Motion compensation, Hardware and software requirements, Overview – Hypertherm V9 Series Phoenix Rev.11 User Manual
Page 217
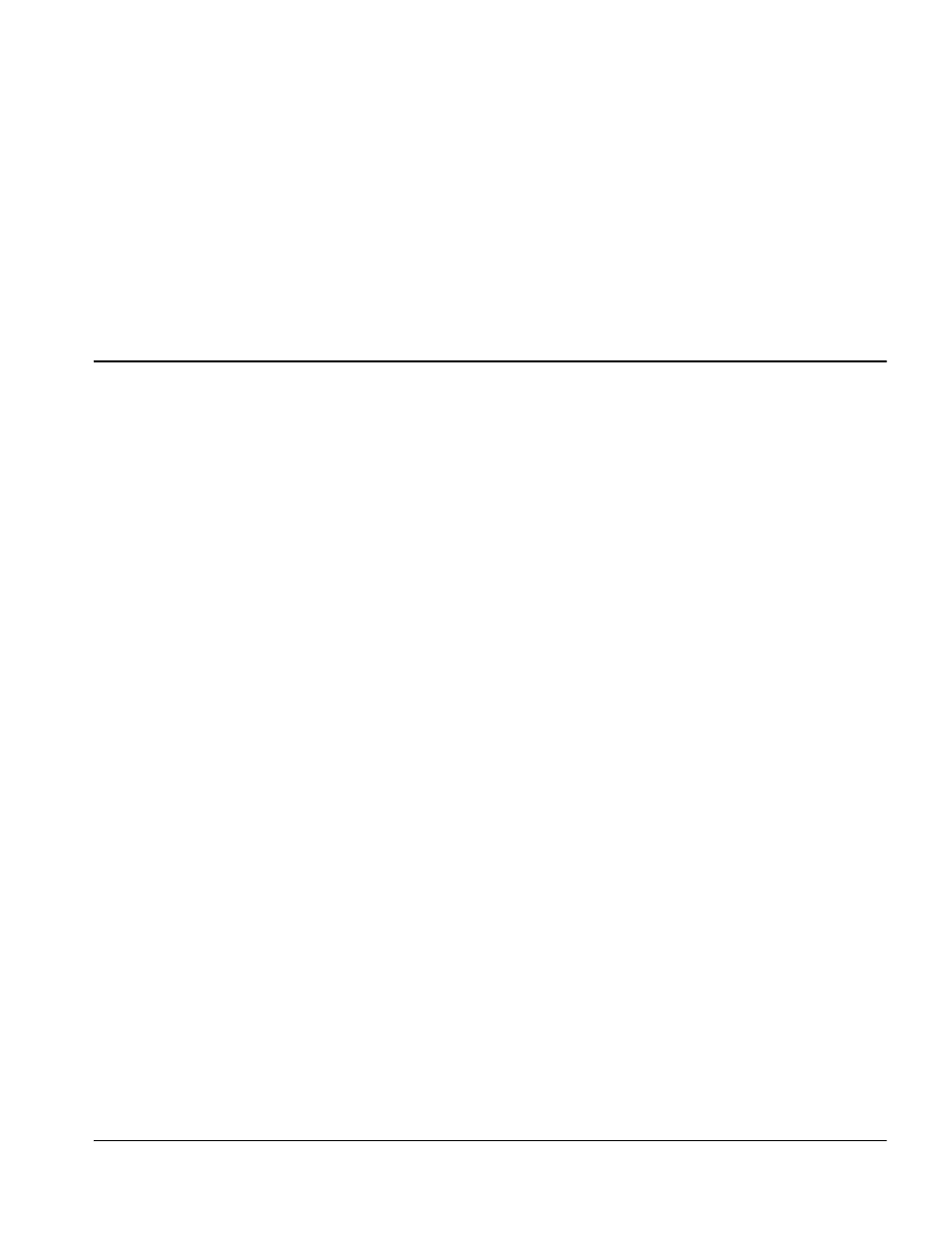
Phoenix 9.76.0 Installation and Setup Manual 806410
217
Section 10
Motion Compensation
Motion compensation is a feature of Phoenix software that improves the linear positioning accuracy of a cutting table if
there are mechanical inaccuracies on the axes. A laser interferometer records a number of positions along the rail,
transverse, and dual gantry axes. The CNC uses the data from the interferometer to compensate the commanded
position to each drive axis and reduce position errors to 0.
The compensation calculation is based on the position deviations between the CNC’s commanded position and the data
collected by the laser interferometer at the same points, or targets, along each axis.
Motion compensation does not improve the following error on an axis. The only way to reduce following error is to ensure
that system drives are tuned properly.
Hardware and Software Requirements
The following equipment and software are required to implement motion compensation:
A Hypertherm CNC
Phoenix software version 9.7 or later
Laser interferometer, such as the Renishaw XL-80
Overview
Position data from the laser interferometer are based on target locations along each axis. The CNC uses these positions
to create a part program for each axis.
Because motion compensation is based on position, it is important that all measurements and compensation start at a
consistent location. The table must be homed to the same location for each axis before laser mapping and before motion
starts.
In addition, parameters such as Home Offset, Absolute Home, Home Direction, Up Direction, and Right Direction affect
motion on the table. If any of these parameters are changed after compensation data is entered into the Phoenix software,
axes must be remapped to capture the new settings.