Gain, Proportional gain, Integral gain – Hypertherm V9 Series Phoenix Rev.11 User Manual
Page 211: Derivative gain, Feedforward
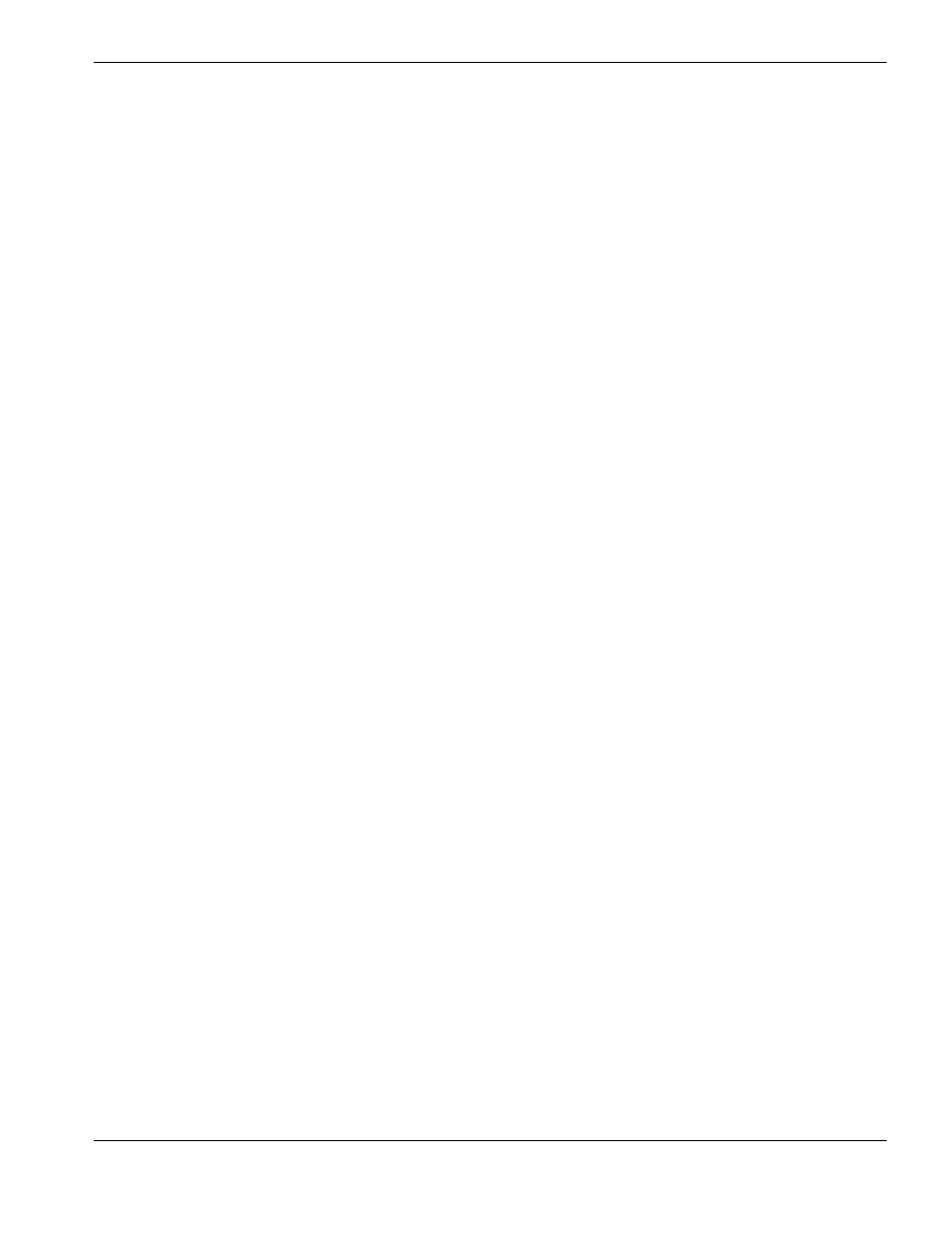
Phoenix 9.76.0 Installation and Setup Manual 806410
211
9 – Motion Control
For example:
4000 RPM Motors x 0.125 inches per rev = 500 inches per minute
Through test or calculation it is determined that the table moves 1/8 inches per revolution of the encoder.
With the maximum speed, encoder counts per inch, DAC and encoder polarities determined and entered into control
setups, a simple test of machine motion can be made in the control Drive Diagnostics screen. This test should be made
with the motors disengaged for safety. This is a basic motion test of the system and does not use gain terms or the
position loop for motion. For more information on maximum machine speeds, refer to the Setting Speeds chapter in the
Machine Setup chapter.
Gain
Proportional Gain
In a feedback control system, the error term is acted on by the control system and it alters the output. Proportional gain is
amplification of the error term. In a closed loop control system, this is proportional to the error signal. Thus, the output is
proportional gain multiplied by error.
In most systems, proportional gain is the primary tuning parameter for improving the response of the position loop.
Integral Gain
Proportional gain cannot completely eliminate error. The system can become unstable if only proportional gain is used to
eliminate error in a system. When the response of a system is satisfactory, but steady state error is excessive, the error
can be further reduced by increasing system gain only for long term accumulations of error over time. Integral gain is
sometimes used to compensate for static load disturbances like torque loading, gravity bias, and offset.
Note: Integral gain can cause instability in a system because it has a more instant effect at the beginning of a
move profile. Therefore, it is rarely used for velocity drives. However, integral gain can provide improved response
with current drives. Only small adjustments to integral gain should be made if indications of steady state error exist.
In almost all applications, this value is set to zero. Use the feed forward gain for closing following error that occurs
during a move profile.
Derivative Gain
Derivative gain responds to the rate of change of the signal and can produce corrections before the error term becomes
large, therefore it is useful in improving the transient response of a system. Since it opposes change in the controlled
output, it can produce a stabilizing effect by dampening a tendency toward oscillation. As a rule of thumb, tune by
following error to the maximum proportional gain then set derivative gain at 10% of proportional gain. Do not overdo
derivative gain as it can have a detrimental effect on the overall response of the system.
Feedforward
Feed forward “pushes” the commanded output ahead to reduce or eliminate the difference between the actual position
and the commanded position during motion, called dynamic following error. Feed forward corrects for a “lag” in the
system and has an effect similar to proportional gain. Do not make large increases in feed forward gain because it can
cause positive following error and excessive overshoot.