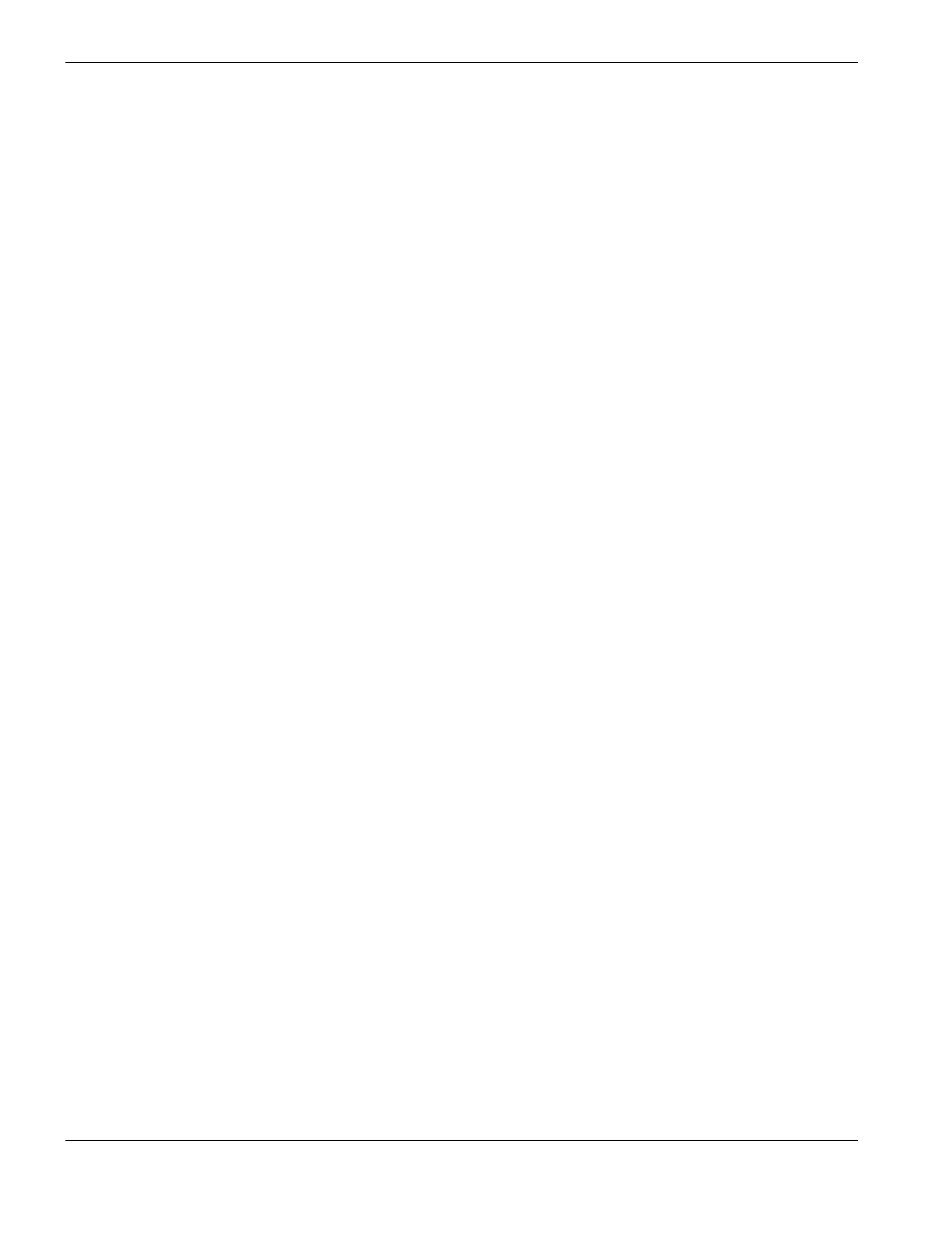
62
Phoenix 9.76.0 Installation and Setup Manual 806410
2 – Machine Setup
Drive Type: This parameter is used to tell the CNC what type of control loop to run. If you are running an external velocity
loop drive (indicated by having an integrated tachometer in the motor), select Velocity. If you are running in
torque mode (no tachometer), select Current.
DAC Polarity: This parameter allows changing of the analog output polarity to establish proper control loop feedback
without any wiring changes.
Encoder Polarity: This parameter allows changing of the encoder input polarity to establish proper counting for positive
machine motion without any wiring changes.
Encoder Decode Mode: Currently, the CNC only supports 4X encoder decode mode. This has been done to increase
positional accuracy.
Use Hardware Overtravels: Select whether the cutting system will be using hardware overtravel switches. If Hardware
overtravel switches are used, the CNC will disable feedback and display an error message if the inputs
become active. It is recommended that hardware overtravel switches be installed.
Backlash Compensation: The Backlash Compensation parameter is used to offset or compensate for any backlash in
the mechanics of the drive system. The maximum value for backlash compensation is 12.7 mm (.5 in).
Home: The Home parameter is used to activate use of the Home feature. Depending on configuration, the table may be
Homed to either a designated home switch or an overtravel switch.
The Home feature is used to set a known absolute physical position location on the cutting table that is used
for referencing future manual Go to Home and other motion commands. This is generally performed through
activation of a home switch positioned on the appropriate axis giving it a known physical location.
When you enter a homing command, the CNC moves the axis toward the home switches at the Fast Home
Speed until the switches activate. Once the switches activate, motion stops and then the axis moves in the
opposite direction off switch at the Slow Home Speed. The moment that the switch deactivates, the CNC
records the position which provides an absolute reference point for future motion commands.
Absolute Home Position: Defines the position of the axis when the Home Limit Switch or Marker Pulse is detected.
Home Offset Distance: Allows the user to set an offset distance from the Home Limit Switch.
Home Direction: Determines which direction the axes will travel during phase one of the homing sequence.
Use Marker Pulse: When enabled, the absolute home position will be assigned at the instant the marker pulse is
detected. It is recommended that the Marker Pulse be used for optimal homing repeatability.
Use Software Travel Limits: The CNC is capable of running with software travel limits that are based on position.
When enabled, this feature allows you to select Fault or Fast Decel when active. Fault operates as hardware
switches with immediate fault. Fast Decel uses the Fast Deceleration rate set on the Speeds screen to
ramp down motion.
Maximum Travel Limit: If Software Overtravels are enabled, the user is prompted for the maximum travel of the cutting
machine.
Minimum Travel Limit: If Software Overtravels are enabled, the user is prompted for the minimum travel of the cutting
machine.
Laser Compensation: Uses position readings gathered with a laser interferometer to correct the actual position of the
axes (Transverse, Dual Transverse, Rail, and Dual Gantry only).