Hypertherm V9 Series Phoenix Rev.11 User Manual
Page 111
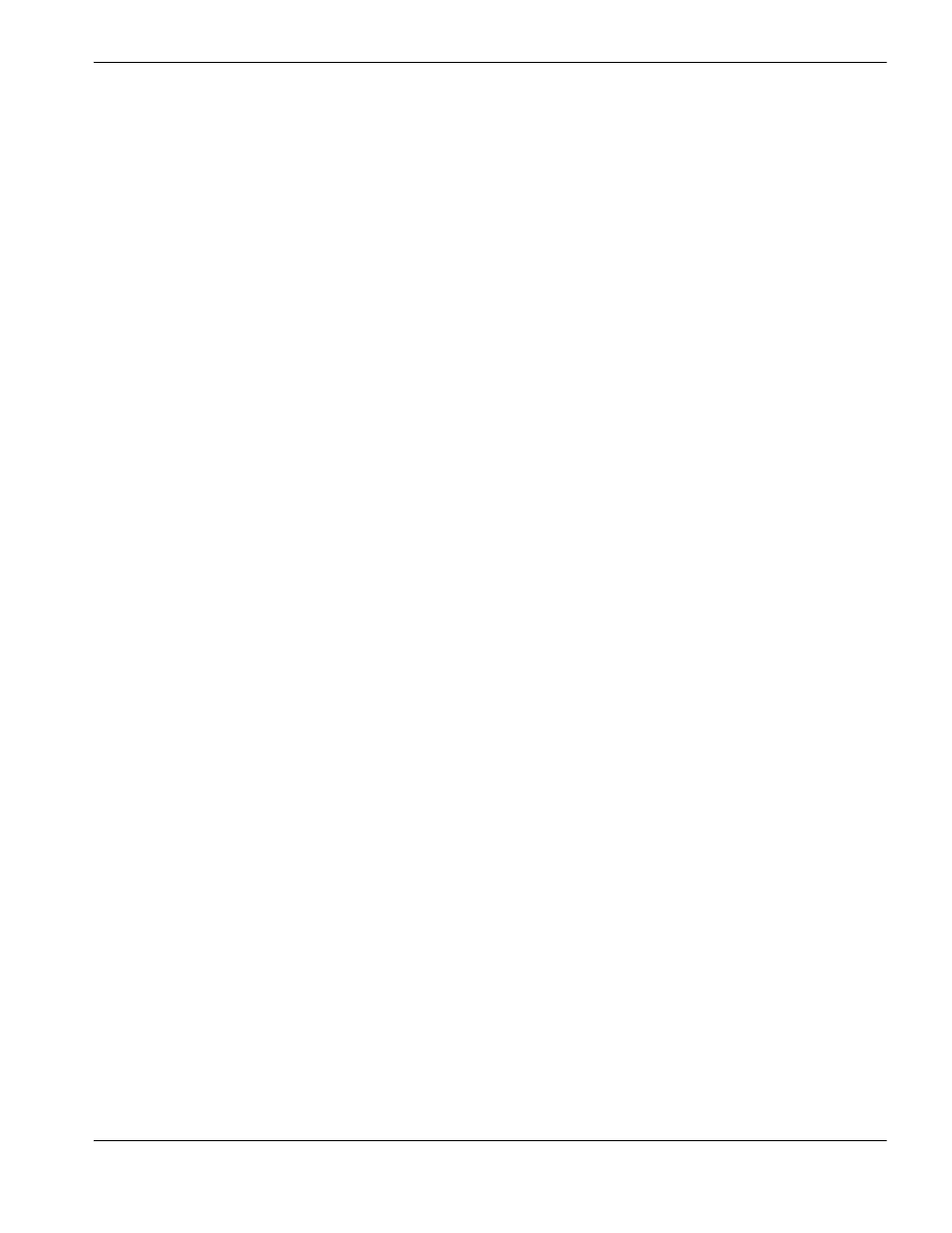
Phoenix 9.76.0 Installation and Setup Manual 806410
111
3 – Torch Height Control Axis Setup
Voltage Gain: Controls the relative responsiveness of the entire Sensor THC to maintain the programmed cut height.
The higher the value you enter, the more aggressive the response of the lifter. Voltage Gain is the only tuning
parameter that affects cutting. The other gains affect raising and lowering the torch and initial height sense
motion.
Range: 1 to 500
Recommended setting: 100; Sensor THC: 100
Servo Error Tolerance:
Servo error, also called following error, is the difference between the commanded motor position and the
actual motor position. The servo error tolerance is the upper limit of the amount of following error allowed
before the CNC faults.
The amount of servo error tolerance depends on the cutting system mechanics. Setting the servo error
tolerance too low could cause the CNC to fault repeatedly. Setting it too high could cause inaccurate
motion or mechanical harm. Set the Following Error parameter in the Watch window and observe
steady-state operation of the cutting system (some following error is normal). Set the servo error tolerance to
a value slightly higher than the steady-state following error.
Set to the Servo Error Tolerance to three times the steady-state following error.
Range: 0 to 127 mm (5 inches)
Recommended setting: Sensor THC: 5.08 mm (.2 inch)
Stall Force Tolerance: Stall force is a method of detecting the workpiece during initial height sense. Use stall force
when cutting underwater or in other conditions in which ohmic contact is not feasible. Stall force Tolerance
is the maximum amount of following error on the THC axis. The CNC starts monitoring the THC axis
following error when it reaches the Start IHS Height. The following error accumulates when the torch tip
contacts the workpiece and the lifter continues downward movement but is stopped by the workpiece.
When the following error exceeds the stall force tolerance value, the CNC knows the position of the
workpiece motion reverses, Motion stops when the amount of reverse travel of the THC equals the Transfer
Height.
Range: 0 to 127 mm (5 in.);
Recommended setting: Sensor THC: 1.27 mm (0.05 inch)
Encoder Counts per mm/inch: Sets the number of encoder counts per inch of axis travel.
Encoder counts per inch are equal to the resolution of the encoder, multiplied by the encoder revolutions per
inch or mm (based on the machine drive gearing). Enter a value that is the number of encoder counts per
inch of lifter travel. You can enter fractional encoder units and the CNC will keep track of these fractions
automatically.
Range: Positive, non-zero values up to 39379.08 counts/mm (1,000,000 counts/inch)
Recommended settings: Sensor THC: 819.2 counts/mm (20807.68 counts/inch)