Calculating compensation data – Hypertherm V9 Series Phoenix Rev.11 User Manual
Page 218
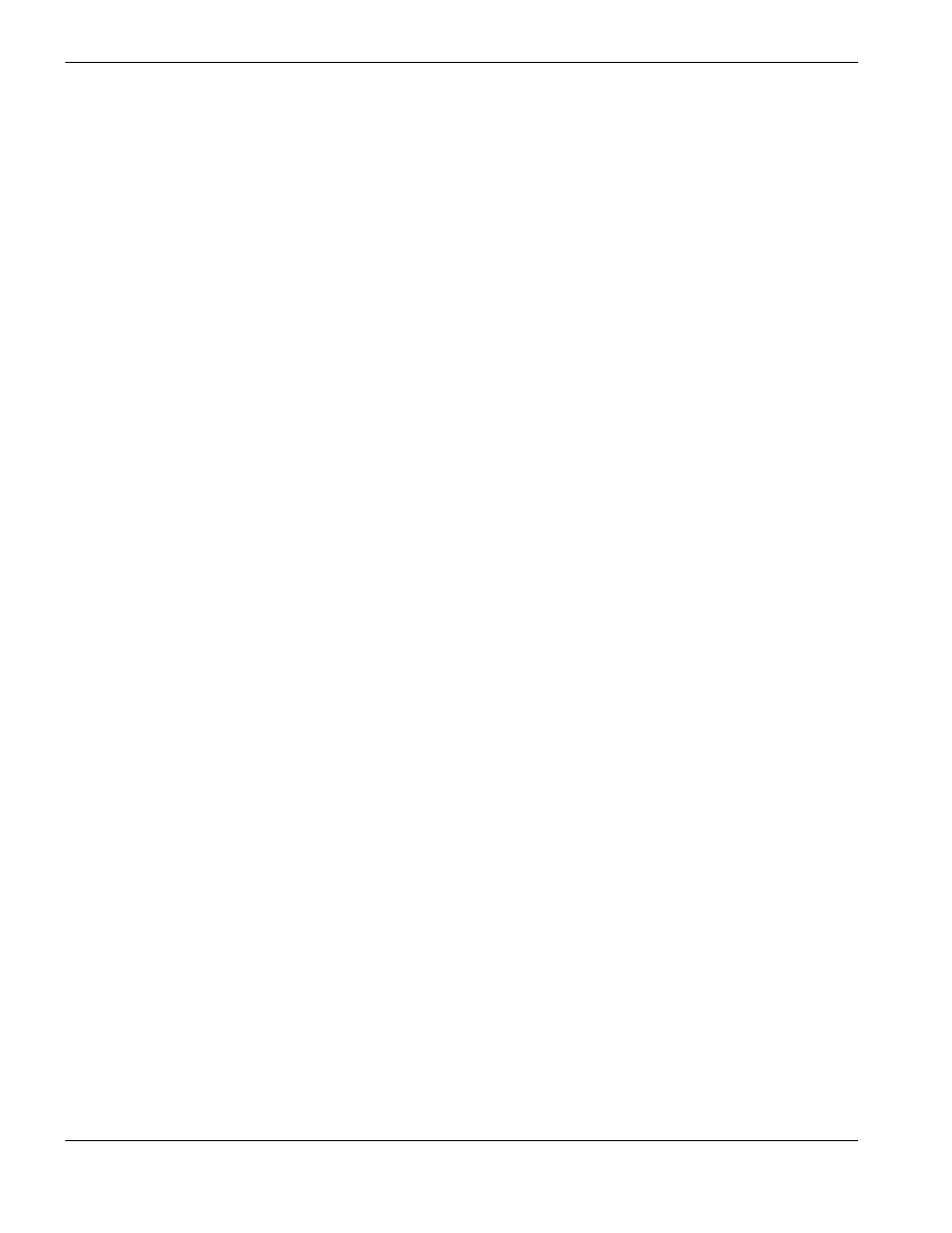
218
Phoenix 9.76.0 Installation and Setup Manual 806410
10 – Motion Compensation
Calculating Compensation Data
Phoenix determines the amount of compensation to apply to servo commands before commanding motion along an axis.
The amount of compensation that Phoenix applies is equal to the size of the position error between two targets. Phoenix
distributes this compensation along the distance between two targets
The basis for motion compensation is the assumption that the cutting system is at the same starting position as when the
axes were mapped. If the start locations are not the same, then Phoenix cannot apply motion compensation correctly. For
this reason, Homing should be enabled so that the system is homed after the system is turned on or after an error to
ensure that motion starts from the same point that was recorded in the data files.
Phoenix determines the amount of compensation to apply to the servo command before it commands motion along an
axis. Compensation is calculated and applied in the following steps:
1. The laser interferometer calculates the average position deviation at each target. The position deviation is the
difference between the target’s position along the axis and the actual position of the axis at the target.
2. The laser interferometer calculates the position deviation between two corresponding targets and records this data
in a text data file. This data file is loaded into the EDGE Pro so that Phoenix software can use it to compensate servo
commands for the position deviations.
3. Phoenix software distributes (averages) the position deviation over the length of each target distance along the axis.
4. Phoenix compensates the servo command along each target distance on the axis so that when the axis reaches each
target, the actual position error is 0. If the average position deviation is negative (the average position deviation is
short of the target position), compensation is added to servo commands. If the average position deviation is positive
(the average position deviation is past the target position), the compensation is subtracted from servo commands.
The following figure illustrates a cutting table with target points arranged along two runs. The first target is at home
position, shown as position 0,0. Each target is equally spaced at 152.4 mm (6 inches), the target distance. When the
user presses the soft key to map the axis, Phoenix creates a CNC program with traverses equal to the target distance
and pauses after each traverse.