Tuning procedures, Voltage controller tuning procedure – Basler Electric DGC-2020HD User Manual
Page 372
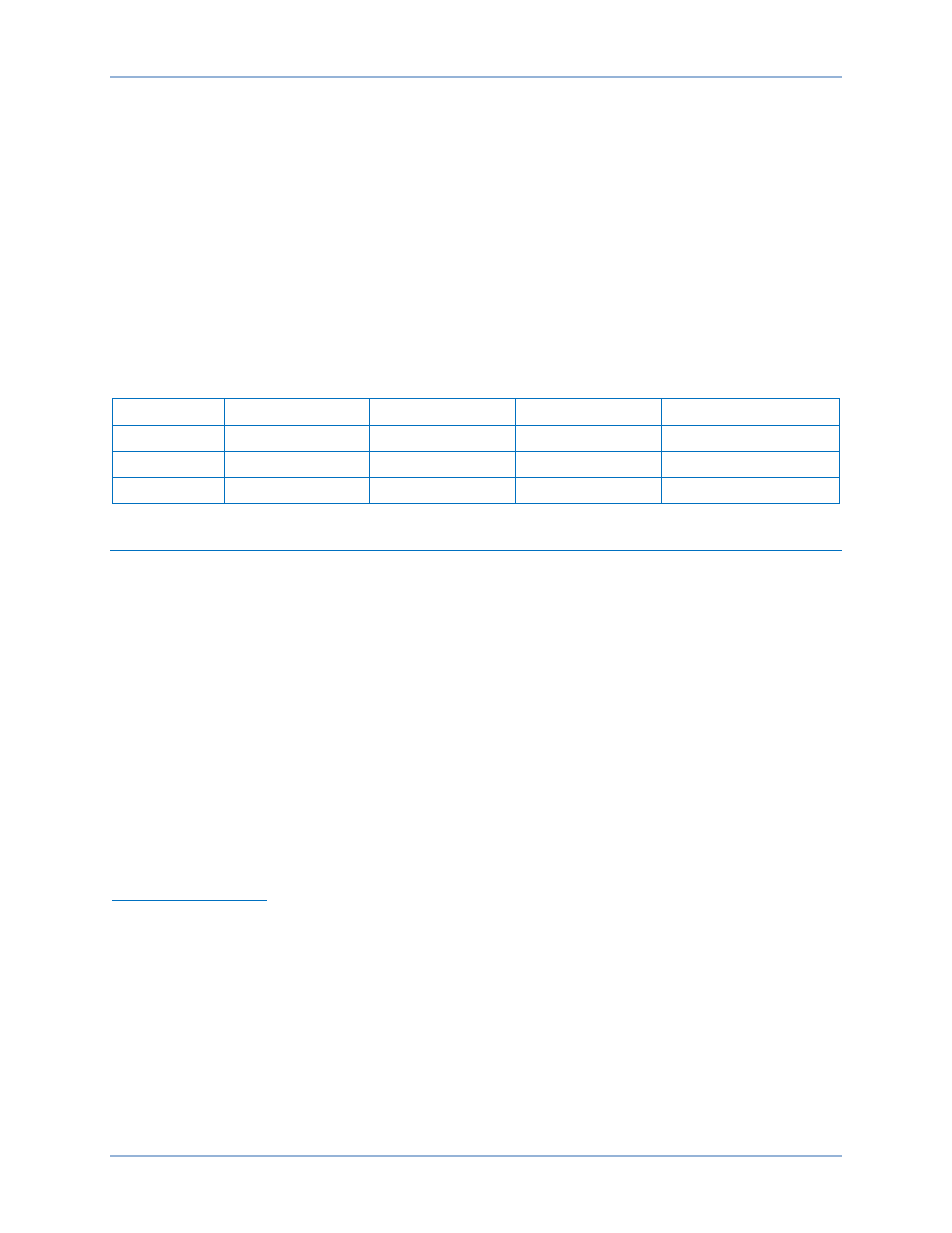
362
9469300990 Rev B
•
K
i
- Integral Gain - The contribution from the integral term is proportional to both the magnitude of
the error and the duration of the error. Some integral gain is required in order for the system to
achieve zero steady-state error. The integral term (when added to the proportional term)
accelerates the movement of the process towards setpoint and eliminates the residual steady-
state error that occurs with a proportional only controller. Larger K
i
implies steady state errors are
eliminated quicker. The trade-off is larger overshoot: any negative error integrated during
transient response must be integrated away by positive error before reaching steady state.
•
K
d
- Derivative Gain - The derivative term slows the rate of change of the controller output and is
used to reduce the magnitude of the overshoot produced by the integral component and improve
the combined controller-process stability. However, differentiation of a signal amplifies noise in
the signal and thus this term in the controller may be sensitive to noise in the error term, and can
cause a process to become unstable if the noise and the derivative gain are sufficiently large.
Larger K
d
decreases overshoot, but slows down transient response and may lead to instability.
Table 97 shows the effects of increasing parameters.
Table 97. Effects of Increasing Parameters
Parameter
Rise Time
Overshoot
Settling Time
Steady State Error
Kp
Decrease
Increase
Small Change
Decrease
Ki
Decrease
Increase
Increase
Eliminate
Kd
Small Change
Decrease
Decrease
None
Tuning Procedures
Voltage Controller Tuning Procedure
The voltage controller is tuned prior to the speed controller. Set all Kp, Ki, and Kd gains in the voltage
controller, speed controller, and kW load controller to 0. Set the Kg values to 0.1. Start the generator.
The voltage controller is only active during synchronization when the DGC-2020HD is trying to close the
generator breaker. In order to tune it, a variable AC voltage source must be connected across the bus
input of the DGC-2020HD. The generator must be started, then a breaker close sequence initiated by
applying a breaker close pulse to a discrete contact input to cause the synchronizer to become active. In
addition the Breaker Close Wait Time parameter and the Sync Fail Activation Delay should be set to a
large value such as 120 seconds or more. This will allow the voltage controller to run for a long enough
time to get meaningful response information.
If the synchronizer times out during the tuning process resulting in a synchronizer fail pre-alarm or a
breaker close failure occurs while tuning, press the Reset button on the front of the DGC-2020HD to clear
the associated pre-alarm. Then, issue a breaker open pulse to a discrete contact input. The synchronizer
is now reset, so a pulse can be applied to the breaker close discrete contact input to restart the
synchronizer. Tuning can resume at this point.
KP - Proportional Gain
Set an initial value of 1 for KP.
Each time KP is set, disturb the system by changing the voltage on the bus input of the DGC-2020HD so
that the DGC-2020HD will try to follow it. Verify that the generator’s output approaches the new value in a
stable manner. Since KI is zero at this point, there may be some small difference between the generator’s
output and the bus it is trying to follow. The important thing is that the generator’s output behaves in a
stable manner. If it is not stable, lower the value of KP and repeat.
Repeat this procedure, raising KP until the system is unstable, and then lower it to half the value where
instability is first attained.
If it is not possible to obtain stable voltage operation, it may be necessary to reduce the control gains in
the voltage regulator that has its analog bias input driven by the DGC-2020HD.
Tuning PID Settings
DGC-2020HD